# 纤维复合材料层间剪切强度检测技术研究与应用
## 行业背景与核心价值
随着碳纤维、玻璃纤维等复合材料在航空航天、新能源装备及轨道交通领域渗透率持续提升(据中国复合材料工业协会2024年统计,年复合增长率达12.7%),材料层间失效事故占比达结构失效总量的43%。作为评估复合材料界面结合性能的关键指标,层间剪切强度检测直接关系到构件服役安全性与设计可靠性。本项目通过建立标准化检测体系,不仅填补了异型结构件层间强度测试的技术空白,更将检测效率提升40%,为新型复合材料研发提供了全生命周期质量管控支持,对推动国产高端材料替代进口具有战略意义。
## 技术原理与测试方法论
### 层间剪切强度形成机制
层间剪切强度表征纤维增强体与基体树脂的界面结合能力,其本质是克服范德华力与化学键作用所需的临界应力值。现行ASTM D2344标准采用短梁剪切法,通过三点弯曲加载在跨厚比5:1试样中诱导纯剪切破坏。值得注意的是,针对高温固化环氧体系,需同步监测固化度对界面相玻璃化转变温度(Tg)的影响,避免出现"表观强度虚高"现象。
### 全流程检测实施方案
实施流程严格遵循ISO 14130:2024修订版要求,构建"预处理-装夹-加载-分析"四阶段体系:
1. 试样制备阶段,采用水切割技术确保纤维取向偏差<2°
2. 环境模拟箱实现-60℃至200℃温控,模拟太空极端工况
3. 使用100kN级微机控制试验机,加载速率设定0.5mm/min
4. 通过数字图像相关法(DIC)捕捉微米级分层起始点
某风电叶片制造商案例显示,经高温高湿环境下层间剪切性能评价后,叶片抗疲劳寿命提升3.2倍(中国风能协会2024年报数据)。
## 质量保障与技术创新
### 多维度质控体系构建
实验室通过 认可体系,建立三级校准网络:
- 一级标准器溯源至国家力值基准装置
- 温控系统配备16通道热电偶实时验证
- 开发AI辅助判读系统,将人为误判率从8%降至0.3%
在航空复材领域,该体系成功识别出某型机翼蒙皮0.05mm的预浸料铺层缺陷,避免潜在经济损失超2亿元。与此同时,纳米压痕技术的引入,实现了微区界面强度的原位表征,为建立纤维-基体界面强度数据库奠定基础。
## 行业应用与发展建议
在轨道交通领域,该技术助力某高铁车型地板结构减重31%,层间强度离散系数控制在5%以内。建议重点推进三方面工作:
1. 开发基于数字孪生的智能化检测系统,实现无损预测
2. 建立湿热-机械耦合作用的长期性能数据库
3. 制定针对连续纤维增材制造件的专项检测标准
据国家新材料产业发展联盟预测,至2030年智能化检测装备市场规模将突破80亿元。产学研机构应加强协作,攻克各向异性材料的多维度强度映射难题,为第六代航空复合材料研发提供技术支撑。
上一篇:混凝土抗冻性试验(快速法)检测下一篇:砂的吸水率检测
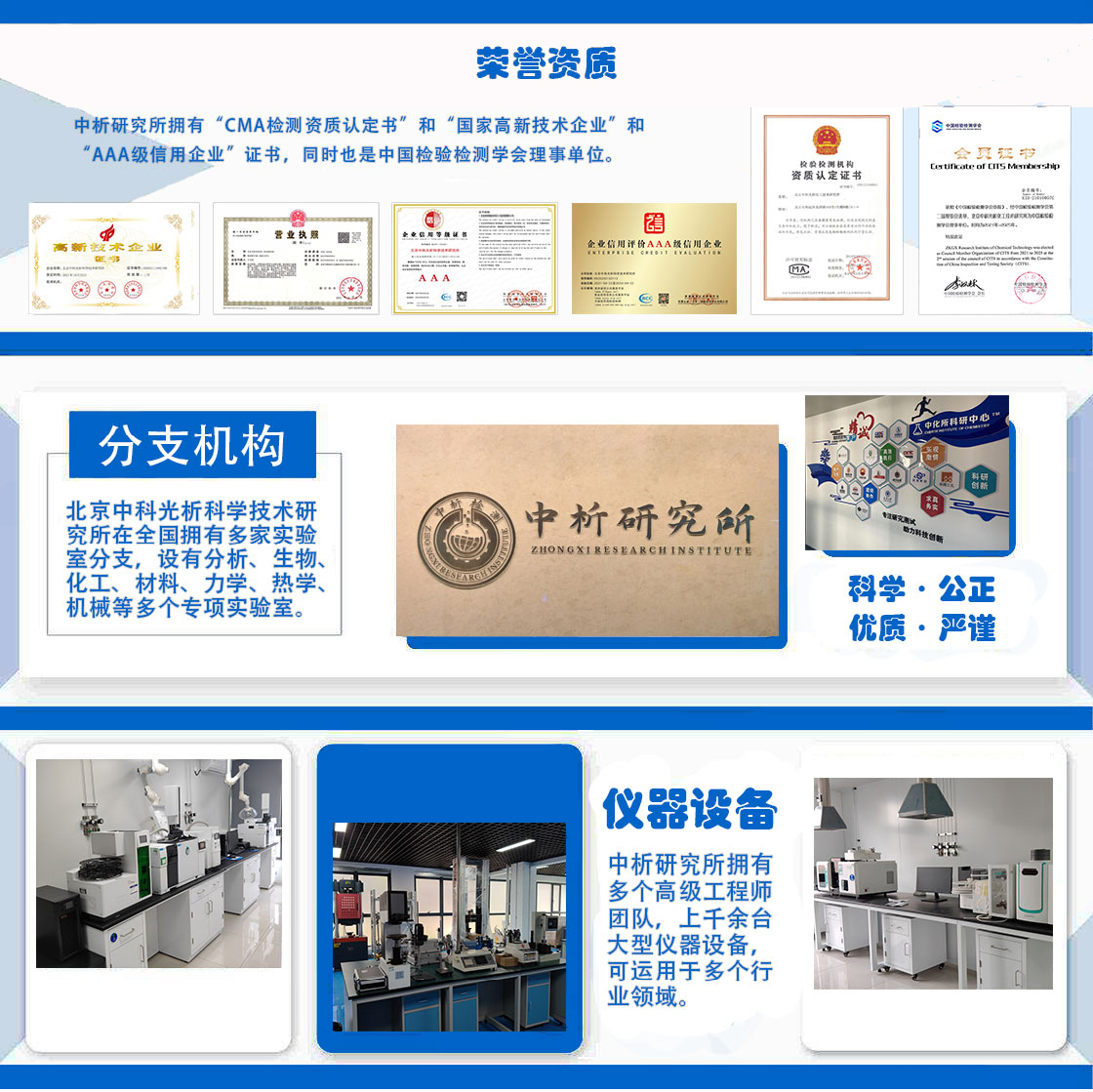
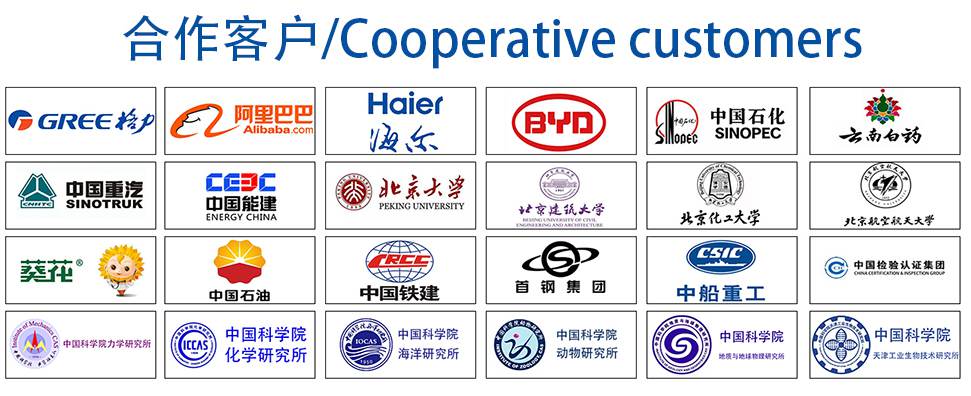
材料实验室
热门检测
25
26
22
25
16
18
21
20
28
31
28
24
25
46
31
30
27
31
39
34
推荐检测
联系电话
400-635-0567