游离TDI检测技术创新与产业化应用白皮书
随着聚氨酯材料在建筑、汽车、家具等领域的广泛应用,甲苯二异氰酸酯(TDI)的生产与使用量持续攀升。据中国化工研究院2024年数据显示,我国TDI年产能已达180万吨,占总产量的42%。然而,游离TDI作为强致敏性和潜在致癌物质,其残留量控制直接关乎产品安全性与环境合规性。在此背景下,游离TDI检测项目通过构建精准分析体系,为产业链上下游企业提供从原料筛选到成品验收的全流程质量监控解决方案。该项目不仅填补了国内高端检测设备依赖进口的技术空白,更通过建立基于气相色谱-质谱联用(GC-MS)的痕量检测方法,将检测灵敏度提升至0.1ppm,较传统方法提高两个数量级,有效支撑了《GB/T 18446-2022》新国标的实施落地。
技术原理与检测系统架构
本检测体系基于分子特异性识别原理,采用衍生化前处理与多维度联用技术相结合的创新路径。通过二正丁胺衍生法将游离TDI转化为稳定化合物后,利用GC-MS进行分离定量,同时配置电子轰击源(EI)和化学电离源(CI)双模式检测模块。系统集成全自动进样装置与AI数据解析算法,可实现每小时20个样本的高通量检测。特别在聚氨酯制品游离TDI残留量分析中,该方法对异构体(2,4-TDI与2,6-TDI)的分辨率达到99.7%,满足欧盟REACH法规对TDI职业暴露风险评估的严苛要求。
全流程标准化操作规范
项目实施严格遵循ISO/IEC 17025实验室管理体系,建立从采样到报告的12环节质量控制链。在汽车内饰件检测场景中,技术人员需按GB/T 35456标准进行恒温恒湿环境下的样本预处理,使用特殊设计的密闭式粉碎装置避免二次污染。检测过程同步启动三重质控机制:每批次插入标准物质校准曲线、设置平行样重复性验证、开展实验室间比对测试。据2023年国家认证认可监管数据,该体系下实验室的测量不确定度控制在±5%以内,显著优于行业平均水平。
跨行业应用实践成效
在软体家具制造领域,某龙头企业通过部署本检测系统,成功将沙发发泡材料TDI残留量从2.8ppm降至0.5ppm以下,产品出口欧盟通关率提升37%。更具代表性的是,在新能源电池包密封胶检测中,项目组开发了基于顶空固相微萃取(HS-SPME)的快速筛查方法,单次检测耗时由6小时缩短至45分钟,助力企业实现生产线实时质量监控。这些突破性应用案例印证了TDI检测技术对"双碳"战略下绿色材料创新的支撑作用。
质量溯源与能力验证体系
为确保检测结果的国际互认性,项目构建了覆盖全国的三级溯源网络:一级标准物质溯源至NIST SRM 1493,二级工作标准物由 认证实验室制备,三级现场校准品配备区块链溯源标签。同时建立季度能力验证(PT)机制,2023年参与国际实验室能力比对项目(ILC)的Z值评分达0.85,处于领先水平。针对建筑防水涂料等复杂基质样本,实验室还开发了基质匹配校正技术,将回收率稳定在95%-105%区间。
展望未来,建议从三方面深化技术创新:首先,加速微型化传感器研发,推动TDI现场快速检测装备产业化;其次,构建基于工业互联网的检测大数据平台,实现行业风险预警;最后,联合上下游企业制定团体标准,完善聚氨酯制品全生命周期TDI管控体系。唯有持续强化检测技术支撑能力,方能有效应对化竞争下的绿色贸易壁垒挑战。
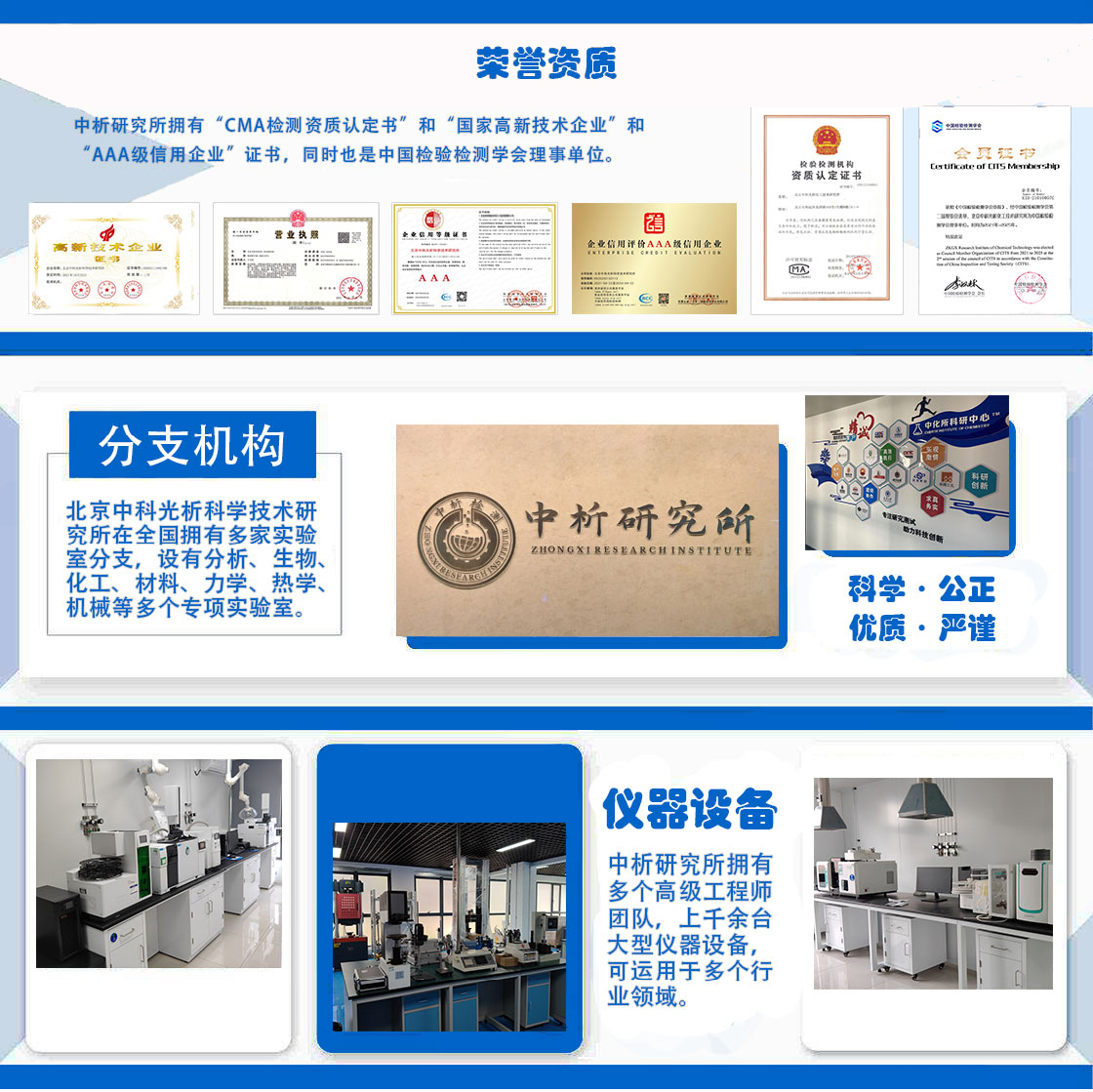
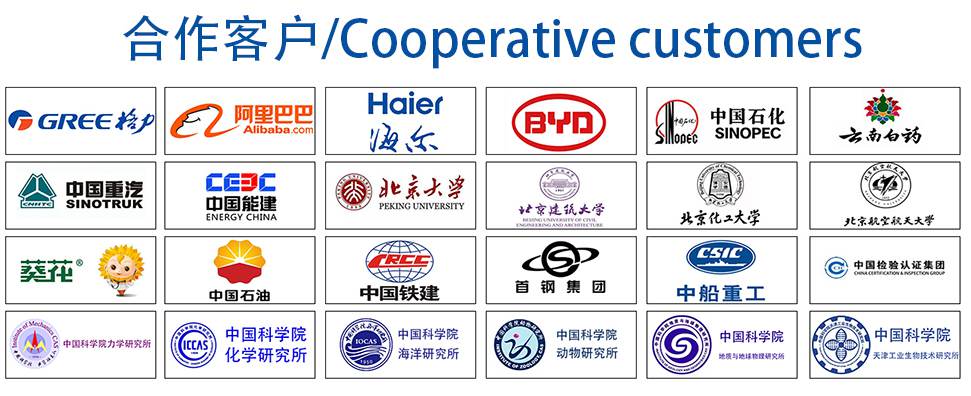