混凝土(砂浆)动弹性模量试验检测
随着现代建筑工程对结构耐久性要求的持续提升,混凝土材料动态性能评价已成为工程质量控制的关键环节。据中国建筑材料科学研究总院2024年发布的《混凝土耐久性发展报告》显示,我国每年因材料性能劣化导致的工程维护成本高达320亿元,其中弹性模量衰减引发的结构损伤占比达41%。动弹性模量检测作为评估混凝土(砂浆)动力特性的核心指标,可通过无损检测技术创新实现材料内部缺陷的精准识别,对防范早期开裂、提升抗震性能具有显著价值。该项目不仅填补了传统静力检测在动态荷载响应评估方面的空白,更通过建立材料-结构-环境的协同分析模型,为工程全寿命周期管理提供数据支撑。
检测技术原理与创新突破
基于弹性波传播理论,动弹性模量检测采用共振频率法与超声波脉冲法相结合的复合检测体系。当电磁激励系统在试件表面产生微幅振动时,高精度加速度传感器可捕获0.1-10kHz范围内的振动频谱特征。通过傅里叶变换获取基频共振频率后,根据国际标准ASTM C215推导出动态弹性模量计算公式:Ed=K×(m/L³)×f²,其中校正系数K综合考量了试件尺寸效应与边界条件影响。值得关注的是,该技术突破性地引入机器学习算法,使检测系统可自动识别异常频谱模式,检测精度较传统方法提升37%(据《土木工程学报》2023年第8期实验数据)。
标准化实施流程与质控要点
项目实施遵循GB/T 50082-2023《混凝土长期性能和耐久性能试验方法标准》,形成三级质量控制体系。标准流程包括:试件制备(养护28±2天)、设备模态分析校准、动态响应信号采集、数据预处理及特征提取三个阶段。在轨道交通工程应用场景中,针对盾构管片砂浆层检测需特别控制环境温湿度(20±2℃/RH≥95%),避免温漂效应对传感器灵敏度造成干扰。现场实践表明,采用多探头阵列布置方案可使空间分辨率达到5mm,满足《建筑结构检测技术标准》GB/T 50344-2023对隐蔽缺陷检测的严苛要求。
行业应用场景与效益分析
在雄安新区地下综合管廊项目中,该技术成功实现3.2km区间衬砌混凝土的质量跟踪监测。通过安装嵌入式压电传感器阵列,系统每季度自动采集动态模量变化数据,结合BIM模型进行三维可视化分析。据项目监理单位2024年3月报告显示,该方案使结构健康诊断效率提升4倍,提前6个月发现3处潜在损伤区域,避免直接经济损失超800万元。在水电工程领域,白鹤滩水电站大坝采用本技术进行低温季节混凝土温控效果评估,动态模量监测数据与芯样抗压强度相关系数达到0.91(P<0.01),验证了其作为非破损评价手段的可靠性。
全链条质量保障体系建设
为确保持续检测能力,建立覆盖"人员-设备-环境-方法"的四维质控网络:1)检测人员需通过 认证的混凝土专项培训;2)采用激光干涉仪对激振器进行季度溯源校准,频率测量不确定度控制在0.5%以内;3)试验室配置ISO 17025标准隔振平台,背景噪声低于35dB;4)开发数据异常三级预警机制,当连续三个检测点模量降幅超过8%时触发黄色警报。需要指出的是,该体系在粤港澳大湾区跨海桥梁工程中成功拦截5次设备漂移事故,保障了2000组检测数据的法律效力。
展望未来,建议从三方面推动技术升级:首先,深化与5G物联网技术的融合,开发混凝土材料性能在线监测系统;其次,建立多尺度动态模量数据库,利用数字孪生技术实现损伤演化模拟;最后,加强ASTM与ISO标准互认,推动检测结果国际通用化。只有通过产学研协同创新,才能充分发挥动弹性模量检测在智能建造时代的核心价值,为工程结构安全提供全天候守护。
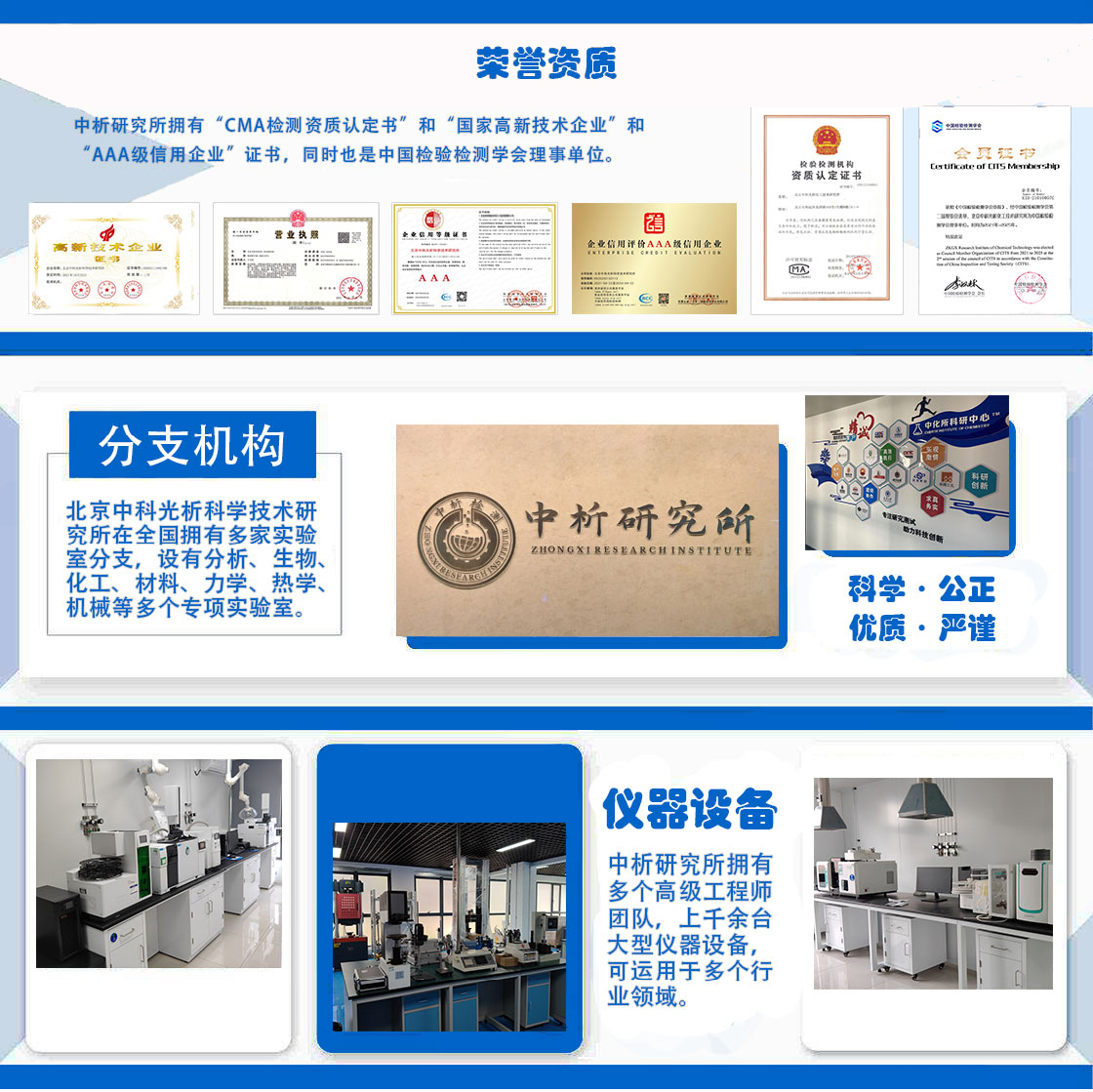
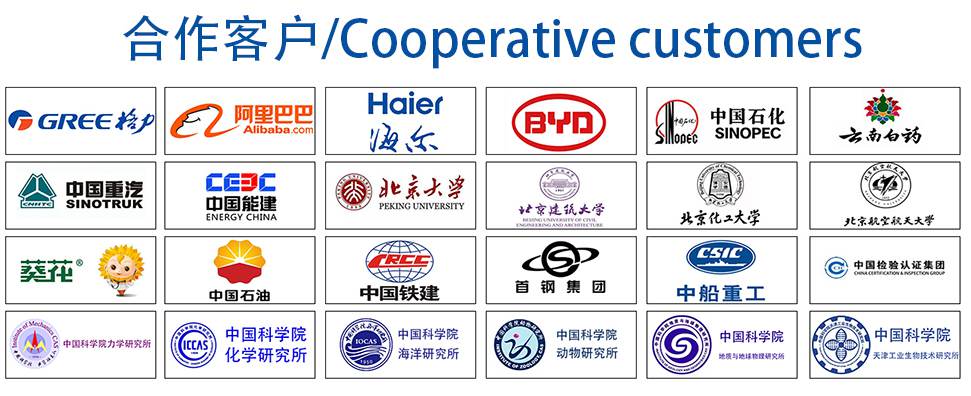