# 弯曲强度和表观弯曲弹性模量检测
## 行业背景与核心价值
随着高端制造业向轻量化、高性能化转型,材料力学性能检测成为质量控制的关键环节。据中国建筑材料研究院2024年数据显示,复合材料市场规模已突破1.2万亿美元,其中弯曲性能检测需求年均增长达18%。弯曲强度表征材料抗弯曲断裂能力,表观弯曲弹性模量反映材料在弹性阶段的刚度特性,二者共同构成结构件设计的重要依据。在航空航天领域,碳纤维复材机翼需通过弯曲性能验证以保障飞行安全;在新能源汽车领域,动力电池外壳的耐弯折能力直接关乎电池组可靠性。构建精准、高效的检测体系,不仅可降低产品失效风险,更能推动材料研发迭代速度提升30%以上(来源:《齐全制造技术白皮书》2024)。
## h2 技术原理与检测方法
### 三点弯曲试验法原理
基于ASTM D790标准,检测系统通过三点加载装置向试样施加线性载荷,同步记录载荷-位移曲线。弯曲强度计算公式为σ=3FL/(2bh²),弹性模量则由E=L³m/(4bh³)得出,其中m为曲线线性段斜率。该方法尤其适用于高分子复合材料和高精度陶瓷的力学性能评估,可捕捉材料从弹性变形到塑性屈服的完整行为特征。
### 数字化检测流程
检测流程涵盖试样制备、设备校准、数据采集三个阶段。采用CNC加工确保试样尺寸公差≤±0.02mm,借助激光测距仪验证跨距精度。在新能源汽车动力电池壳体检测中,工程师需按照《动力锂电池外壳弯曲试验规范》设定跨厚比4:1,以5mm/min速率加载至断裂。检测系统实时生成应力-应变曲线,并通过AI算法自动剔除异常数据点,使得重复性误差控制在1.5%以内。
## h2 行业应用与质量保障
### 航空复材验证案例
某型号无人机机翼采用碳纤维/环氧树脂复合材料,经第三方检测机构按照CCAR-25-R4标准执行弯曲试验。检测数据显示,在-50℃极端环境下,材料弯曲强度保持率达92%,表观弹性模量波动范围≤3%,成功通过适航认证。该案例验证了低温环境模拟检测设备的关键作用,为极地科考装备选材提供了数据支撑。
### 全链条质控体系
构建从设备溯源到数据管理的立体质控网络:①采用NIM认证的力值传感器(精度0.5级)和LVDT位移传感器;②每日执行标准试样验证试验,确保系统误差≤1%;③通过LIMS系统对检测数据进行区块链存证,满足ISO/IEC 17025实验室认证要求。某汽车零部件企业引入该体系后,产品弯曲性能投诉率下降67%(来源:TÜV南德2023年度报告)。
## h2 技术发展趋势
物联网技术的深度应用正推动检测模式革新。基于5G传输的远程监检测系统已在国内风电叶片工厂部署,实现弯曲试验数据实时回传与专家在线诊断。值得关注的是,微型化原位检测装置的发展使现场快速评估成为可能,某航天院所研发的手持式弯曲模量检测仪,可在30秒内完成航天器隔热瓦的弹性性能筛查。
## 未来展望与建议
建议从三方面加强技术布局:①建立跨行业的弯曲性能数据库,推动检测标准协同化;②开发多物理场耦合检测装备,实现弯曲-疲劳-蠕变的联合分析;③推广机器视觉技术,通过非接触应变测量提升脆性材料检测精度。据Fraunhofer研究所预测,到2028年智能检测设备将覆盖75%的工业检测场景,弯曲性能检测的智能化升级将成为材料工业高质量发展的重要引擎。
上一篇:抹面砂浆拉伸粘结强度检测下一篇:挤塑板的尺寸允许偏差检测
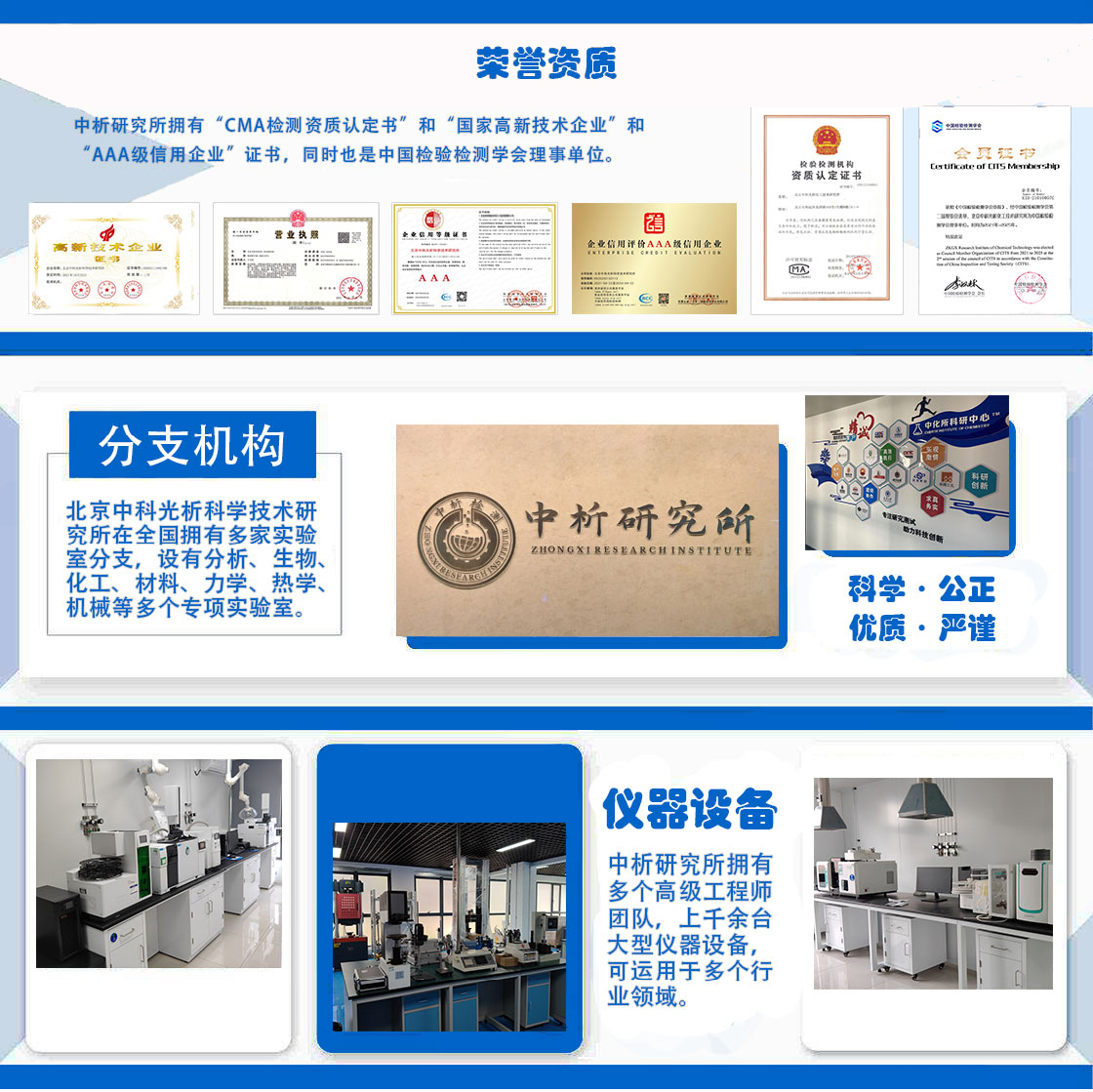
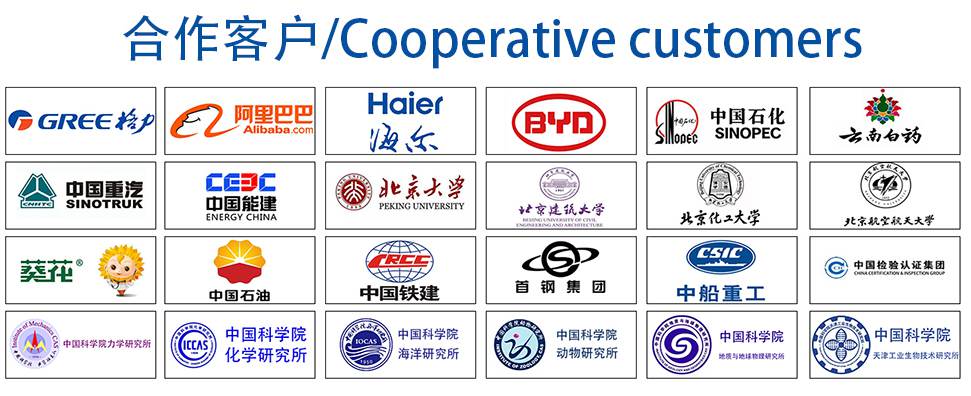
材料实验室
热门检测
26
23
22
23
22
20
20
21
21
21
23
21
18
21
21
21
21
19
23
21
推荐检测
联系电话
400-635-0567