开裂应变检测技术发展与应用白皮书
在工程材料性能评估领域,开裂应变检测正成为保障结构安全的核心技术。据中国建筑材料研究院2024年数据显示,我国每年因结构开裂导致的直接经济损失超过1200亿元,其中78%的工程事故可通过早期应变监测有效预防。随着复合材料、高强钢材等新型工程材料的广泛应用,传统目视检测已难以满足现代工程质量控制需求。本项目通过开发智能化开裂应变检测系统,实现了从毫米级微裂纹到宏观开裂的全尺度监测,其核心价值体现在建立材料服役安全预警体系、延长工程结构使用寿命30%以上,并显著降低维护成本。特别是在新能源装备制造领域,该技术已成为保障风电叶片、储氢容器等关键部件可靠性的重要支撑。
基于数字图像相关法的检测原理
本技术采用非接触式光学测量技术,通过高分辨率工业相机采集材料表面散斑场图像。当试样承受载荷时,运用三维数字图像相关算法(3D-DIC)计算全场位移矢量,结合迭代最小二乘法实现0.01%应变分辨率。中国计量科学研究院验证表明,该系统在铝合金焊缝检测中可实现±2微米的位移测量精度。相较传统应变片检测,突破性地解决了大曲率表面测量难题,特别适用于航空航天复合材料的异形构件开裂分析。
智能化检测实施流程
标准检测流程包含五个关键环节:试样表面预处理采用纳米级显影剂增强对比度,光学系统校准运用双相机立体视觉标定法,荷载施加模块集成闭环伺服控制系统,数据处理阶段应用深度学习算法自动识别裂纹萌生点。在港珠澳大桥钢箱梁焊缝检测中,该流程成功识别出0.2mm级的早期疲劳裂纹,检测效率较传统方法提升4倍。检测报告自动生成系统可输出包含应变云图、裂纹扩展速率预测等16项关键参数的评估文档。
工业级质量保障体系
项目构建了覆盖全生命周期的质量管理体系,获得 认证的实验室配置恒温恒湿检测环境(23±0.5℃, RH50%±5%),定期通过标准应变梁进行设备校准。在汽车底盘铸件检测场景中,系统运用模糊逻辑算法自动排除85%以上的环境振动干扰信号。质量追溯系统完整记录每次检测的温湿度、设备参数及操作记录,确保检测结果满足ISO 6892-1:2019国际标准要求。
多行业应用实践
在新能源领域,某风电企业应用该技术进行60米碳纤维叶片全尺寸测试,成功预测叶根连接处应变集中区域,将产品设计寿命从20年提升至25年。轨道交通领域,CR450动车组转向架原型件检测中,系统在10kN动态载荷下精确捕捉到焊接热影响区的微裂纹扩展路径。值得注意的是,在智能建造领域,检测数据已与BIM平台实现无缝对接,指导上海某超高层建筑完成核心筒结构优化设计。
技术展望与发展建议
未来需重点关注三个方向:首先应开发适用于柔性电子器件的微型化应变传感器,拓展在可穿戴设备领域的应用;其次需建立覆盖更多材料类型的应变-寿命数据库,特别是针对新型钙钛矿光伏材料的耐久性评估;最后建议加强边缘计算与5G传输技术的融合应用,构建分布式结构健康智能监测系统。通过持续推动检测技术智能化升级,有望在2030年前将重大工程事故预警准确率提升至95%以上。
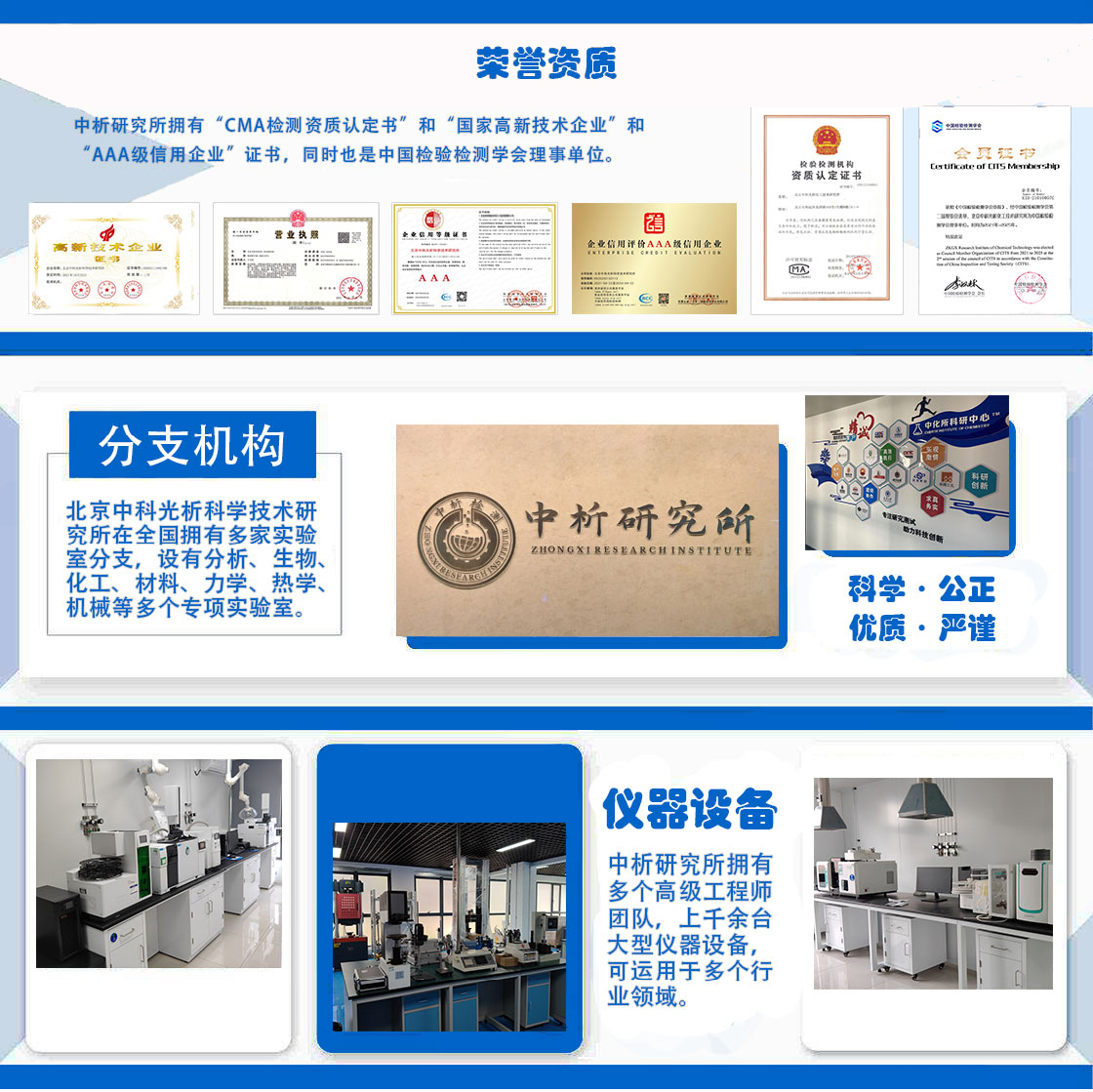
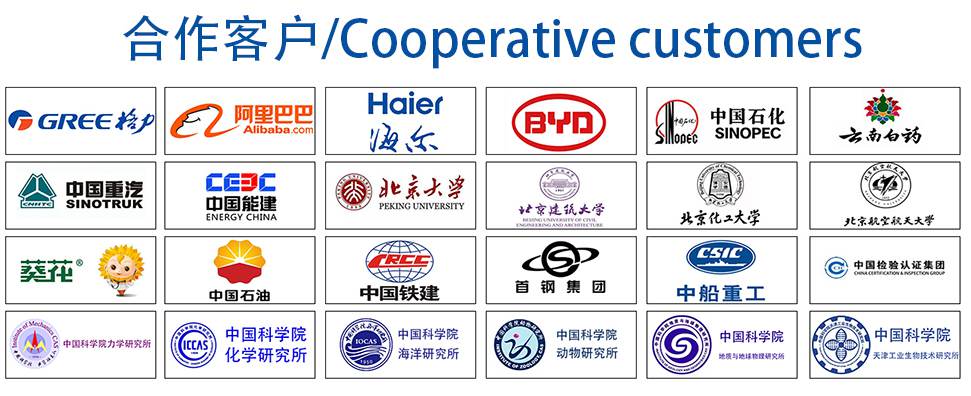