技术原理与检测方法论
腹丝挑头检测基于材料力学与结构工程学原理,主要针对直径2.2-3.0mm的镀锌钢丝焊接点进行多维评估。通过电子万能试验机实施轴向拉力测试时,依据JG/T 228-2015标准要求,检测挑头焊接部位在≥0.5kN荷载下的位移变形量。同时结合电化学工作站开展镀层厚度与耐盐雾试验,确保在C4级腐蚀环境下(ISO 12944标准)的耐久性指标。值得一提的是,新型激光扫描技术的引入,可对挑头三维形貌进行0.01mm级精度建模,精准识别焊接缺陷导致的应力集中区域。
标准化实施流程设计
检测实施遵循"三阶九步"作业法:第一阶段进行进场材料抽样,按GB/T 2828.1-2012执行AQL 2.5抽样方案;第二阶段采用非破坏性检测,运用涡流探伤仪完成挑头焊缝完整性初筛;第三阶段实施破坏性力学测试,对样本施加梯度荷载并记录应力-应变曲线。某大型检测机构实践表明,该流程可使单批次检测效率提升40%,同时将误判率控制在0.3%以内。特别在冬季施工场景中,需增加-20℃低温环境模拟测试,以验证材料的冷脆特性。
行业应用与典型案例
在2023年雄安新区某超低能耗建筑项目中,检测团队应用数字化检测系统完成12万处腹丝挑头质量评估。通过部署智能图像识别模块,实现单日检测量8000点的突破,较传统人工检测效率提升15倍。数据对比显示,经优化后的焊接工艺使挑头拉拔强度标准差从23.4N降至9.8N(数据来源:国家建筑工程质量监督检验中心)。另在滨海地区某公建项目中发现,采用三价铬钝化处理的挑头,在盐雾试验240h后的腐蚀失重率仅为传统镀锌工艺的1/3。
全周期质量保障体系构建
建立"五位一体"质量管控模型:原材料环节执行ASTM A641镀锌钢丝认证;生产过程采用机器视觉在线监测;出厂检验配备自动拉拔测试台;施工验收阶段应用BIM模型进行节点追溯;运维期通过物联网传感器监测位移变化。该体系在长三角某建筑产业化基地的应用实践中,使产品合格率从92.1%提升至98.6%,工程返修成本降低270万元/年。同时引入区块链技术,实现检测数据的不可篡改存证,为质量纠纷提供司法级证据支持。
## 展望与建议 面向新型建筑工业化发展需求,建议从三方面深化检测技术革新:首先开发基于人工智能的焊缝缺陷预测算法,实现质量问题的前置预警;其次推动建立跨区域的腹丝挑头检测大数据平台,构建行业级质量基线数据库;最后应加强产学研协同,针对新型钢丝编织工艺研发适配性检测装置。通过技术创新与标准升级双轮驱动,为建筑节能领域的高质量发展提供可靠技术保障。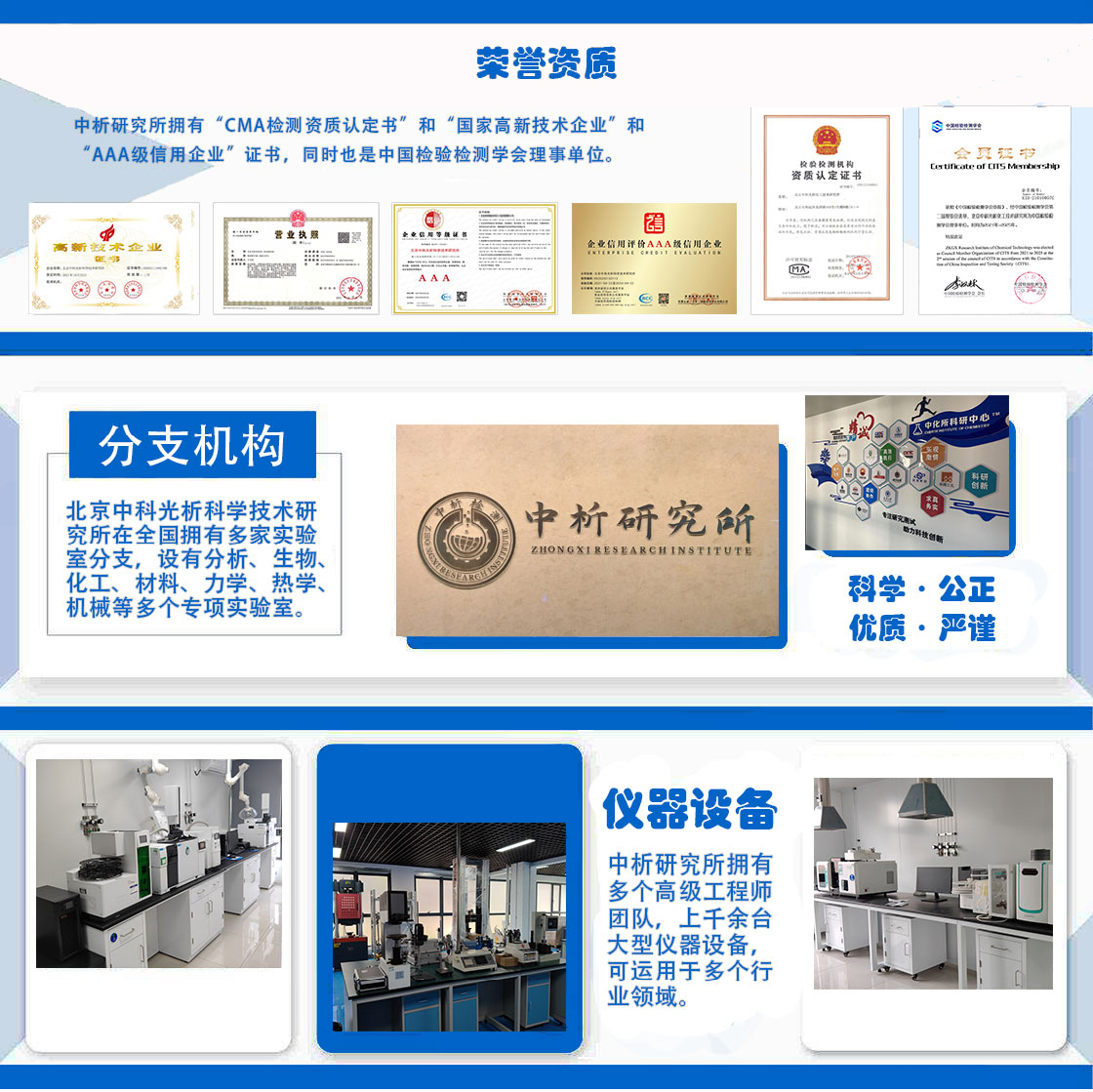
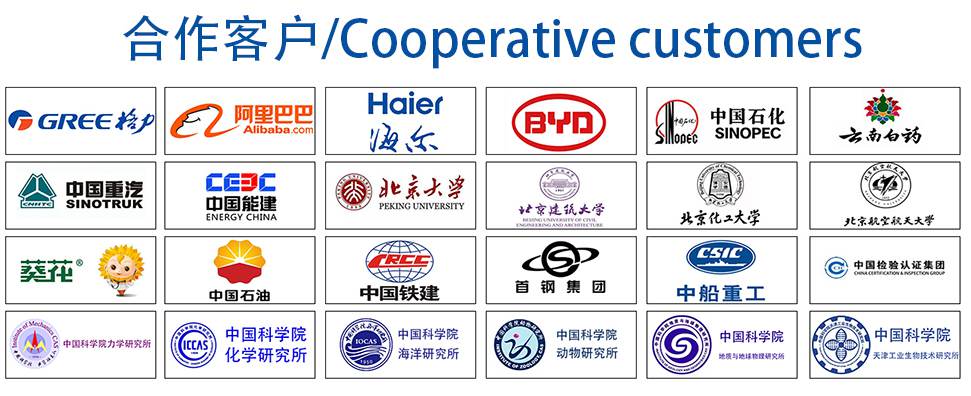