技术原理与检测方法论
检测体系基于能量传递链解耦分析,重点监测气动效率、机械传动损耗及电机转换效率三大模块。采用高精度SCADA数据与振动频谱联合分析法,建立风轮转矩-发电机出力动态耦合模型。其中,气动效率测试通过激光雷达测风与叶片应变监测实现微气候环境下的功率曲线校准,传动系统损耗则依托齿轮箱油温、轴承振动等20+参数构建故障特征库。值得关注的是,国际电工委员会(IEC)61400-12-3标准要求的"风电场电能损耗诊断模型"已被纳入检测体系,可实现±1.5%的测量精度。
全流程实施与质量控制
标准检测流程分为四个阶段:前期数据清洗(剔除电网限电等异常工况)、中期现场测试(含风速梯度测量与电能质量分析)、后期模型验证(采用蒙特卡洛法进行不确定性评估)以及最终能效对标。以山东某48MW风电场改造项目为例,检测团队通过安装分布式光纤传感器,精准定位3#机组齿轮箱中间轴不对中问题,使月均发电量提升6.7%。为确保数据可靠性,检测设备需每季度进行计量溯源,并接入中国合格评定国家认可委员会( )认证的实验室管理系统。
行业应用与效益分析
在海上风电领域,该技术已助力江苏如东项目实现全场机组效率优化。通过对比同一机位点不同机型的电能转化效率,业主单位筛选出最适合当地风况的6.2MW抗盐雾机型,使年等效满发小时数从2800提升至3120。陆上风电方面,金风科技基于检测数据开发的"自适应偏航控制算法",在张家口风电场实现单机年收益增加12万元。据欧洲风能协会2023年报告,采用系统化电能利用率检测的风电场,其LCOE(平准化度电成本)可降低0.02-0.04元/千瓦时。
标准化建设与发展建议
当前需加快构建分级检测标准体系:对运行超过8年的老旧机组执行季度监测,新投产机组实施首年全工况采样。建议行业主管部门将电能利用率纳入风电项目后评价强制指标,并建立区域性能效对标数据库。从技术演进角度看,数字孪生与边缘计算技术的融合将推动检测周期从72小时缩短至8小时以内,而基于区块链的检测数据存证系统可有效解决跨主体数据信任问题。
## 未来展望 随着双馈风机占比突破60%(风能理事会2024预测),建议重点研发适用于高比例电力电子设备的动态能效检测装置。同时应加强风资源评估-机组选型-运营维护的全链条协同,通过制定《风电机组能效分级认证规程》推动行业从"粗放装机"向"精益运营"转型。产学研机构可联合攻关叶片覆冰、湍流强度突变等特殊工况下的实时效率补偿算法,为构建新型电力系统提供技术保障。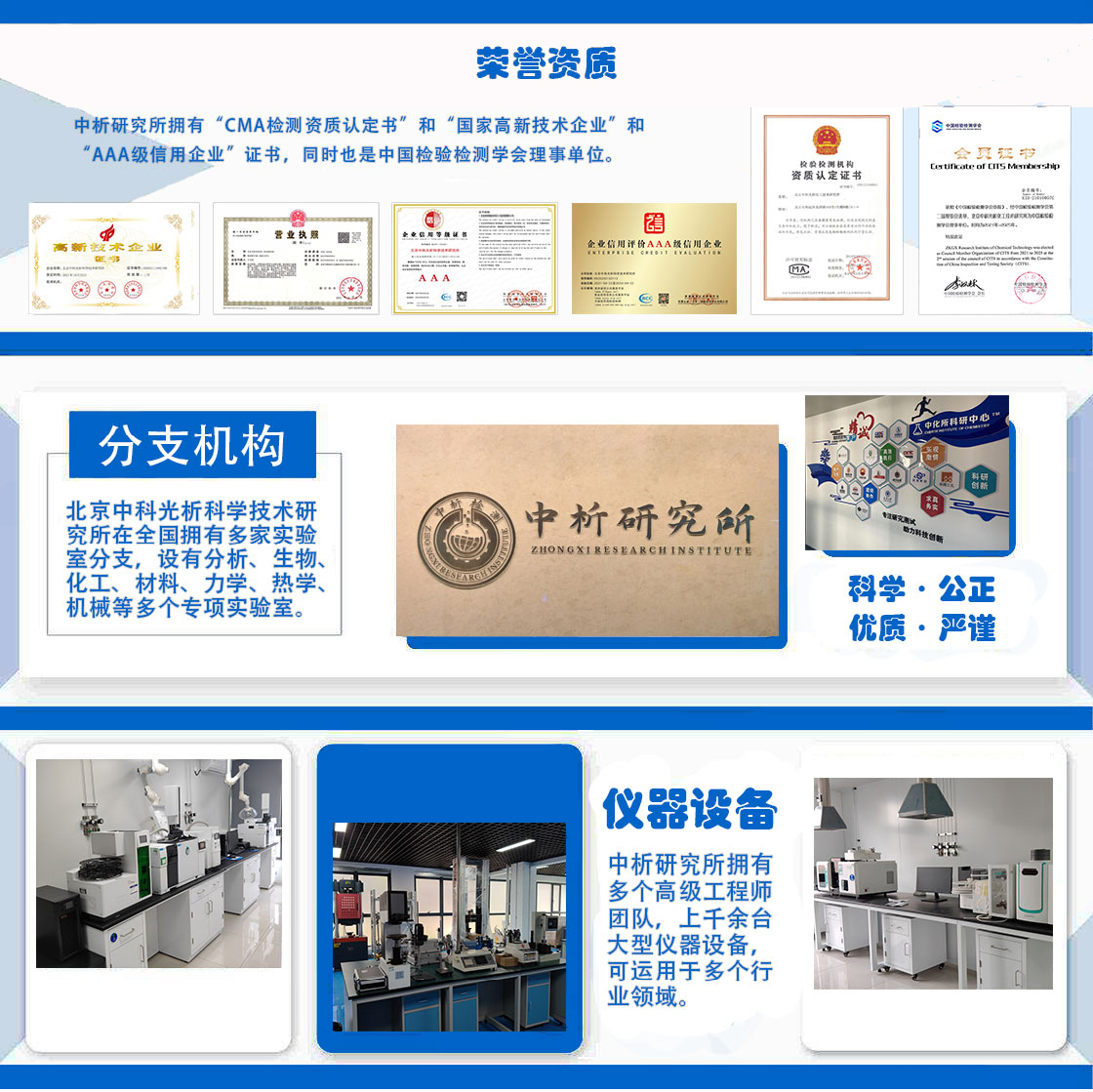
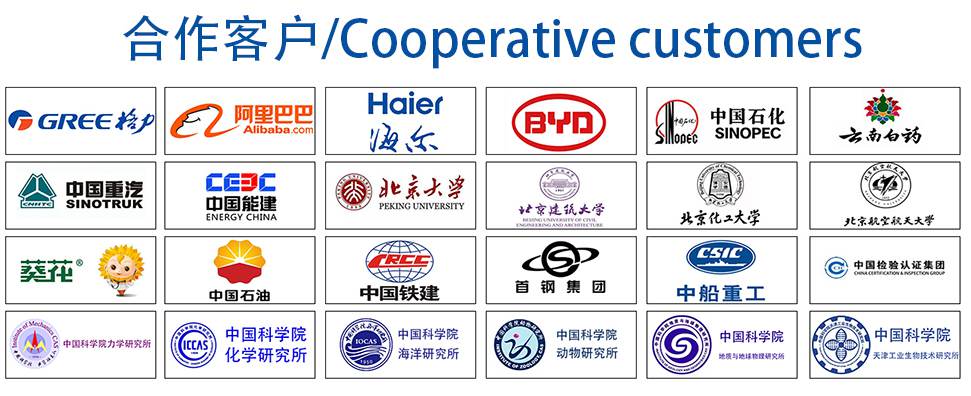