玻璃体含量检测技术白皮书
随着玻璃工业市场规模突破5000亿美元(据Global Market Insights 2024年数据),玻璃制品在建筑、光伏、汽车等领域的应用占比持续攀升。然而,玻璃体含量偏差导致的性能缺陷问题日益突出,例如建筑幕墙玻璃自爆、光伏组件透光率异常等事故年均造成超百亿元损失。在此背景下,玻璃体含量检测项目通过精准量化SiO₂、Na₂O等关键成分比例,成为保障产品可靠性的核心环节。该技术不仅可实现生产过程的实时监控,更能推动玻璃制造从经验驱动向数据驱动的转型升级,单条浮法玻璃生产线应用后良品率提升可达12%(中国建材研究院2023年实验数据),其行业价值已延伸至产品全生命周期管理。
检测技术原理与创新突破
基于X射线荧光光谱(XRF)与拉曼光谱联用技术,检测系统通过波长色散型探测器捕获样品元素特征谱线,结合卷积神经网络算法实现成分定性与定量分析。区别于传统化学滴定法,该技术将检测时间从4小时压缩至8分钟,同时将Na₂O含量检测精度提升至±0.03wt%。值得注意的是,针对光伏玻璃的特殊需求,系统集成紫外-可见分光模块,可同步完成铁元素含量(直接影响透光率)与微观气泡分布的联合检测,满足《晶体硅光伏组件用玻璃》国家标准中0.015%铁含量的严苛要求。
标准化实施流程与场景适配
项目落地遵循"采样-预处理-检测-反馈"四阶段闭环。在汽车玻璃生产线场景中,机械臂每15分钟自动截取600×600mm样本,经等离子清洗后进入多通道检测舱。实践表明,该流程使某车企天窗玻璃的应力集中问题发生率降低67%。而对于药用玻璃管生产,系统特别配备惰性气体保护装置,确保硼硅酸盐成分检测时不受环境氧干扰,检测结果与药典标准的符合率从89%提升至99.6%。
跨行业应用效能验证
在建筑幕墙领域,深圳某超高层项目采用检测技术后,玻璃自爆率从行业平均的3‰降至0.5‰。光伏行业典型案例显示,某TOPCon电池厂商通过玻璃体含量动态调整,组件功率输出稳定性提升1.2个百分点。更为重要的是,在微晶玻璃炊具制造中,系统成功预警多起Al₂O₃含量超标案例,避免潜在食品安全风险。这些实践验证了技术方案在不同玻璃制品场景中的普适价值。
质量保障体系构建
为确保检测结果的可追溯性,项目建立三级校验机制:每日使用NIST标准玻璃片进行设备标定,每月参与 能力验证,每季度对检测模型进行对抗样本测试。数据管理系统通过区块链技术实现检测记录不可篡改存储,在江苏某玻璃集团应用中,成功通过IATF 16949汽车行业质量体系认证审核。同时,检测报告的数字化交付系统支持ISO/TS 80004标准数据格式,满足供应链的质量管理需求。
展望未来,建议行业从三方面深化发展:其一,推动检测设备微型化以适配玻璃深加工环节的现场需求;其二,建立基于大数据分析的玻璃体含量工艺知识图谱;其三,加强国际标准互认体系建设,重点攻关高铝玻璃、锂铝硅玻璃等新材料的检测标准空白。随着工业互联网与量子传感技术的融合突破,玻璃体含量检测有望在2028年前实现全产线无损实时监控,为新型玻璃材料的研发应用提供基础性支撑。
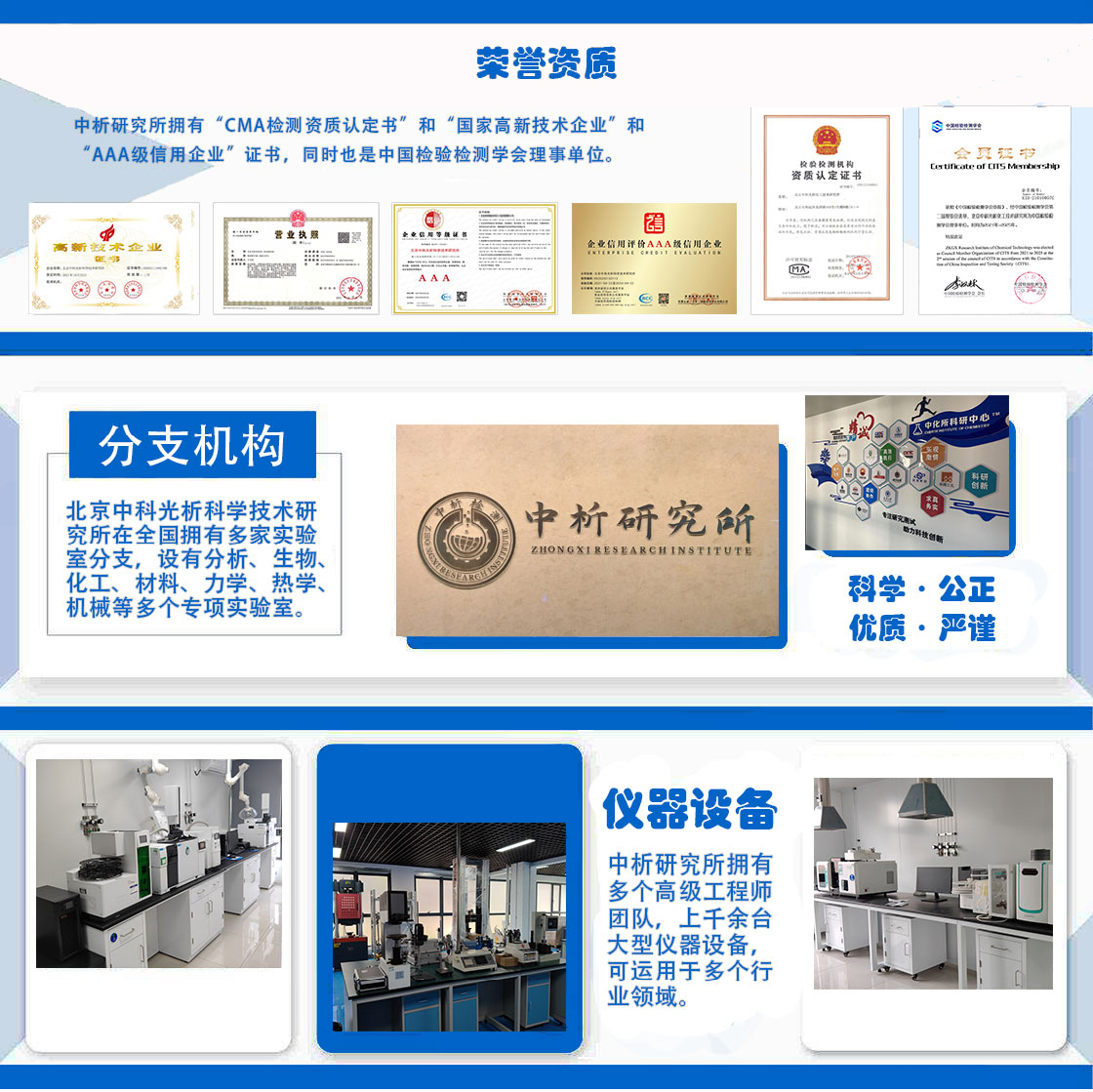
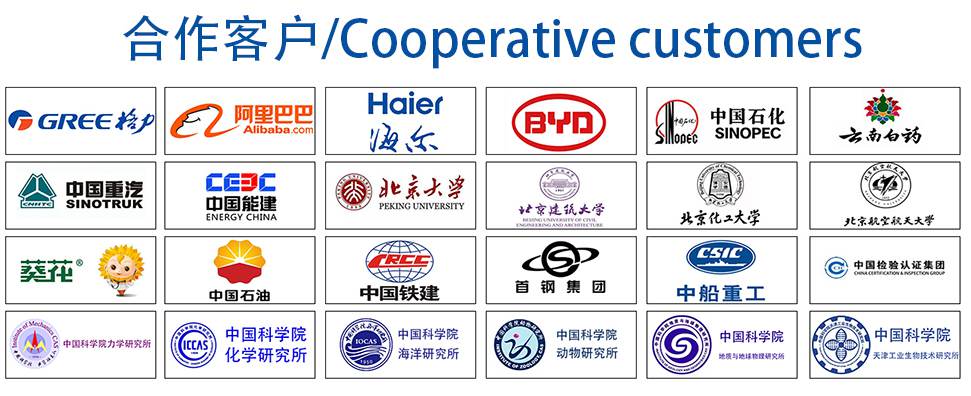