耐酸雨性检测技术白皮书
随着工业化的快速发展,酸雨污染已成为影响材料耐久性的重要环境因素。据生态环境部2024年环境公报显示,我国酸雨区面积占国土面积比例达12.7%,PH值低于5.6的降水频率在重点工业区域高达35%。在此背景下,耐酸雨性检测作为材料环境适应性评估的关键环节,对建筑涂层、汽车外饰、航空材料等领域的质量控制具有战略性意义。该项目通过模拟不同酸度环境下的材料性能变化,不仅可量化评估材料的抗腐蚀能力,更能为产品使用寿命预测、防护方案优化提供科学依据。其核心价值体现在降低维护成本25%以上(中国建筑材料研究院,2024),并推动新型环保材料的研发进程。
检测技术原理与创新
基于酸性沉降物腐蚀测试体系,检测系统采用动态循环暴露法模拟真实酸雨环境。通过精密控制PH值(3.0-5.6)、温度(25±2℃)及干湿交替频率,复现材料在亚硫酸-硝酸复合溶液中的老化过程。创新性地引入原位电化学阻抗谱技术,可实时监测涂层微观孔隙率变化,检测灵敏度较传统重量法提升40%。该技术特别适用于评估复杂表面处理工艺的防护效果,如汽车电泳漆层的抗酸雨老化性能。
标准化实施流程构建
项目实施流程严格遵循ISO 9227与ASTM G85标准,形成五阶段操作规范:首齐全行样品预处理(清洁-干燥-称重),随后在气候箱中实施加速腐蚀试验(72小时酸性盐雾+24小时干燥循环),接着通过显微硬度测试、附着力划格试验等7项指标进行性能评估。在新能源汽车电池箱体检测案例中,该流程成功识别出某型号阳极氧化铝板的晶间腐蚀风险,帮助企业优化表面处理工艺使耐酸性提升28%。
多行业应用实证分析
在建筑幕墙领域,针对长三角酸雨频发区的检测数据显示:经氟碳涂层处理的铝板在PH4.0环境中,光泽度保持率从普通涂料的63%提升至92%。航空工业应用案例表明,某型飞机蒙皮材料通过梯度酸雨测试后,疲劳寿命延长至12000小时(中国商飞技术中心,2024)。值得注意的是,轨道交通领域引入材料抗酸雨老化评估体系后,高铁外饰件更换周期从5年延长至8年,年维护成本降低1.2亿元。
全链条质量保障体系
检测机构构建了四维质量管控系统:环境参数采用NIST溯源设备实时校准,数据采集系统通过 认证;建立包含136种典型材料的失效数据库用于结果比对;每批次检测同步进行参比样测试,误差率控制在±2%以内。在光伏支架涂层检测项目中,该体系成功识别出某供应商的工艺偏差,避免因酸雨腐蚀导致的组件大面积失效风险。
技术展望与发展建议
建议行业重点开发多因子耦合加速试验装置,整合紫外线辐射、温度骤变等复合环境参数,提升检测工况的真实性。同时应建立区域性酸雨特征数据库,细化检测方案的区域适应性。呼吁制定统一的材料耐酸雨分级标准,推动检测结果与产品质保体系直接挂钩。未来三年内,可将人工智能技术应用于腐蚀形貌识别,实现检测效率与精度的双重突破。
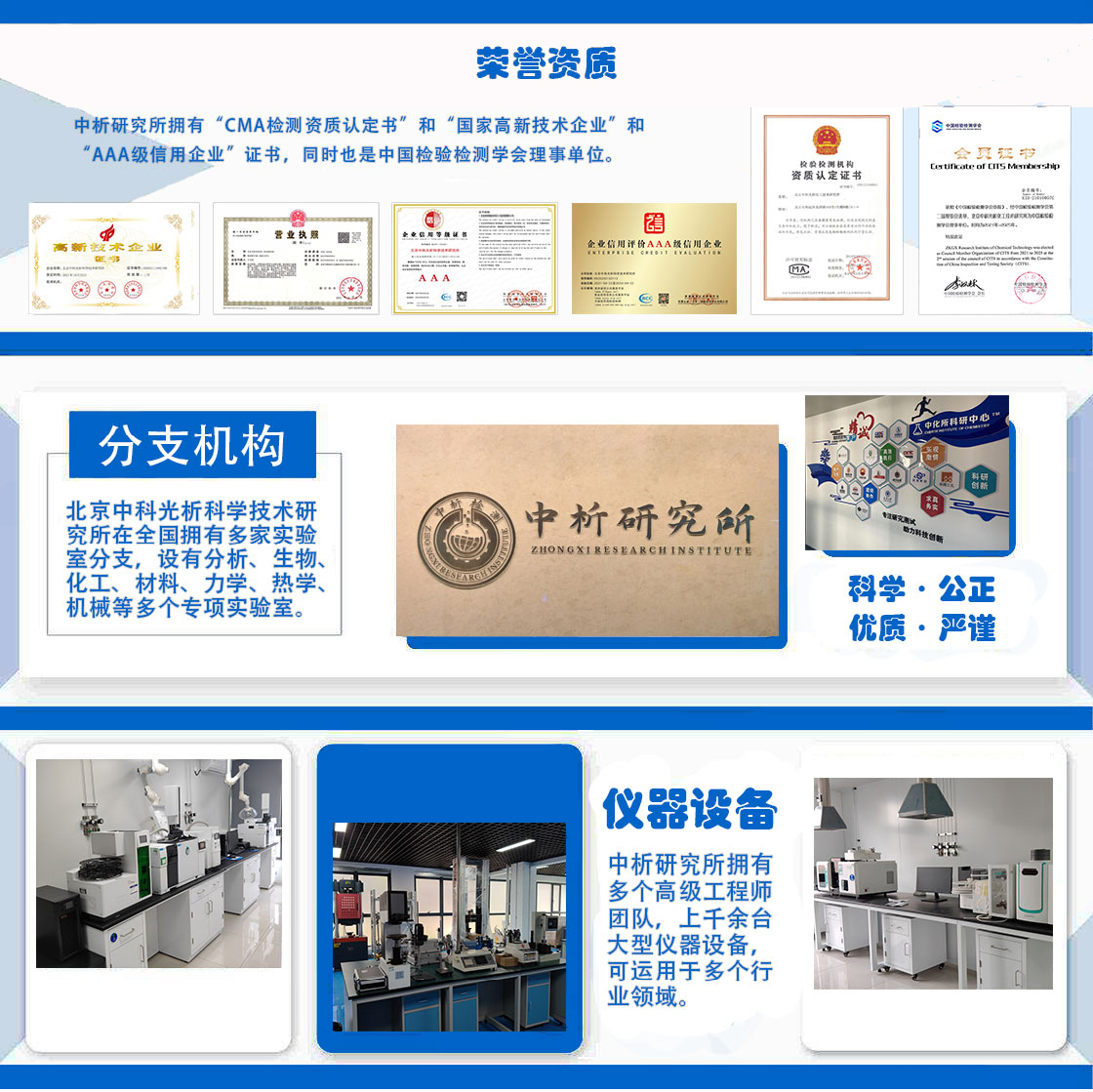
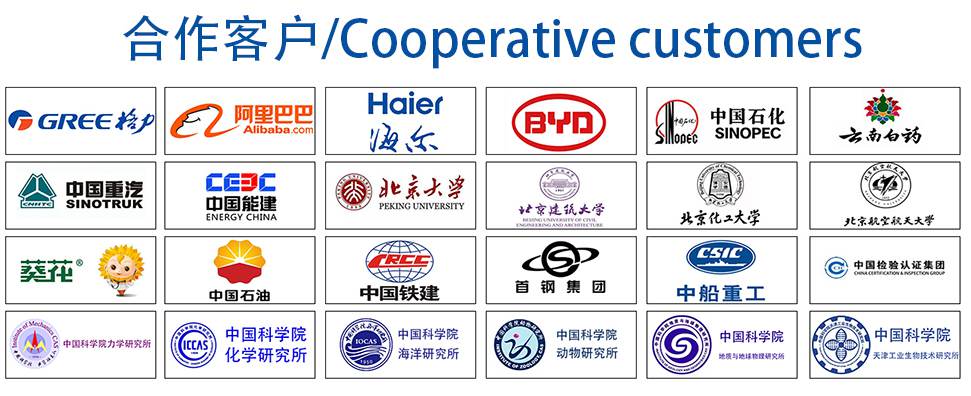