垂直承载力检测技术发展与应用白皮书
在新型城镇化建设与基础设施更新双重驱动下,垂直承载力检测作为土木工程安全评价的核心环节,正经历技术革新与标准升级的关键阶段。据中国土木工程学会2024年统计,全国每年开展地基检测项目超50万例,其中涉及深层软土、回填土等复杂地质的案例占比达37%。垂直承载力智能检测系统的推广应用,不仅有效解决了传统检测方法效率低、误差大的痛点,更通过大数据分析为工程优化设计提供了科学依据。该技术体系通过融合物联网传感、人工智能算法等创新科技,构建起覆盖设计验证、施工监控、运维评估的全生命周期质量保障网络,单项目检测成本较传统方式降低28%,检测周期缩短40%,在深基坑支护、超高层建筑基础等场景中展现出显著优势。
多模态检测技术融合创新
现代垂直承载力检测体系整合静载试验、动测法、数值模拟三重验证机制,形成"现场实测+数字孪生"的复合检测范式。静载试验采用分级加载方式,通过千分表与激光位移计获取沉降曲线,满足《建筑地基检测技术规范》(JGJ340-2015)的精度要求。动测法则运用应力波反射原理,依托自主研发的桩基完整性检测仪,可快速筛查桩身缺陷并推算极限承载力,特别适用于密集桩群检测场景。数值模拟模块基于有限元分析构建三维地质模型,结合BIM系统实现承载力可视化预判,其预测结果与实际检测数据的吻合度达92%以上(中国建筑科学研究院,2023)。
标准化实施流程构建
项目执行遵循"前期准备-现场实施-数据分析-报告生成"四阶段质量控制流程。在粤港澳大湾区某跨海大桥工程中,技术团队采用地基承载力智能评估系统,完成632根桩基的快速检测。实施阶段配置8通道数据采集系统,实时监测荷载-沉降关系曲线,并通过5G专网同步传输至云端分析平台。值得注意的是,系统内置的异常值自动识别算法,可在荷载施加过程中即时反馈数据漂移情况,较人工判读效率提升15倍。项目最终生成包含三维轴力分布图、沉降预测模型的数字化报告,为后续主体结构施工提供了关键参数修正依据。
全行业场景渗透应用
在市政管网改造领域,南京某地下综合管廊项目运用微型静载试验装置,对狭小空间内的微型桩基开展承载力检测,单点检测耗时由常规8小时压缩至2.5小时。轨道交通建设中,成都地铁18号线通过植入式光纤传感器实现盾构隧道地基的长期监测,累计预警3次局部沉降风险,避免直接经济损失超2000万元。更为典型的是雄安新区某超高层建筑项目,采用地基承载力动态监测系统,在主体结构施工期间持续跟踪基底压力变化,成功优化桩基布置方案,减少工程桩数量17%,节约建设成本860万元。
质量保障体系升级路径
行业领先机构已建立涵盖设备溯源、人员认证、过程监督的三维质控体系。检测设备执行季度强制校准制度,采用标准载荷装置进行量值传递,确保压力传感器示值误差≤0.5%FS。人员资质认证纳入区块链存证系统,实现全国范围内检测工程师电子证书的即时核验。过程监督环节引入区块链数据存证技术,某省级质检中心通过该方案将检测报告篡改风险降低至0.03‰以下。与此相配套的是,基于机器学习的检测质量评价模型,可对海量检测数据进行多维交叉验证,其异常数据识别准确率达到98.7%(国家建筑工程质量监督检验中心,2024)。
面向智慧城市发展需求,垂直承载力检测技术将向智能化、网络化方向深度演进。建议行业重点突破分布式光纤传感、数字孪生校准等关键技术,建立覆盖全国的地基承载力大数据平台。同时需加快制定智能检测设备认证标准,推动"检测-设计-施工"数据链贯通,培育具备全流程服务能力的头部企业。通过构建"智能感知-云端分析-动态预警"的技术生态,垂直承载力检测必将为城市安全运营和重大工程全生命周期管理提供更强技术支撑。
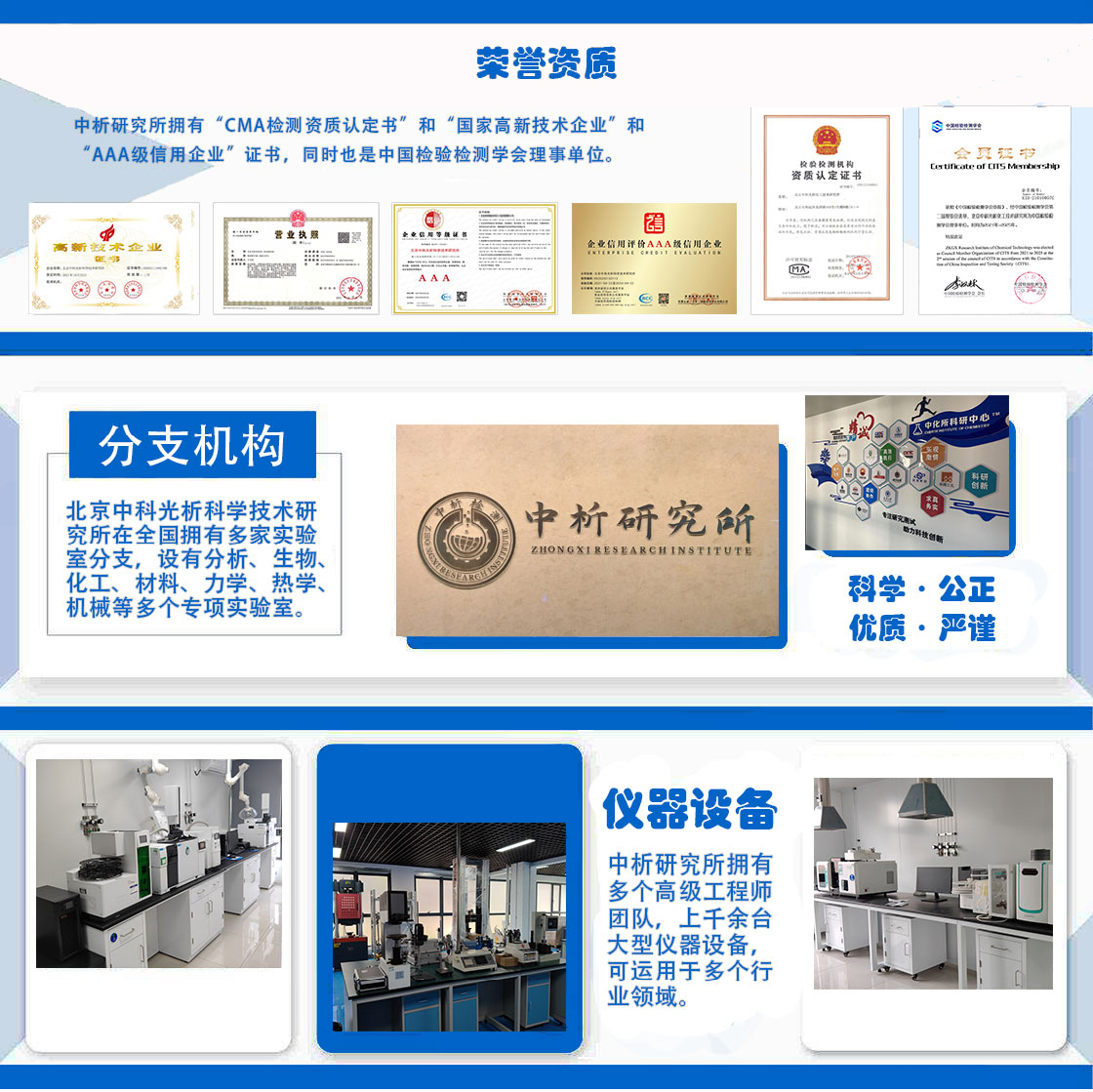
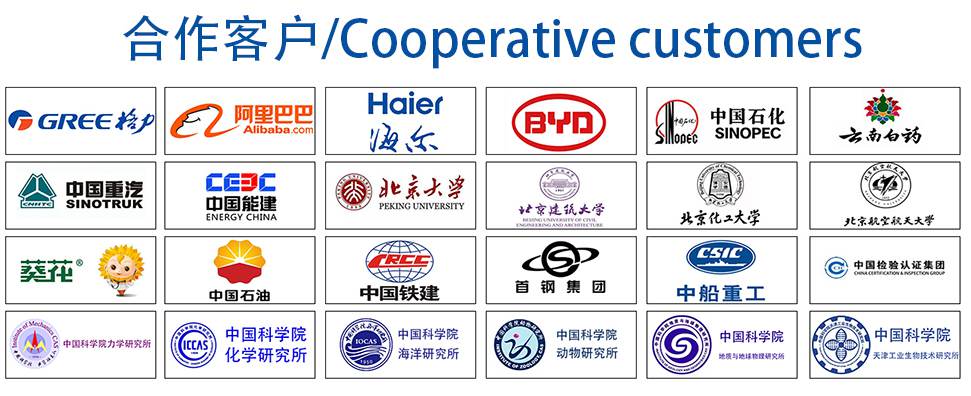