耐酸碱性能检测
随着化工、环保、新能源等行业的快速发展,材料在极端化学环境下的耐受性已成为产品质量控制的核心指标。据中国腐蚀与防护学会2024年数据显示,我国每年因材料腐蚀造成的经济损失达2.8万亿元,其中60%与酸碱介质相关。在此背景下,耐酸碱性能检测作为材料可靠性评估的关键环节,直接关系到设备使用寿命、安全生产和环境保护。通过系统性验证材料在pH值0-14范围内的化学稳定性,可为航空航天燃料储罐、半导体蚀刻设备、锂电池电解槽等场景提供科学选材依据,其核心价值在于降低设备失效风险,延长关键部件服役周期,同时推动新型耐蚀材料的研发进程。
检测技术原理与标准化体系
耐酸碱性能检测基于材料与环境介质的交互作用机制,主要采用浸泡法、电化学测试和微观形貌分析三重验证体系。其中,ASTM G31标准规定的恒温浸泡法可模拟长期接触工况,通过质量损失率计算腐蚀速率;电化学阻抗谱(EIS)则能动态监测材料表面钝化膜的形成与破坏过程,适用于评估酸性介质抗性验证场景。值得注意的是,国际标准化组织(ISO)2023年新发布的ISO 22479标准,已将X射线光电子能谱(XPS)纳入碱性环境材料衰减分析的必备技术,可精确测定材料表面元素价态变化。
全周期检测实施流程
典型检测流程涵盖五个阶段:首先根据GB/T 10124规范制备标准试样,随后配置目标酸碱溶液并建立温度-浓度梯度控制模型。实验阶段采用交叉验证方式,在72小时连续浸泡后同步进行电化学工作站实时监测。以某半导体企业晶圆蚀刻机内衬检测为例,通过模拟98%浓硫酸与40%氢氧化钠交替工况,结合SEM扫描电镜观测晶界腐蚀深度,最终确定钽钨合金的耐蚀性能优于传统哈氏合金,使设备维护周期从3个月延长至18个月。
行业典型应用场景
在新能源领域,锂电隔膜耐电解液腐蚀测试已成为行业强制认证项目。据高工锂电研究院2024年报告,采用改进型氢氟酸耐受性检测方案后,TOP10电池企业的隔膜孔隙率稳定性提升23%。环保工程中,垃圾渗滤液处理设备的316L不锈钢部件需通过氯化物酸性介质抗性验证,某省级固废中心通过引入动态冲刷腐蚀试验系统,成功将反应罐使用寿命从5年提升至8年。此外,海洋工程领域应用ISO 11306标准的模拟海水酸化实验,为南海油气平台选用了抗点蚀性能优异的双相不锈钢材料。
质量保障与认证体系
为确保检测结果公信力, 认证实验室须执行严格的质量控制程序。具体包括:使用NIST标准物质校准PH计,每批次试验设置参照样进行数据漂移校正,以及采用区块链技术实现检测数据全程追溯。某化工巨头在2023年供应商审核中发现,通过ILAC互认实验室出具的耐氢氟酸检测报告,其材料筛选准确率比普通实验室高41%。此外,数字化检测平台的应用实现了测试参数的智能优化,如某检测机构开发的AI模型可将复杂工况模拟实验设计效率提升65%。
技术发展趋势与建议
面向未来,耐酸碱检测技术将向智能化、场景化方向演进。建议行业重点发展三方面:一是建立极端浓度梯度下的材料失效预测模型,二是推广微型化原位检测装置在生产线上的应用,三是制定适用于新型生物基材料的绿色耐蚀评价标准。同时,应加强跨行业数据共享,将腐蚀大数据纳入工业互联网平台,为设备全生命周期管理提供支撑。据中国材料研究学会预测,到2028年,集成机器学习算法的智能腐蚀监测系统将覆盖30%以上重点工业场景,推动我国耐蚀材料产业迈入国际领先行列。
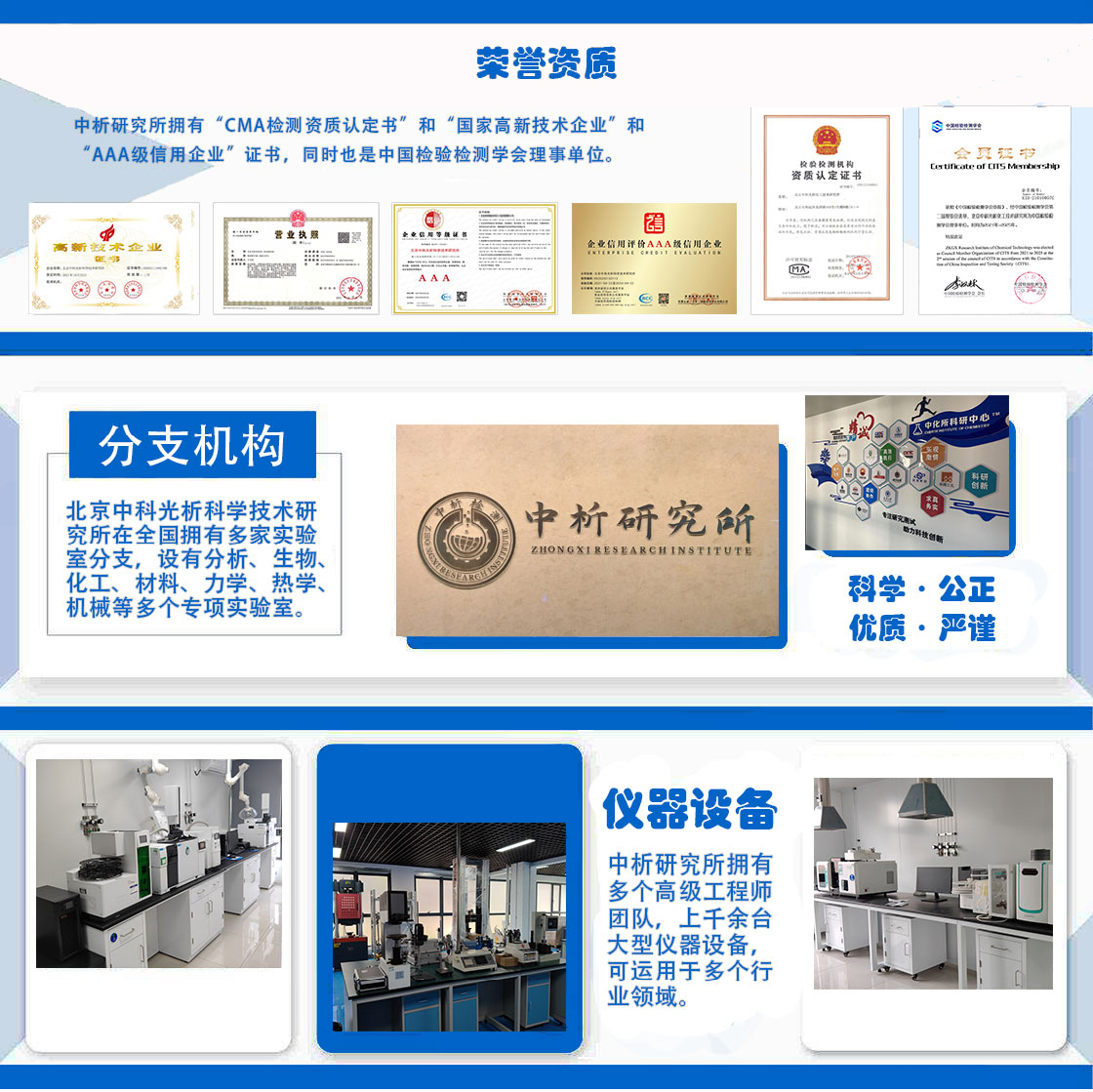
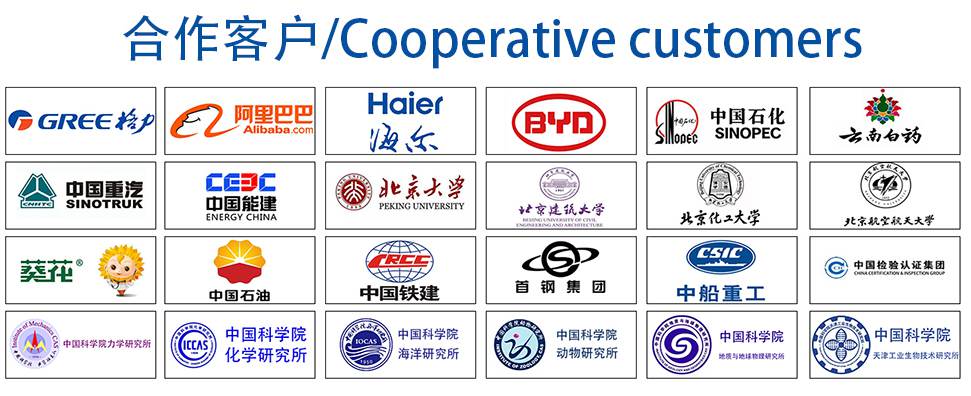