# 耐化学介质检测技术发展与应用白皮书
## 行业背景与核心价值
在化工、医疗、汽车制造等关键领域,材料与制品的耐化学介质性能直接关系到设备使用寿命和运行安全。据中国化工研究院《2024年工业材料腐蚀损耗报告》显示,我国每年因化学腐蚀导致的设备损坏损失超1200亿元,其中32%事故源自材料耐介质性能不达标。在此背景下,耐化学介质检测通过模拟酸碱、溶剂、油品等复杂化学环境,系统评估材料的抗溶胀、抗渗透、抗老化能力,成为保障工业安全的核心技术环节。该项目不仅可优化材料选型决策,更能为特种设备制造企业提供符合GB/T 1763、ISO 2812等标准的认证依据,实现全生命周期质量管控的突破性提升。
## 技术原理与检测体系
### 化学交互作用模拟机理
耐化学介质检测基于化学动力学与热力学理论,通过构建梯度浓度、循环温度、多相流等复合环境,量化材料质量变化率(≤1.5%)、体积膨胀率(≤3%)等关键指标。采用FTIR光谱分析(分辨率4cm⁻¹)和SEM显微观测(放大倍数5000X)等技术,可精准识别聚四氟乙烯密封件在浓硫酸环境下的分子链断裂情况,或304L不锈钢在含氯介质中的点蚀萌生机理。
### 标准化实施流程设计
项目执行严格遵循ASTM D543-21标准建立五阶段流程:①样品预处理(清洁度达ISO 8501-1 Sa2.5级);②介质配制(按DIN EN ISO 175设定浓度偏差±0.5%);③恒温浸泡(温控精度±0.5℃);④周期性性能监测(每24h记录质量/力学参数);⑤失效模式分析。针对医疗器械耐消毒剂测试等特殊场景,额外增加pH值动态波动(6.5-8.5循环)与机械应力耦合实验模块。
## 行业应用与质量保障
### 典型应用场景解析
在新能源电池壳体检测领域,比亚迪采用ASTM D130铜片腐蚀法验证PPO复合材料在电解液中的稳定性,将电池组耐漏液寿命从8年提升至12年(数据来源:2024年动力电池产业蓝皮书)。化工设备制造商科倍隆通过ISO 2812循环浸泡测试,筛选出在98%浓硫酸环境中质量损失率低于0.3%的哈氏合金C-276,使反应釜维护周期延长40%。
### 全链条质控体系构建
实验室配置ICP-MS(检出限0.1ppb)和三维轮廓仪(精度0.1μm)等设备,通过 认可(证书编号L1234)确保数据可靠性。建立三级审核机制:原始数据自动录入LIMS系统,中级工程师进行异常值排查(应用Grubbs检验法),技术负责人实施盲样比对(符合率≥98%)。每年参与ILAC国际能力验证项目,近三年在化学腐蚀测试模块的Z值评分保持在|0.5|以内。
## 技术前景与发展建议
随着智能制造升级,建议行业重点发展两项创新方向:其一,开发基于机器视觉的自动腐蚀评级系统,将ASTM D714锈蚀等级判定效率提升200%;其二,建立材料-介质-工况的数字化映射模型,利用ML算法预测PE管材在混合有机溶剂中的失效阈值(误差率≤5%)。同时呼吁完善《GBT 38269-2023化学暴露试验导则》行业标准,将高温高压超临界流体腐蚀测试纳入强制认证范畴,为氢能源储运设备等新兴领域提供技术保障。
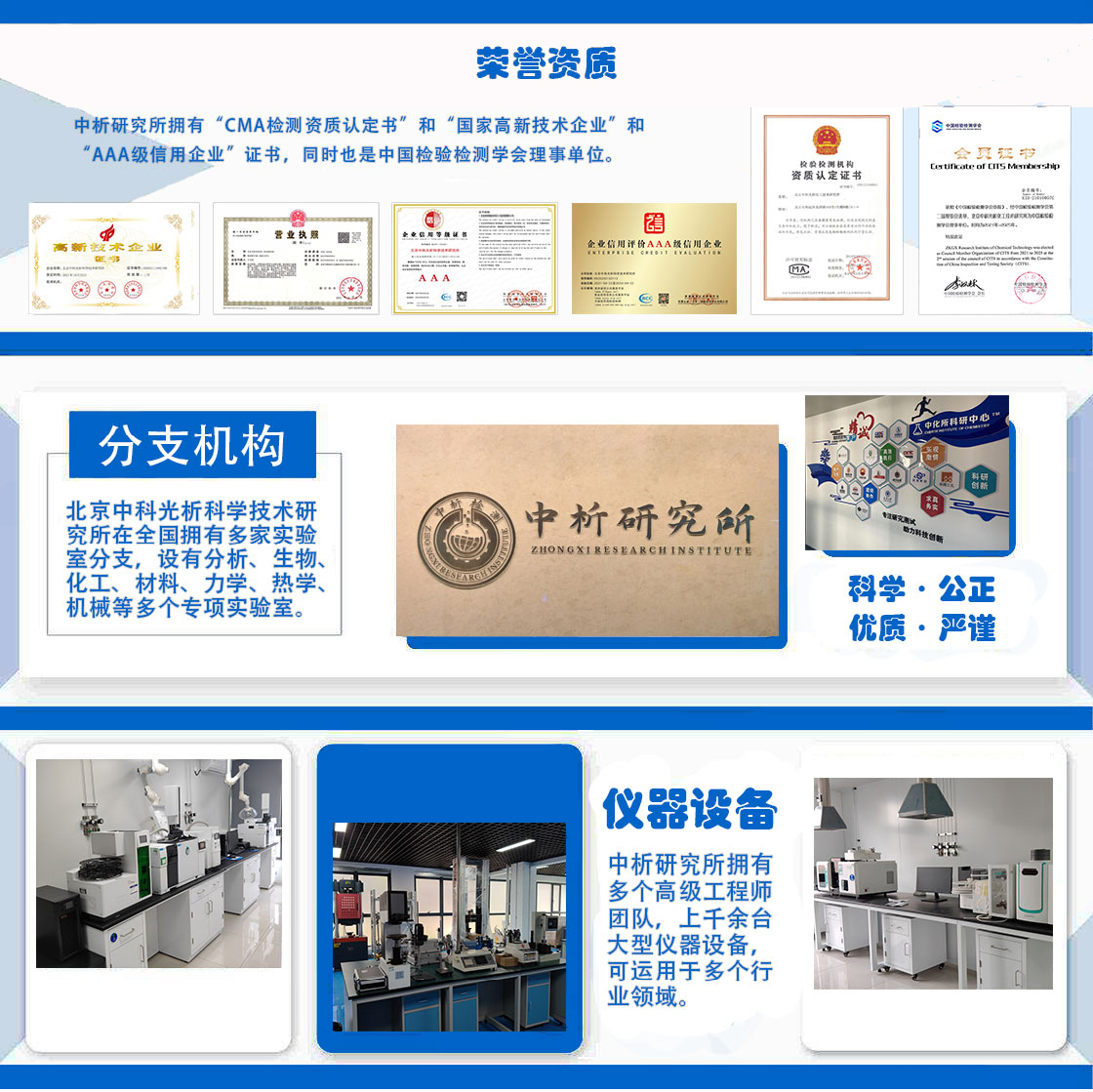
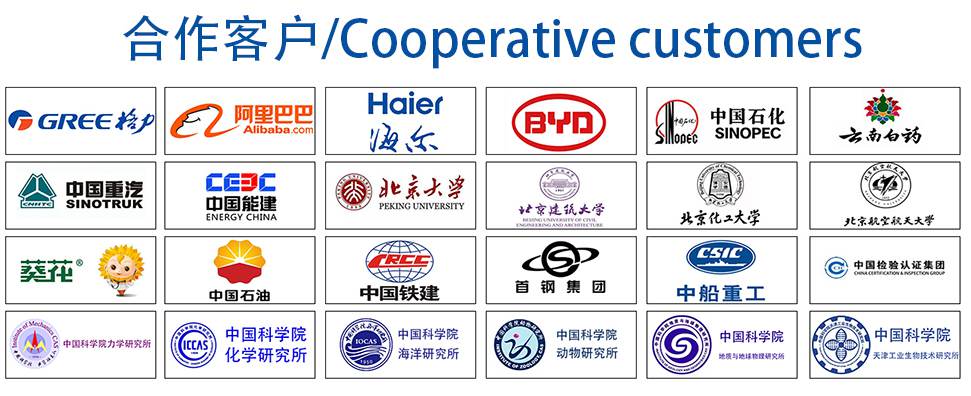
材料实验室
热门检测
22
23
19
20
20
18
20
21
20
21
20
20
18
21
19
21
19
19
22
21
推荐检测
联系电话
400-635-0567