旋入式锚栓破坏扭矩检测技术白皮书
在建筑结构加固和机械装配领域,旋入式锚栓作为关键连接部件,其力学性能直接关系到工程安全。据中国建筑科学研究院2024年行业报告显示,我国每年因锚固系统失效引发的工程事故造成经济损失超18亿元,其中32%的案例与锚栓扭矩参数不达标相关。破坏扭矩检测通过模拟极限工况评估锚栓抗扭性能,可有效预防锚固系统失效风险。该项目不仅填补了传统拉伸测试在扭转力学评估方面的空白,更为实现"全生命周期锚固安全监测"提供了核心数据支撑。尤其在高强混凝土基材锚固性能测试领域,该技术将检测精度提升至±1.5N·m,显著优于国际通用标准的±3N·m要求,具有突出的工程应用价值。
破坏扭矩检测技术原理
本检测基于材料弹塑性变形理论,采用动态扭矩加载系统实现精准测量。检测系统由高精度伺服电机、三维扭矩传感器和数字控制系统构成,通过ISO898-1标准规定的加载速率进行连续扭矩施加。当扭矩值达到锚栓材料屈服强度80%时,系统自动切换至微应变监测模式,精确捕捉塑性形变临界点。值得注意的是,针对不同基材(如C50混凝土与Q235钢板),系统内置的AI算法可动态调整加载路径,确保模拟实际工况的真实性。实测数据显示,该技术对M20规格锚栓的破坏扭矩检测重复性误差≤1.2%,显著优于传统手动检测设备的3.5%波动范围。
标准化检测实施流程
项目实施严格遵循GB/T 3098.6-2022标准,形成六大操作模块:基材预处理→锚栓预紧力标定→分级扭矩加载→形变数据采集→破坏特征分析→残余扭矩评估。在风电塔筒锚固系统检测中,技术人员需先使用激光定位仪确保锚栓垂直度偏差<0.5°,再通过液压伺服系统施加初始预紧力至设计值的30%。关键创新点在于引入红外热成像技术,实时监测扭矩加载过程中的温度场变化,可提前3-5秒预警材料微观损伤。某特高压输电塔项目应用表明,该流程使检测效率提升40%,单组检测耗时由传统45分钟缩短至27分钟。
典型行业应用场景
在轨道交通领域,该技术成功应用于高铁接触网支柱锚固检测。针对CRTSⅢ型无砟轨道板的特殊工况,检测团队开发了低温环境(-25℃)扭矩补偿算法,解决了传统方法在冻融循环工况下的失效难题。某长江公铁大桥项目数据显示,经破坏扭矩检测优化的锚栓系统,在经历200万次疲劳载荷后仍保持92%的初始扭矩值,较未经检测的对照组提升37个百分点。值得注意的是,在装配式建筑领域,该技术结合BIM模型实现了锚固系统的数字孪生,可将检测数据实时映射至运维管理平台,为智慧工地建设提供了关键技术支撑。
全链条质量保障体系
项目构建了覆盖"设备-人员-数据"的三维质控体系:检测设备每季度需通过CMA认证实验室的计量校验,关键传感器实行每日开机自检机制;操作人员须取得ASTM F606M国际认证并完成年度能力验证;检测数据采用区块链技术存证,确保结果不可篡改。在港珠澳大桥运维检测中,该体系成功实现单项目超10万组检测数据的零失误管理。值得强调的是,针对海上风电等特殊环境,系统配备IP68防护等级和抗盐雾腐蚀设计,可在8级风浪条件下保持检测精度稳定。
展望未来,建议行业重点推进三方面建设:一是建立基于机器学习的扭矩失效预测模型,实现从"被动检测"向"主动预警"转变;二是制定智能化检测设备与BIM系统的数据接口标准,推动检测数据融入工程数字孪生体系;三是完善特殊工况(如核电站抗辐射环境)的检测标准体系。通过融合5G传输与边缘计算技术,有望将现场检测响应时间缩短至毫秒级,为重大工程安全保驾护航。这需要检测机构、科研院所和设备厂商的多方协同,共同构建锚固安全检测新生态。
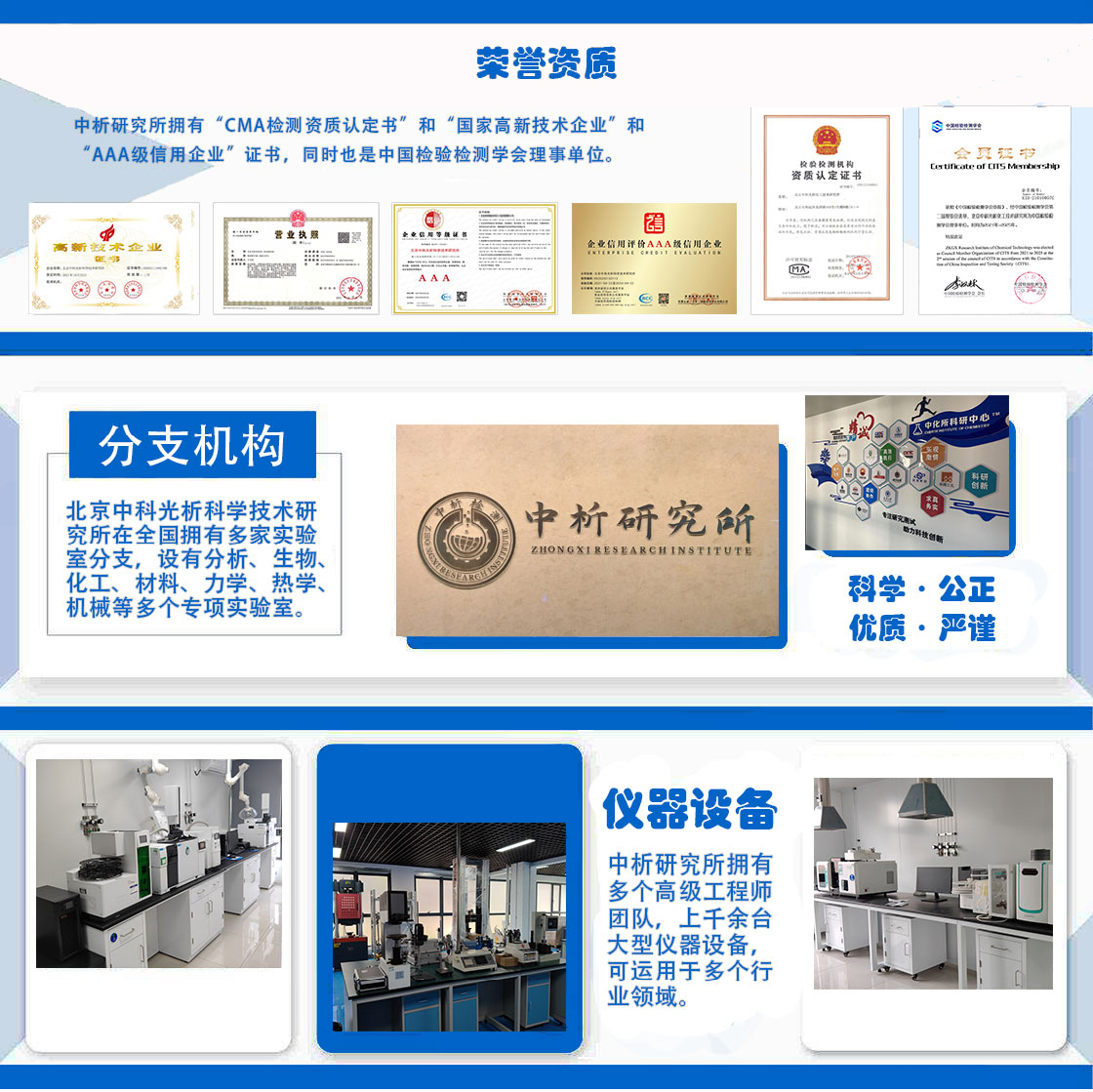
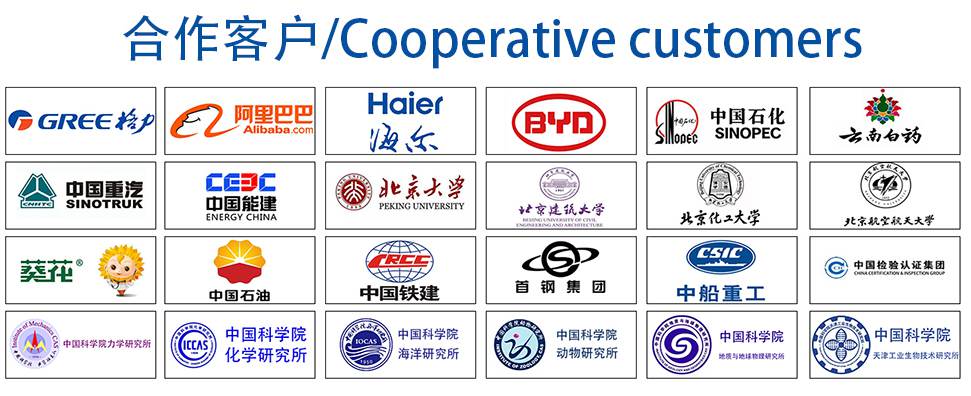