石油天然气站场管道及设备外防腐层检测的重要性
在石油天然气行业中,站场管道及设备的运行安全直接关系到能源传输效率和环境保护。由于管道长期暴露在复杂的土壤、大气及化学介质环境中,外防腐层易受物理损伤、老化或腐蚀影响。一旦防腐层失效,可能导致管道泄漏、设备损坏甚至安全事故。据统计,80%以上的管道失效事件与防腐层缺陷相关。因此,定期开展外防腐层系统性检测,是保障设施完整性、延长使用寿命的核心技术手段。
外防腐层检测的核心项目
1. 防腐层外观检查
通过目视或光学仪器(如内窥镜、无人机巡检)检查防腐层表面是否存在裂纹、鼓包、剥离、机械损伤等问题。重点关注焊缝区域、弯头部位和埋地管段,记录缺陷位置并评估损伤程度。需结合标准(如SY/T 0063)判断是否符合防腐层连续性和均匀性要求。
2. 防腐层厚度检测
使用磁感应测厚仪(磁性基材)或超声波测厚仪(非金属基材),按照GB/T 4956标准对防腐层进行多点抽样测量。要求厚度偏差不超过设计值的±10%,重点核查阴保电位异常区域的涂层厚度是否符合规范。
3. 附着力测试
通过划格试验(ASTM D3359)或拉拔试验(ISO 4624)评估防腐层与基材的结合强度。拉拔强度需达到≥5MPa(环氧类涂层)或≥3MPa(沥青类涂层),划格法脱落面积应小于5%。对于多层复合涂层需分层测试。
4. 破损点与阴极保护匹配性检测
采用直流电位梯度法(DCVG)或交流电流衰减法(ACCA)定位防腐层破损点,同步测量管地电位(CIPS)验证阴极保护系统的有效性。要求保护电位维持在-850mV~-1200mV(CSE参比电极),破损点修复后需复测阴保电位分布均匀性。
5. 材料性能老化评估
通过实验室分析检测防腐层材料的玻璃化转变温度(DSC)、抗冲击强度(ASTM G14)及耐化学介质性能(浸泡试验)。对服役超过10年的防腐层,需增加差示扫描量热法(DSC)检测热稳定性,评估其剩余使用寿命。
综合检测技术应用
现代检测通常采用多技术融合方案:红外热成像(TIR)快速发现分层缺陷,脉冲涡流(PEC)检测埋地管段,结合地理信息系统(GIS)建立防腐层健康档案。建议每3年实施全面检测,高风险区域加密至每年1次,检测数据需接入完整性管理平台实现动态预警。
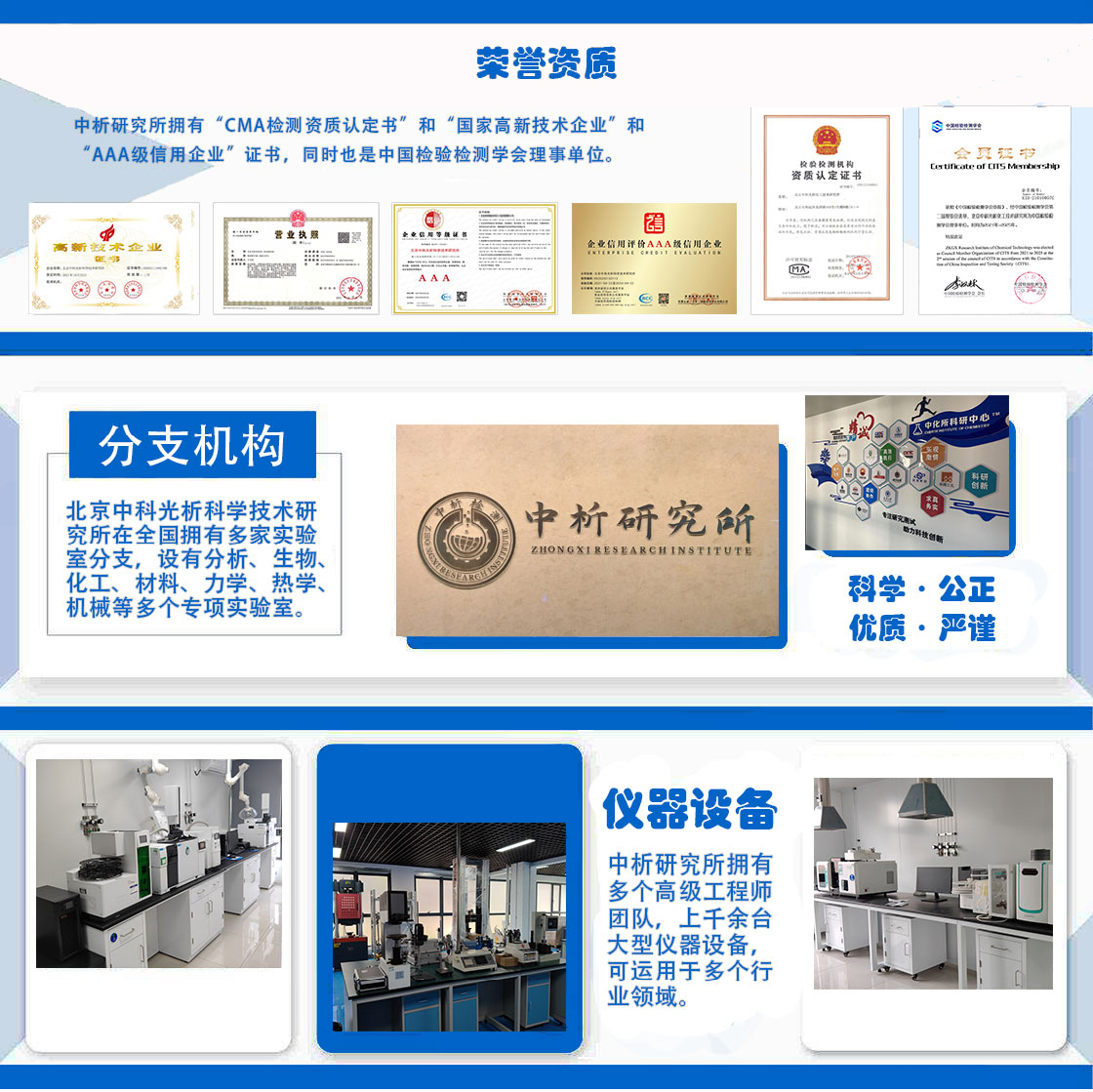
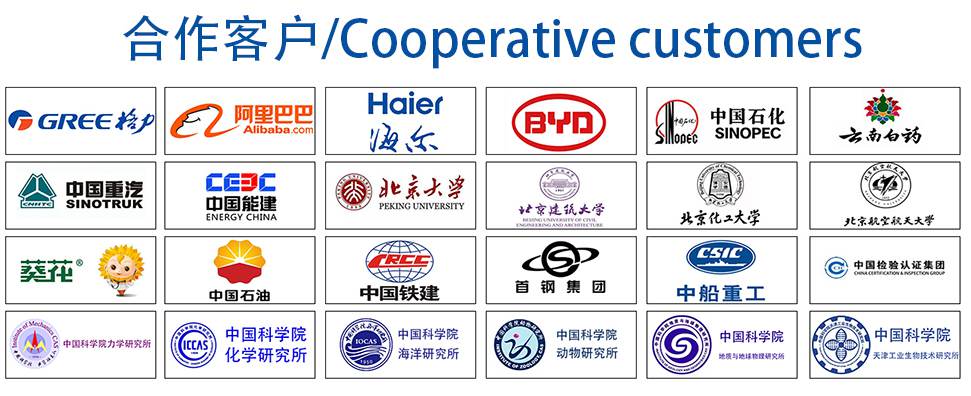