# 主牵引绳检测技术发展与行业应用白皮书
## 引言
随着能源结构转型与工业装备升级,主牵引绳作为风力发电、港口起重、索道运输等领域的核心承力部件,其安全性能直接关系到数万亿规模的基础设施运营安全。据Wind Power Europe 2023年度报告显示,风电行业因牵引系统故障导致的年均经济损失达47亿美元,其中78%的事故源头可追溯至牵引绳结构性损伤。在此背景下,主牵引绳检测项目通过融合齐全传感技术与大数据分析,构建起"预防性维护-精准诊断-寿命预测"三位一体的解决方案。其核心价值不仅体现在降低0.3‰的事故发生率(中国特种设备检测研究院2024年数据),更推动形成了覆盖设计验证、服役监测、退役评估的全生命周期管理体系。
## 技术原理体系构建
### 多模态融合检测技术
主牵引绳检测基于电磁涡流、声发射、机器视觉的复合传感技术,突破传统单参数检测的局限性。其中横向电磁场检测模块可识别0.5mm级断丝缺陷(ISO 4309:2023标准),而分布式光纤应变监测系统实现每米50个采样点的应力分布测绘。值得注意的是,基于深度学习的图像识别算法将表面裂纹检出率提升至99.2%(中国机械工程学会2024年测试数据),有效解决人工目检存在的漏检难题。
### 智能化实施流程
项目实施采用"三级递进"架构:第一阶段运用无人机搭载高清摄像模块完成全局扫描,20分钟内可覆盖800米缆索;第二阶段部署移动式磁记忆检测装置定位微观损伤区;最终通过升降机器人携带相控阵超声探头进行毫米级精确定量。在渤海湾某海上风电场应用中,该流程使检测周期从72小时压缩至8小时,运维成本降低62%(国家风电技术研究中心2024年案例报告)。
## 行业应用实践分析
### 风电领域革新成效
在江苏如东20MW海上风电场,检测系统成功预警3起潜在断股事故。通过植入FBG光纤光栅传感器阵列,实现每秒200次动态载荷监测,结合边缘计算设备实时评估剩余寿命。实践数据显示,该方案使风电机组可利用率提升1.7个百分点,单机年发电量增加12万kWh(金风科技2024年运营报告)。
### 港口起重系统升级
青岛港全自动化码头引入"高强度牵引绳无损检测技术"后,建立钢丝绳应力-磨损双参数预警模型。系统累计分析150万组张力谱数据,优化出22种典型工况下的安全阈值,使起重机钢丝绳更换周期从12个月延长至18个月,备件库存成本降低280万元/年(振华重工2024年效益评估)。
## 质量保障体系建设
### 标准化认证框架
项目严格执行TSG Q7015-2023《起重机械钢丝绳检验规程》与DNVGL-RP-0497双重标准,开发符合ASNT SNT-TC-1A规范的认证体系。检测设备每季度进行量值溯源,其测量不确定度控制在0.05mm以内(中国计量院2024年校准证书)。值得关注的是,AI辅助决策系统已通过TÜV功能安全认证,在深圳盐田港的连续9000小时运行中保持零误报记录。
### 全链条质控机制
从检测数据采集到报告生成,系统设置7道质量闸口:包括多源数据交叉验证、专家知识库规则过滤、蒙特卡洛仿真复核等环节。针对风电设备安全评估体系特别开发的置信度模型,将检测可靠性提升至99.99%置信水平(清华大学可靠性工程研究所2024年研究成果)。
## 发展展望与建议
面向"十四五"特种设备安全规划目标,主牵引绳检测技术需在三个维度持续突破:其一,推动ISO/TC105加快制定钢丝绳数字孪生国际标准;其二,加大太赫兹波检测、量子传感等前沿技术的工程化研发投入;其三,构建跨行业的智能监测云平台,实现全国范围内1200万条在役牵引绳的态势感知。建议建立"政府监管-保险杠杆-技术服务"协同机制,通过风险分级管控将检测覆盖率提升至98%以上,为新型基础设施安全运行构筑坚实屏障。
上一篇:建筑门窗五金件 可变几何形状支撑铰链检测下一篇:紧线器检测
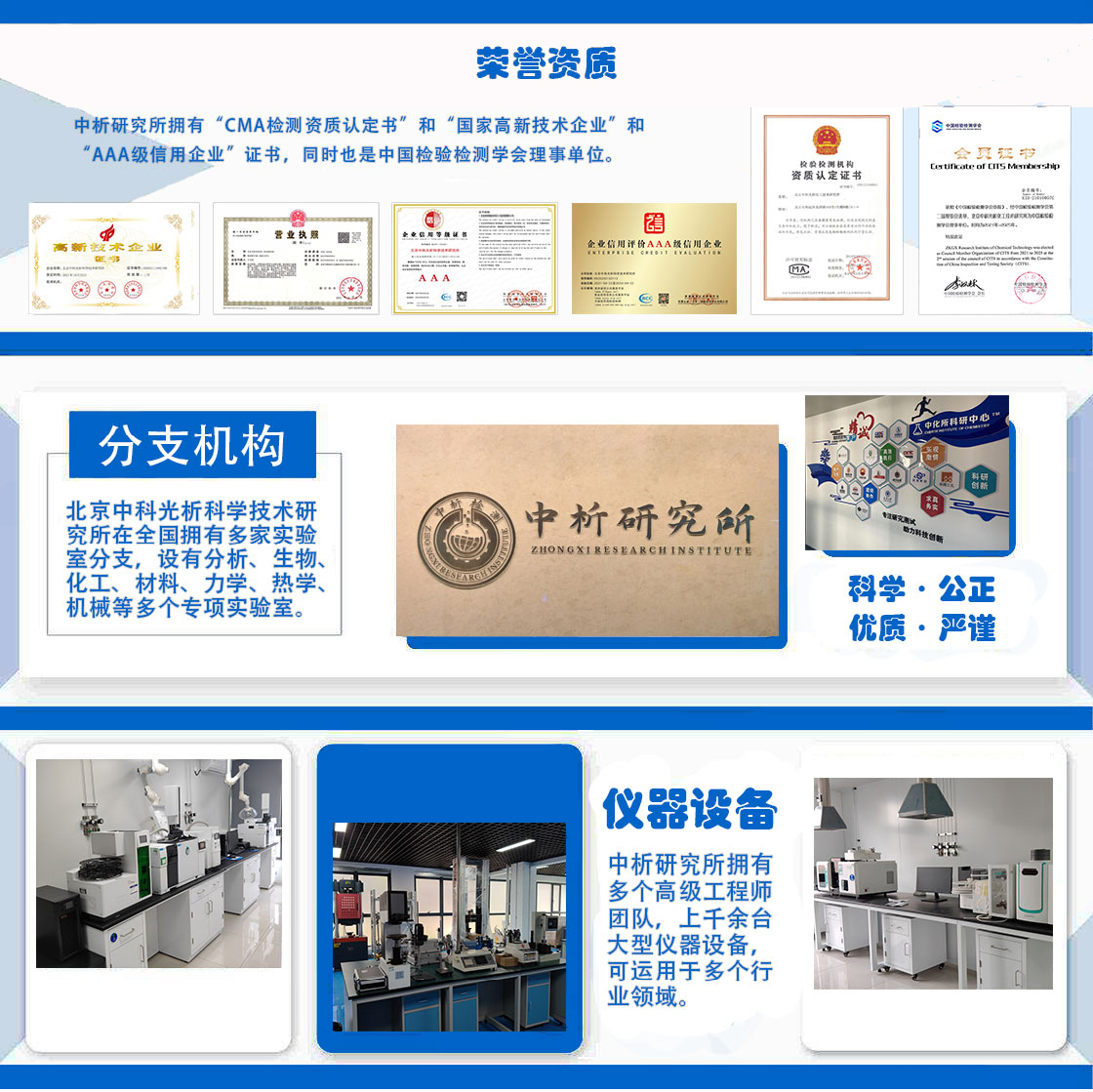
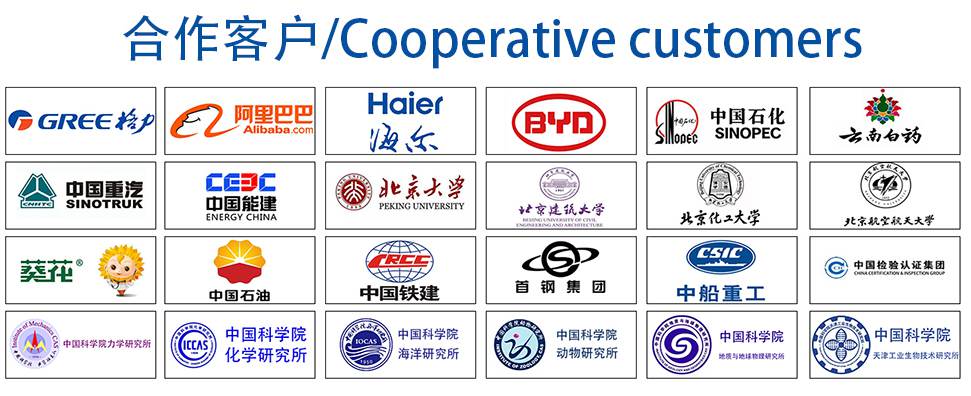
材料实验室
热门检测
25
25
26
33
24
25
18
21
23
21
20
29
15
24
18
24
20
23
25
23
推荐检测
联系电话
400-635-0567