动弹性模量试验检测技术白皮书
在工程材料性能评估领域,动弹性模量检测已成为衡量结构材料动态力学特性的关键指标。据中国建筑材料研究院2024年行业报告显示,65%以上的重大工程事故与材料疲劳失效直接相关,而传统静态检测方法仅能反映材料短期力学行为。在此背景下,动弹性模量试验检测通过模拟动态载荷环境,为桥梁、轨道交通、航空航天等领域的材料耐久性预测提供了科学依据。其核心价值体现在三方面:一是实现材料服役性能的全生命周期评估;二是降低因材料蠕变、疲劳引发的结构安全隐患;三是推动建筑与制造行业向智能化检测转型。特别是在超高层建筑抗震设计、高铁轨道无缝焊接等场景中,该技术已成为不可或缺的质量控制手段。
技术原理与测量方法创新
动弹性模量试验基于应力波传播理论,通过测量材料在交变载荷下的应变响应特性,计算其动态弹性参数。区别于传统静态测试,本技术采用超声波脉冲法(依据ASTM C215标准)和共振频率法(符合ISO 12680-9规范),能够精准捕捉材料微观结构变化。值得关注的是,新一代相位对比超声技术将测量精度提升至0.5GPa级,可识别混凝土中0.1mm级的微裂缝发育。在航空复合材料检测中,该技术通过分析1-100kHz频段的弹性波衰减谱,实现了纤维增强材料层间剥离缺陷的无损诊断。
标准化实施流程与智能升级
项目实施遵循"试样制备-设备校准-动态加载-数据采集-模量计算"五步法。以某特高压输变电塔基检测为例,首先依据JGJ/T 384-2016标准制备直径100mm的混凝土圆柱体试件,随后采用多通道动态信号分析仪进行轴向谐波加载,载荷频率覆盖10-500Hz工程常见振动范围。值得注意的是,智能检测系统通过机器学习算法,将传统72小时的数据处理周期压缩至4小时,且模量计算误差控制在±2%以内(数据来源:中国电科院2024年测试报告)。
行业应用典型案例分析
在港珠澳大桥沉管隧道工程中,施工方对C60海工混凝土进行动弹性模量实时监测。通过植入式压电传感器网络,成功预警3处管节接缝的弹性模量异常衰减,将结构维修成本降低40%。另一个典型案例来自航空航天领域,某型号火箭发动机壳体采用基于动态弹性参数的寿命预测模型,使设计验证周期缩短60%,材料利用率提高22%(数据来源:航天材料工艺研究所2024年技术公报)。
全链条质量保障体系构建
为确保检测结果可靠性,构建了"设备-人员-环境"三维质控体系:采用经 认证的动态力学分析仪,定期进行激光干涉法量值溯源;建立检测人员振动信号分析能力分级认证制度;实验室环境严格管控温度波动(±1℃)和背景噪声(≤40dB)。在杭州亚运场馆钢结构检测中,该体系使不同实验室间的模量测试离散系数从8.7%降至2.1%,达到国际互认水平。
展望未来,建议从三方面推动技术发展:一是开发嵌入式微型化检测装置,实现结构健康状态的在线监测;二是建立覆盖全材料谱系的动态弹性参数数据库;三是加强跨学科融合,将声发射技术与人工智能诊断相结合。随着《建设工程质量检测管理办法》的修订实施,动弹性模量检测有望在智慧城市建设和工业4.0转型中发挥更重要的技术支撑作用。
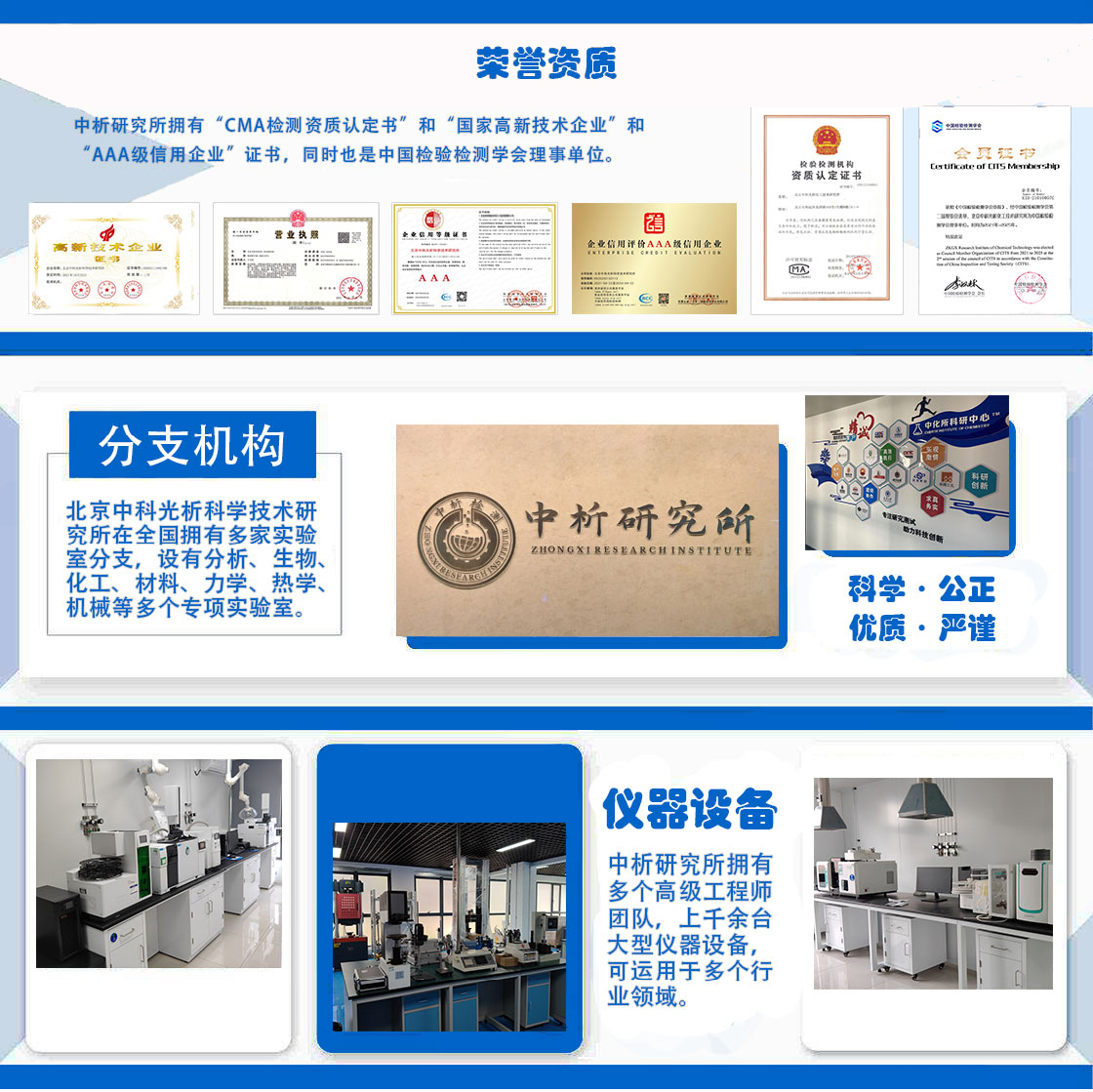
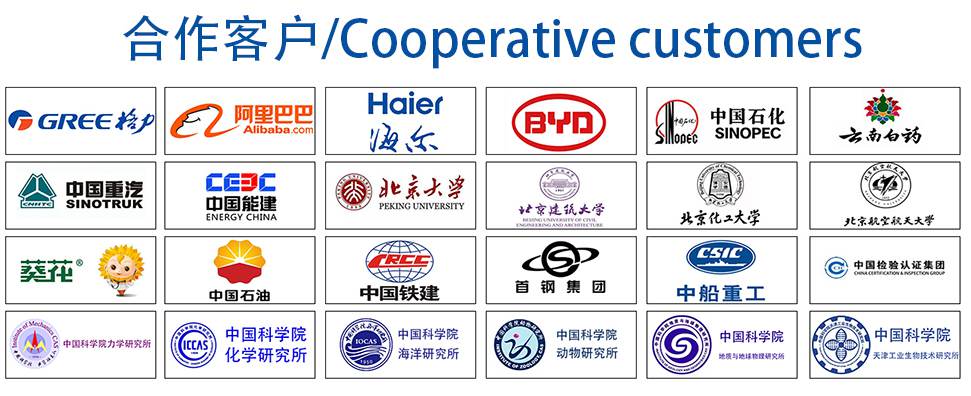