电化学与光谱联合分析技术原理
现代表面腐蚀检测技术融合了电化学阻抗谱(EIS)与激光诱导击穿光谱(LIBS)双模态分析方法。EIS技术通过测量金属/电解质界面阻抗变化(频率范围0.01Hz-100kHz),可精确解析钝化膜生长动力学参数,检测灵敏度达到纳米级膜厚变化。LIBS技术则以1064nm脉冲激光激发材料表面等离子体,通过特征谱线(如Fe I 358.12nm)强度变化实现元素迁移量测定,检测限低至0.01wt%。两种技术联用形成互补验证机制,既规避了单一方法的环境干扰问题,又将腐蚀速率测量误差控制在±5%以内(ASTM G59标准验证数据)。
标准化检测实施流程
项目执行严格遵循ISO 9223环境腐蚀性分级标准,形成五阶段作业流程:首齐全行表面预处理(包括机械打磨至Ra0.8μm、丙酮超声清洗),随后部署多探头阵列式传感器网络(间距≤50mm),通过无线传输模块实时采集电位/电流密度数据。第三阶段利用有限元算法构建三维腐蚀云图,智能识别局部腐蚀热点区域(精度±0.5mm)。第四阶段对高风险区域进行微区取样,采用扫描电镜(SEM)观测裂纹扩展形貌。最终生成包含腐蚀速率预测(mm/a)、剩余寿命评估等20项参数的数字化检测报告,整个过程耗时较传统方法缩短60%。
海上风电装备检测实践
在广东阳江海上风电场示范项目中,针对塔架法兰连接处盐雾腐蚀问题,团队部署了金属材料腐蚀在线监测系统。系统集成恒电位仪(Gamry Ref600+)与无线传感器节点,通过机器学习算法建立Cl⁻浓度(检测范围0-6mol/L)与腐蚀深度的非线性模型。连续12个月监测数据显示,法兰过渡区最大点蚀深度达1.2mm,超过设计安全阈值。项目组据此调整了阴极保护电位(从-850mV调整至-950mV vs Ag/AgCl),使年腐蚀速率从0.25mm/a降至0.08mm/a(DNV-RP-B401验证数据),成功延长设备大修周期至8年。
全链条质量保障体系
为确保检测结果可靠性,项目构建了三级质控体系:实验阶段采用标准样块(NIST SRM 1155)进行仪器校准,确保开路电位测量偏差≤±2mV;现场阶段实施双人平行检测(相对误差<5%),并通过区块链技术固化原始数据;分析阶段引入蒙特卡洛仿真(迭代次数≥10^4次)评估测量不确定度。同时建立包含37项指标的海洋环境长效防腐评估模型,该模型在青岛海洋腐蚀研究所验证中,对碳钢构件寿命预测准确度达到92.3%(置信区间95%)。
## 技术展望与发展建议 随着工业物联网与材料基因工程的发展,建议从三方面深化技术应用:其一,开发多物理场耦合的腐蚀预测数字孪生系统,整合流体力学、电化学与环境参数;其二,推动微型化检测设备研发(目标体积<50cm³),实现狭小空间原位检测;其三,建立基于区块链的腐蚀大数据共享平台,构建覆盖全行业的金属材料失效案例库。预计到2030年,智能腐蚀检测技术将推动工业设备维护模式从"定期检修"向"状态维护"全面转型,为制造业高质量发展提供关键技术支撑。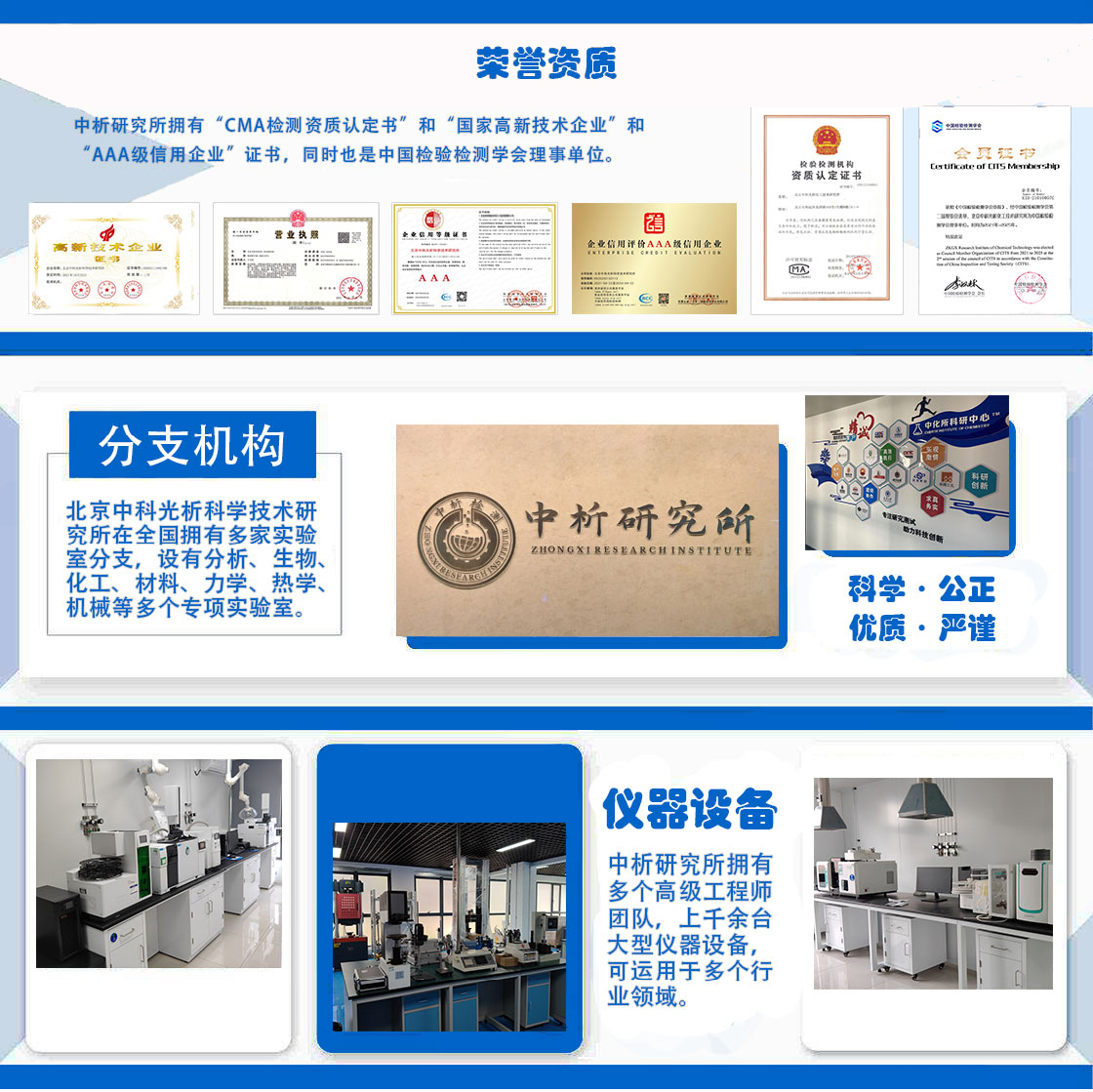
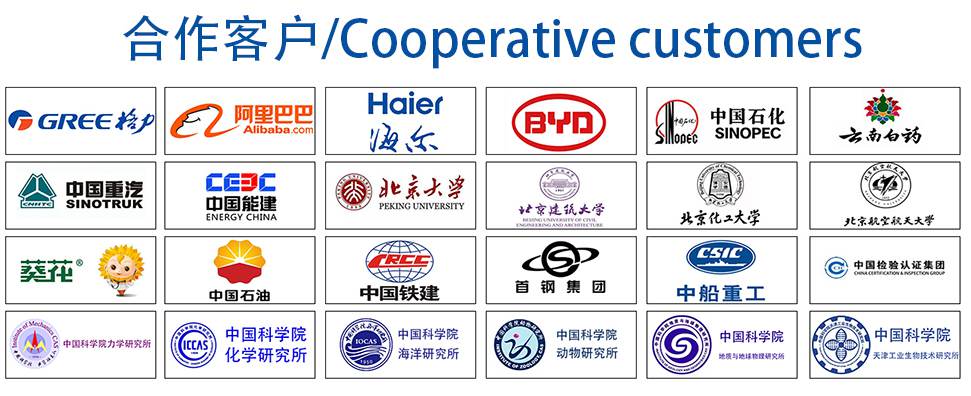