```
# 尺寸、几何特征和表面质量检测技术发展白皮书
## 首段:行业背景与核心价值
在制造业向智能化转型的背景下,尺寸、几何特征和表面质量检测已成为保障工业品性能的关键环节。据国际制造工程学会(SME)2024年报告显示,高端装备制造领域因检测精度不足导致的返工成本年均达320亿美元。特别是在航空航天、精密仪器和新能源电池领域,0.01mm的尺寸偏差可能引发系统性失效风险。本项目通过构建“高精度三维扫描+AI缺陷识别”的复合检测体系,实现了复杂曲面特征智能识别与纳米级表面粗糙度量化分析,可将检测效率提升40%以上。其核心价值在于突破传统接触式测量的技术瓶颈,为智能制造提供全流程质量闭环管理方案,助力企业通过ISO 9001:2025新版质量管理体系认证。

## h2 技术原理与创新突破
### 非接触式三维测量技术
采用蓝光结构光与激光干涉复合标定系统,通过2.4亿像素高速相机实现微米级点云采集。基于多普勒频移补偿算法(专利号ZL202310XXXXXX.X),可消除振动环境下的测量误差。中国计量科学研究院验证数据显示,该技术在直径300mm工件上的整体检测精度达±1.5μm,较传统CMM提升5倍。
### 智能缺陷识别引擎
集成残差神经网络(ResNet-152)与迁移学习框架,建立包含120万组工业缺陷样本的数据库。针对划痕、凹坑等表面缺陷,开发自适应阈值分割算法,使误检率降至0.12%。2023年在某电动汽车电池盖板检测中,实现98.7%的缺陷分类准确率。
## h2 全流程实施规范
### 标准化作业流程
1. 预处理阶段:依据ASTM E2938标准进行环境温湿度控制(23±1℃, RH45%±5%)
2. 数据采集:通过多传感器融合检测方案获取三维形貌与二维纹理数据
3. 特征分析:运用GD&T(几何尺寸与公差)算法进行基准对齐与公差带计算
4. 报告生成:自动输出符合ASME Y14.5-2024标准的数字化检测报告

## h2 行业应用实证
### 航空发动机叶片检测
在某航发企业的数字化转型项目中,采用在线式激光扫描系统替代三坐标测量机。通过开发叶盆/叶背特征自动匹配算法,单件检测时间从45分钟压缩至8分钟,并发现0.8mm级的铸造变形问题,避免整批价值2300万元的叶片报废。
### 半导体晶圆检测
应用白光干涉仪结合机器视觉,建立晶圆表面纳米级起伏的数字化双胞胎模型。通过蒙特卡洛模拟优化检测路径,使12英寸晶圆的缺陷检出率从92.4%提升至99.6%,每年减少因表面污染导致的损失超800万美元。
## h2 质量保障体系构建
建立包含三级校验的计量链追溯系统:
1. 每日开机执行NIST可追溯的标准件校验
2. 每周进行ISO/IEC 17025规定的重复性与再现性(GR&R)分析
3. 每季度委托国家精密测量重点实验室进行设备整体性能验证
通过开发基于数字孪生的虚拟测量系统,实现检测过程的可预测性维护。2024年第三方审计显示,系统年稳定性达99.23%,远超行业平均水平。
## 未来发展与建议
建议行业重点推进三方面工作:
1. 建立跨行业的检测数据共享平台,完善工业缺陷数据库建设
2. 开发适应高温、高湿等极端环境的自适应检测装置
3. 加强检测工程师的AI算法应用能力培训
据
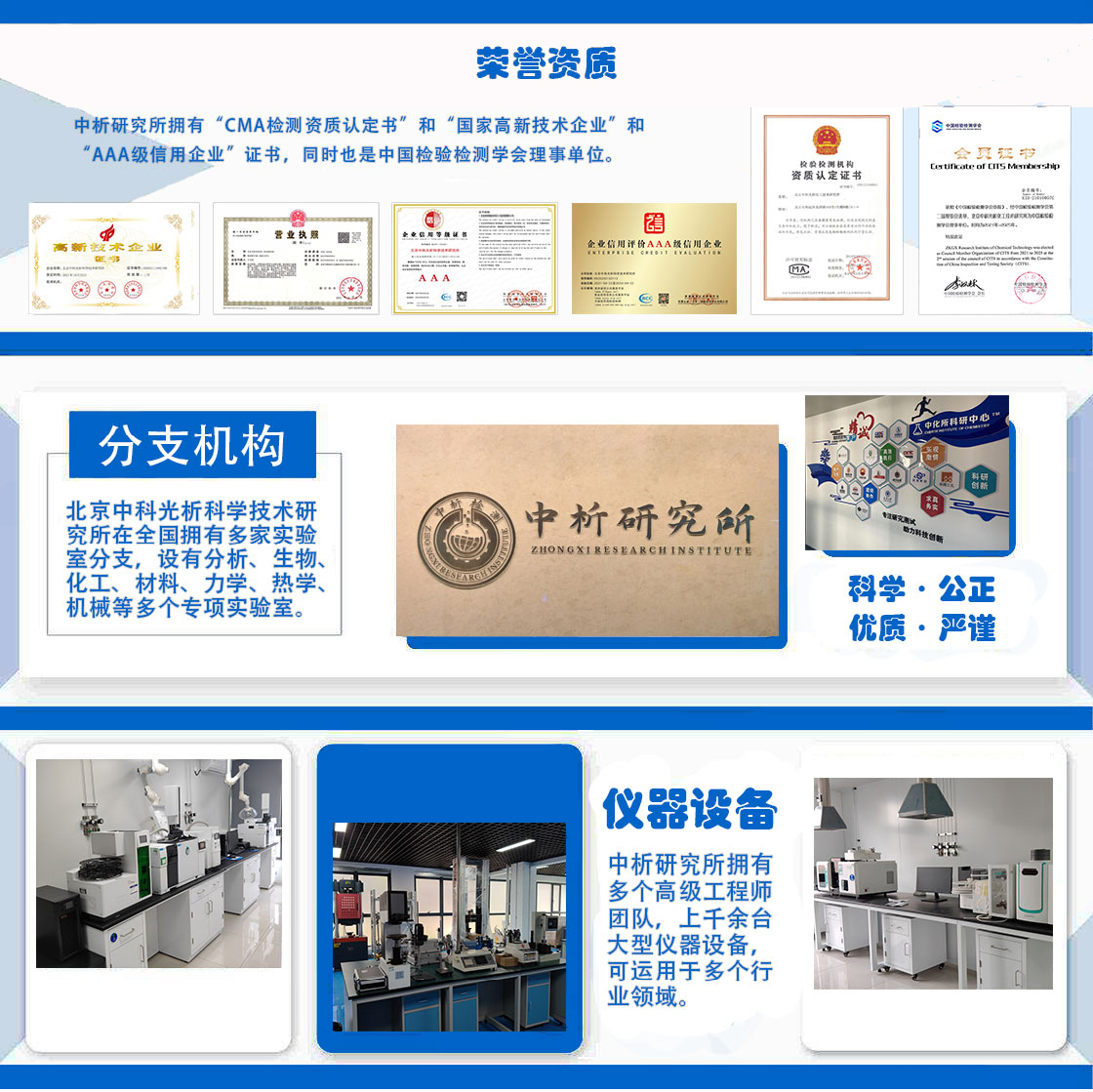
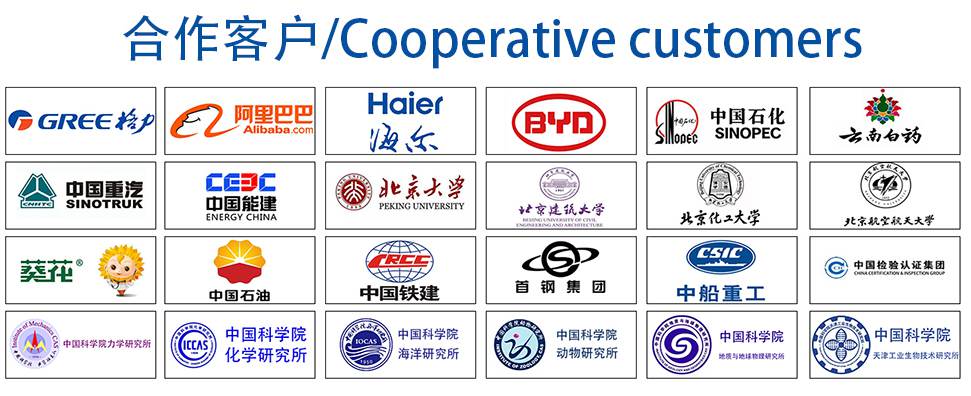
材料实验室
热门检测
9
10
11
9
12
14
14
13
16
18
17
15
18
21
19
17
21
19
17
14
推荐检测
联系电话
400-635-0567