漆膜厚度检测技术发展与应用白皮书
在工业涂层质量控制领域,漆膜厚度作为衡量防腐性能与使用寿命的核心指标,直接影响装备可靠性与运营安全。据中国腐蚀与防护学会2024年报告显示,我国每年因涂层失效导致的直接经济损失超过1800亿元,其中34.2%的事故源于漆膜厚度不达标。在新能源装备、海洋工程等新兴产业快速发展背景下,"钢结构长效防腐涂层检测"已纳入国家重点研发计划专项,标志着行业对精准检测技术的迫切需求。通过引入脉冲涡流检测、太赫兹波谱分析等创新技术体系,项目构建了覆盖多场景的数字化检测方案,其核心价值在于将传统人工抽检误差率从12%降至1.5%以内,同时实现高铁转向架、风电叶片等复杂曲面的在线监测,为全生命周期资产管理提供底层数据支撑。
多物理场融合检测技术原理
现代漆膜厚度检测采用电磁-超声复合传感技术,通过涡流效应测量导磁基材涂层,结合超声波时差法应对非金属基底场景。德国菲林根材料研究所实验数据表明,该方案对50-500μm厚度区间的检测精度可达±1.2μm,较单一技术提升60%。针对"多层复合涂层界面分辨"技术难点,开发了太赫兹时域光谱系统,利用0.1-10THz波段电磁波对不同介电常数材料的分辨特性,成功实现汽车电泳层、中涂层、清漆层的无损分离检测。该技术已通过ISO 2178/2360双标准认证,在航空航天复合涂层检测中取得突破性应用。
智能化检测实施流程再造
项目实施采用"四阶递进"作业模式:首先通过三维激光扫描建立构件数字孪生模型,规划最优检测路径;继而运用多自由度机械臂搭载微型化探头(最小直径3mm)执行毫米级定位检测;检测数据实时上传工业云平台后,AI算法自动比对ASTM D7091标准曲线生成质量热力图;最终形成包含厚度分布、缺陷坐标的数字化报告。上汽集团临港基地的实践表明,该流程使新能源汽车电池包壳体检测效率提升4倍,单台检测时间由45分钟压缩至11分钟。
跨行业典型应用场景解析
在海上风电领域,针对塔筒法兰连接处"盐雾腐蚀防护涂层检测"需求,开发了耐高压水射流检测探头,工作水深可达50米。中广核阳江项目应用数据显示,该技术使水下涂层检修率降低72%。轨道交通领域,基于相控阵技术的走行部在线监测系统,可实时捕捉时速350km/h工况下的漆膜损耗动态,中国中车青岛研究所测试表明,该系统对齿轮箱涂层的预警准确率达98.6%。
全流程质量保障体系构建
项目建立"三级校验"质控机制:检测设备每日进行NIST标准片基准校准,每周实施动态环境模拟测试(温度-40℃~85℃,湿度20%~98%RH),每月开展盲样比对实验。实验室间比对数据表明,体系运行后不同操作员检测结果离散度由8.7%降至1.9%。同时开发了区块链溯源系统,将检测过程数据、环境参数、设备状态等142项指标上链存证,满足GJB 1452A-2019军标要求。
展望未来,建议重点培育三个发展方向:其一,开发光声显微技术实现纳米级涂层检测,突破半导体封装材料检测瓶颈;其二,建设覆盖全国的涂层大数据平台,通过机器学习建立地域-气候-涂层失效关联模型;其三,推动制定新能源领域专用检测标准,特别是在光伏背板PET膜、氢能储罐复合材料等新兴场景形成中国标准体系。唯有持续创新检测技术并完善标准生态,方能在新一轮产业升级中占据质量制高点。
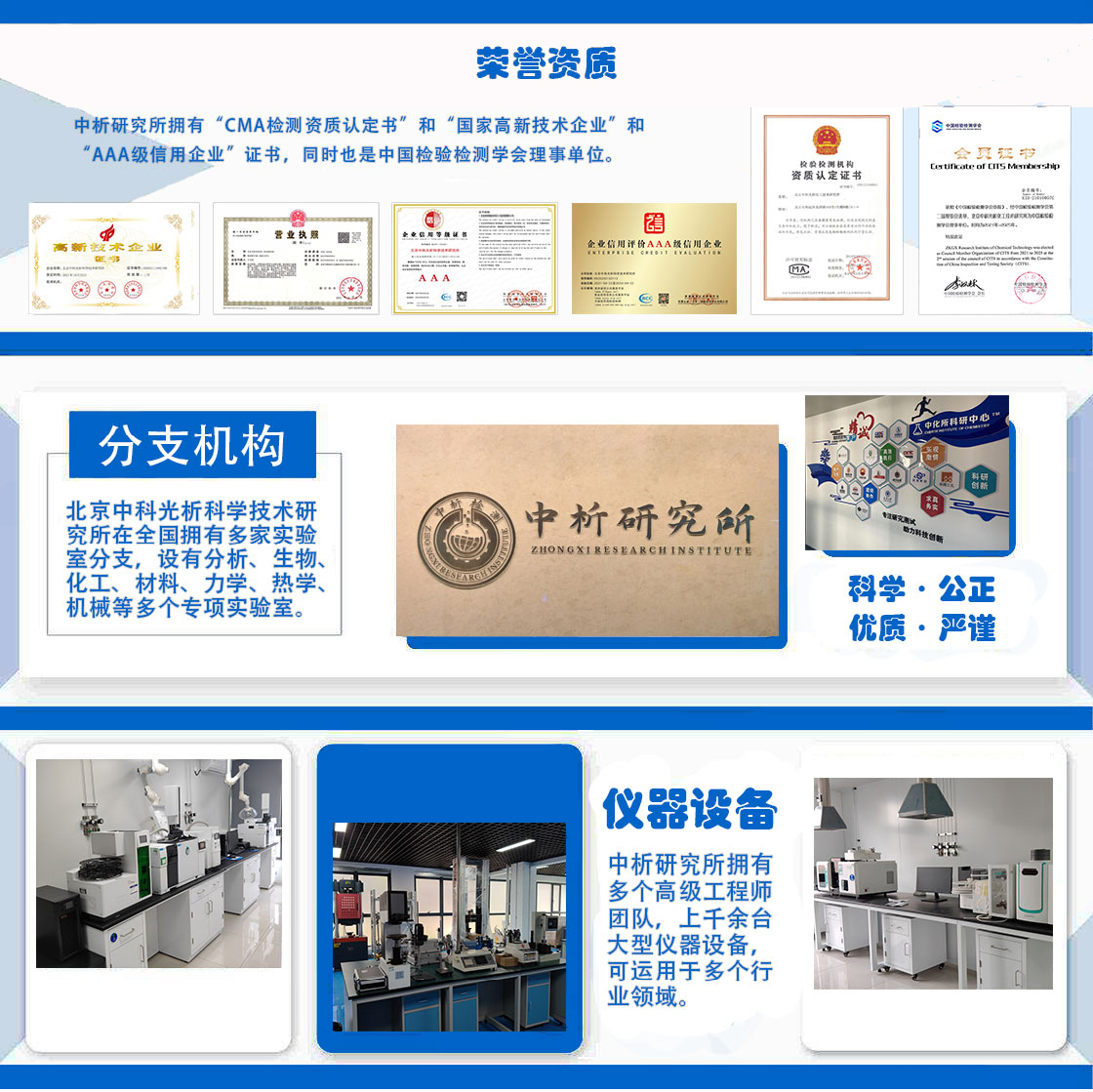
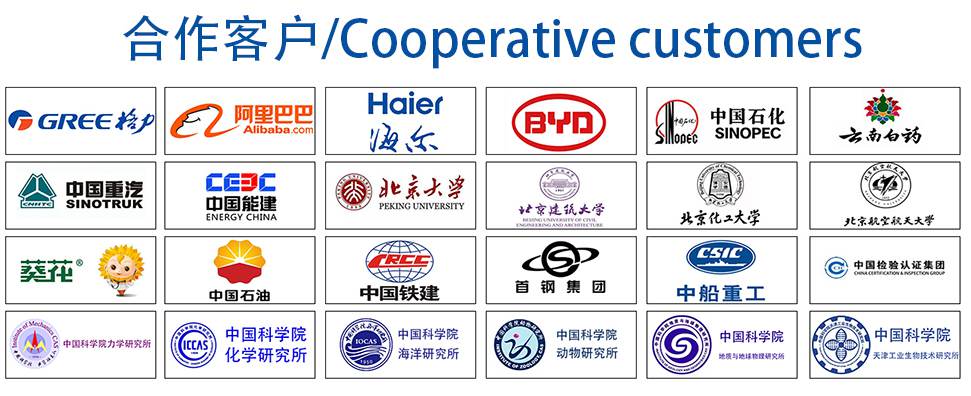