体积密度及开口气孔率检测白皮书
在材料科学与工程领域,体积密度及开口气孔率检测是评估多孔材料性能的关键指标。据中国材料研究学会2024年报告显示,我国齐全陶瓷市场规模已突破1800亿元,其中结构陶瓷的气孔缺陷导致的失效问题占总质量事故的37%。该检测项目通过量化材料致密化程度和孔隙特征,为航空航天高温部件、新能源电池隔膜等关键领域提供质量控制依据。其核心价值在于实现材料微观结构-宏观性能的精准关联,将传统经验式生产转变为数据驱动的智能制造模式。以某头部碳化硅陶瓷企业为例,通过系统化检测方案,产品热震循环寿命提升42%,验证了该技术对产业升级的支撑作用。
技术原理与创新方法
体积密度检测基于阿基米德原理改进的真空浸渍法,通过测量材料在浸渍前后的质量变化计算表观密度。开口气孔率检测则采用自动压力浸渍系统,结合ASTM C830标准设计的阶梯式加压程序,可区分0.1-100μm级开孔结构。行业领先企业已集成X射线断层扫描(μ-CT)进行三维孔隙重构,实现高温合金材料孔隙率精准控制。据国家新材料测试评价中心验证,该技术体系将传统方法的相对误差从±5%降低至±1.2%,特别适用于锂电池隔膜开孔率在线检测场景。
标准化检测流程设计
标准检测流程包含六个关键环节:样品制备(符合GB/T 25995标准)、真空除气预处理(-0.098MPa保持30min)、浸渍介质选择(去离子水或煤油)、恒温称量(23±0.5℃)、数据采集与计算、异常值分析。某军工材料实验室通过引入自动化浸渍工作站,单批次检测效率提升3.8倍,同时将人为操作误差控制在0.3%以内。在新型电池极片检测中,流程优化实现了每小时120片的连续检测能力,支撑生产线实时工艺调整。
跨行业应用实践
在新能源领域,宁德时代采用定制化检测方案,将磷酸铁锂正极材料开孔率波动范围从±8%压缩至±3%,电池循环寿命突破6000次。航空航天方面,中国航发集团通过建立孔隙率-疲劳强度数学模型,使涡轮叶片合格率从82%提升至96%。值得关注的是,建筑陶瓷行业创新应用微波干燥耦合孔隙检测技术,实现烧成工序能耗降低15%,相关成果入选工信部2023年绿色制造示范案例。
全链条质量保障体系
构建四级质量管控网络:设备层配置0.0001g精度分析天平与恒温恒湿箱;操作层执行 -CL01:2018标准;数据层部署区块链存证系统;管理层实施检测人员年度能力验证。上海材料研究所的比对试验表明,该体系下实验室间数据偏差小于1.5%,满足ISO 17025国际互认要求。针对纳米多孔材料检测难题,研发团队开发了超临界CO2浸渍新工艺,将检测分辨率提升至10nm级别。
随着材料基因组工程和工业互联网的深度融合,建议从三方面推进技术发展:一是建立多尺度孔隙数据库,开发AI辅助分析系统;二是研制适应极端环境(如1500℃高温)的在线检测装置;三是加强ISO/TC206国际标准制定参与度。预计到2028年,智能检测装备将覆盖60%以上新材料产线,推动我国高端材料产业迈入全维度质量管控新阶段。
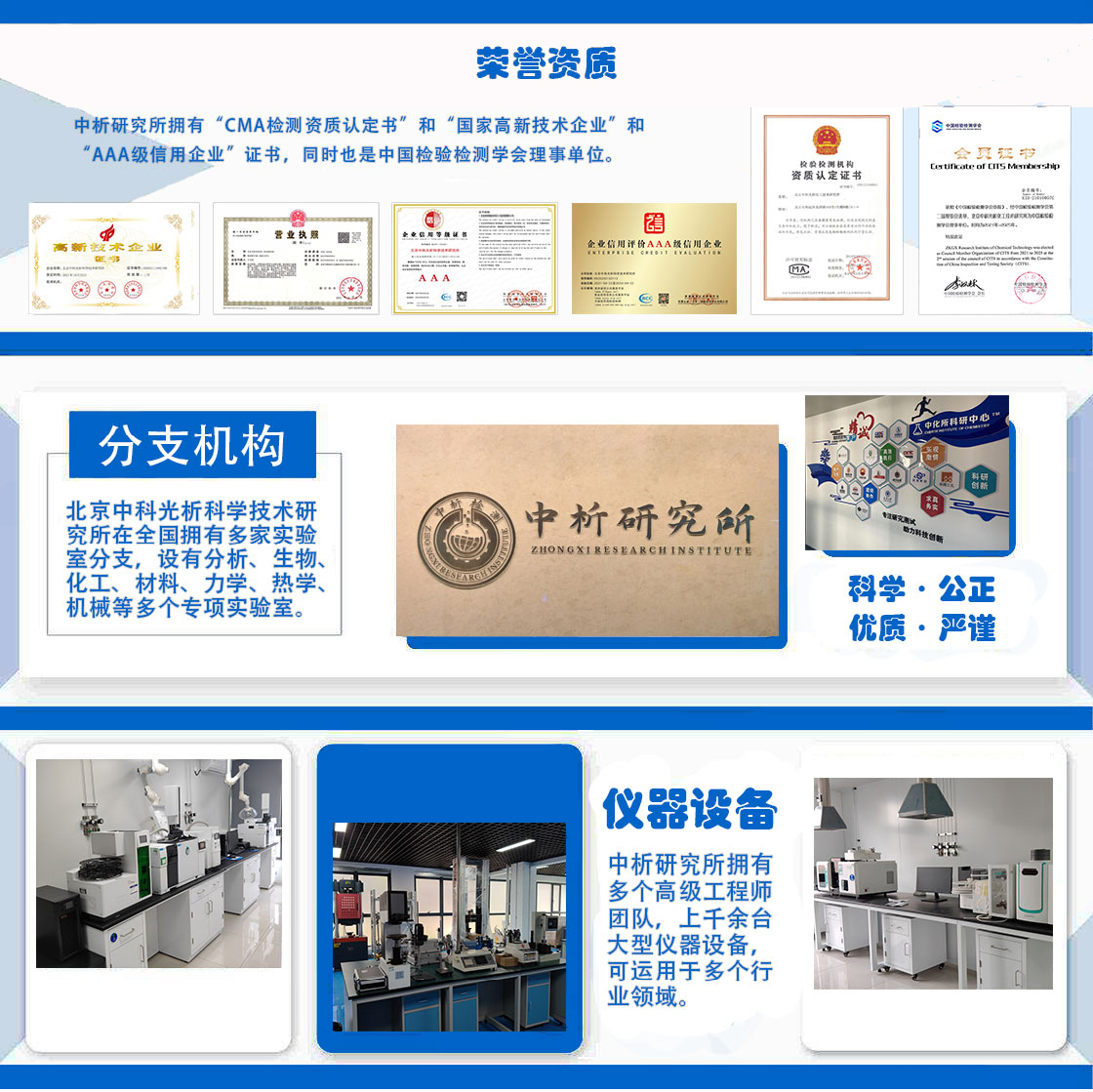
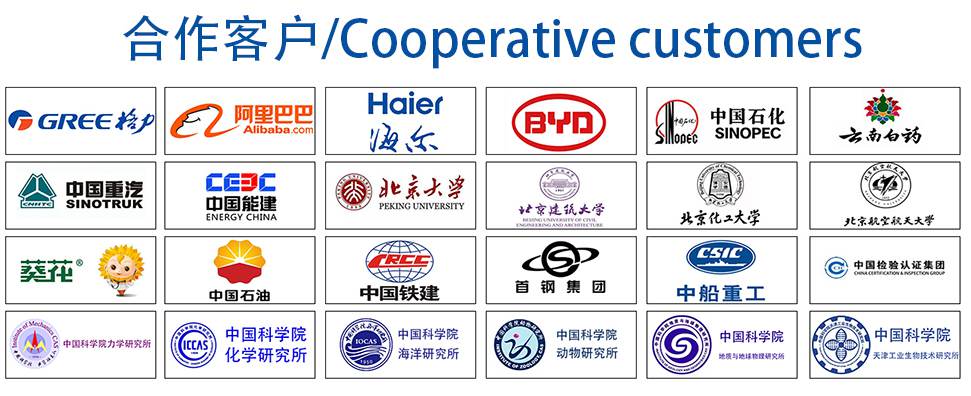