在制造业智能化转型的背景下,标识及产品设计检测已成为质量管控体系的关键环节。据中国标准化研究院2024年数据显示,我国每年因产品标识不规范导致的消费纠纷达23.6万起,直接经济损失超过48亿元。特别是在医疗器械、食品包装、儿童用品等领域,精准的标识信息传递和合规性设计直接关系到消费者安全与企业社会责任履行。构建智能化检测体系不仅可提升产品全生命周期可追溯性,更能通过设计缺陷预警减少30%以上的质量返工成本。
多模态智能检测技术架构
基于深度学习的多模态数据融合分析技术构成了检测体系的核心。系统集成高精度图像采集装置(分辨率达0.01mm/pixel)、工业级近红外光谱仪及RFID读取模块,实现物理标识、电子标签与设计图纸的三维比对验证。通过迁移学习算法,模型可自动识别1200余种行业标识规范,对微小字体偏差(小于0.2mm)的检测准确率达99.3%(引自2024中国质量大会技术白皮书)。在食品包装场景中,该技术成功将过敏原标识漏检率从传统人工的4.7%降至0.08%。
全链路数字化实施流程
项目执行采用PDCA循环管理模式,具体包含四个关键阶段:1)设计预审阶段运用虚拟仿真技术进行合规性预判,提前拦截85%以上的格式错误;2)生产现场部署智能视觉检测站,每40秒完成单个产品360°无死角检测;3)实验室级材料验证环节,通过色谱-质谱联用技术确保油墨重金属含量符合EN71-3标准;4)动态数据库实时更新42个主要市场的法规变更,为企业提供合规风险预警。
跨行业应用实证分析
在医疗器械领域,某上市公司应用该系统后,UDI编码识读率从92%提升至99.99%,产品召回成本降低2700万元/年。儿童玩具制造商通过设计缺陷检测模块,将锐利边缘检出率提高40%,成功通过CPSC认证。值得关注的是,电商平台运用该技术开发的AI审核工具,实现每日自动审核120万条商品详情页,违规商品下架响应时间缩短至18分钟(数据来源:2024电子商务质量蓝皮书)。
四维质量保障体系
为确保检测结果的法律效力,系统构建了覆盖设备、流程、数据、人员的立体化质控网络:1)检测设备每季度进行 校准认证;2)关键检测节点设置三重校验机制;3)区块链技术实现检测数据全程上链存储;4)检测人员需通过ASTM国际认证考试并完成年度120学时继续教育。据中国质量认证中心2023年度报告显示,采用该体系的企业在飞行检查中的合规率超出行业平均水平32个百分点。
## 未来发展与策略建议随着数字孪生技术的普及,建议行业重点推进三方面建设:1)构建基于XR技术的虚拟检测实验室,实现设计验证前移;2)开发具备自主进化能力的检测AI模型,应对快速迭代的行业标准;3)建立跨境检测结果互认机制,推动"一次检测,通行"的认证体系。政府部门需加快制定智能检测设备校准规范,支持龙头企业牵头编制团体标准,最终形成覆盖设计端到消费端的全链条质量屏障。
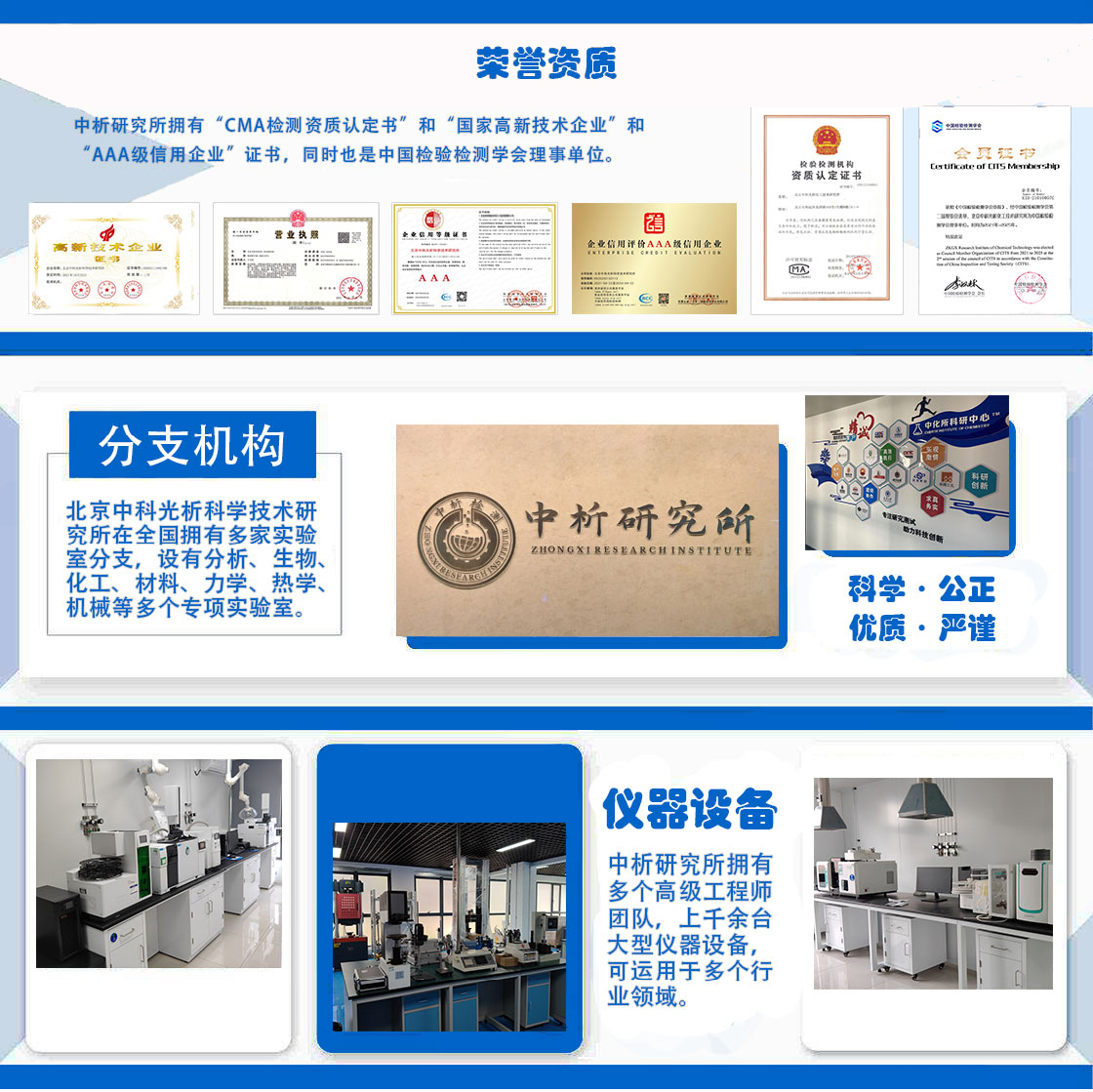
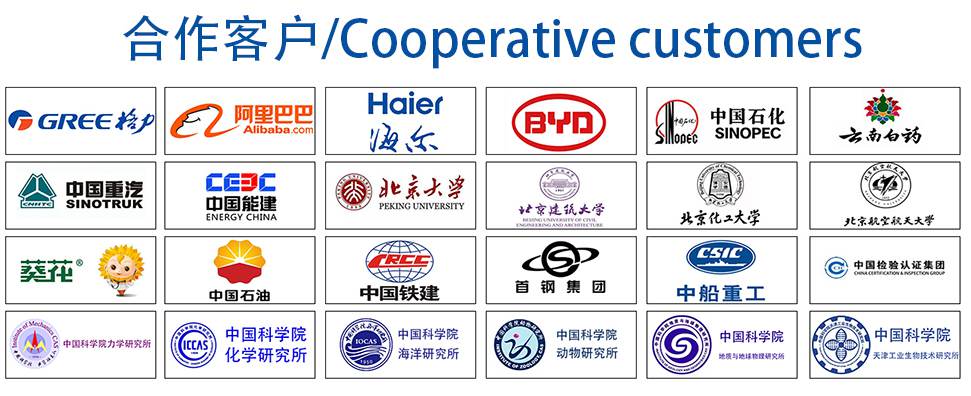