外观疵点检测
发布时间:2025-08-02 22:00:24- 点击数: - 关键词:
实验室拥有众多大型仪器及各类分析检测设备,研究所长期与各大企业、高校和科研院所保持合作伙伴关系,始终以科学研究为首任,以客户为中心,不断提高自身综合检测能力和水平,致力于成为全国科学材料研发领域服务平台。
立即咨询外观疵点检测:核心检测项目与技术解析
一、外观疵点检测的核心意义
- 质量管控:避免瑕疵品流入市场;
- 成本优化:减少返工和报废成本;
- 工艺改进:通过缺陷分析优化生产流程。
二、主要检测项目分类与详解
1. 表面缺陷检测
2. 颜色与纹理一致性检测
3. 尺寸与形位公差检测
4. 装配与封装完整性检测
三、检测技术发展趋势
- 深度学习突破:基于CNN的缺陷分类模型可识别复杂纹理背景下的细微瑕疵(如织物暗斑),误检率低于0.5%。
- 多传感器融合:结合3D视觉、热成像和声学检测,实现全维度质量评估。
- 实时化与边缘计算:嵌入式视觉系统可在产线实现毫秒级响应,单工作站检测速度达2000件/分钟。
四、检测标准与实施建议
- 国际标准参考:ISO 9001(质量管理)、ASTM E1951(外观检验规程)。
- 企业实施要点:
- 根据产品特性定制检测参数阈值;
- 定期校准设备并更新缺陷样本库;
- 融合SPC统计过程控制实现预防性质检。
结语
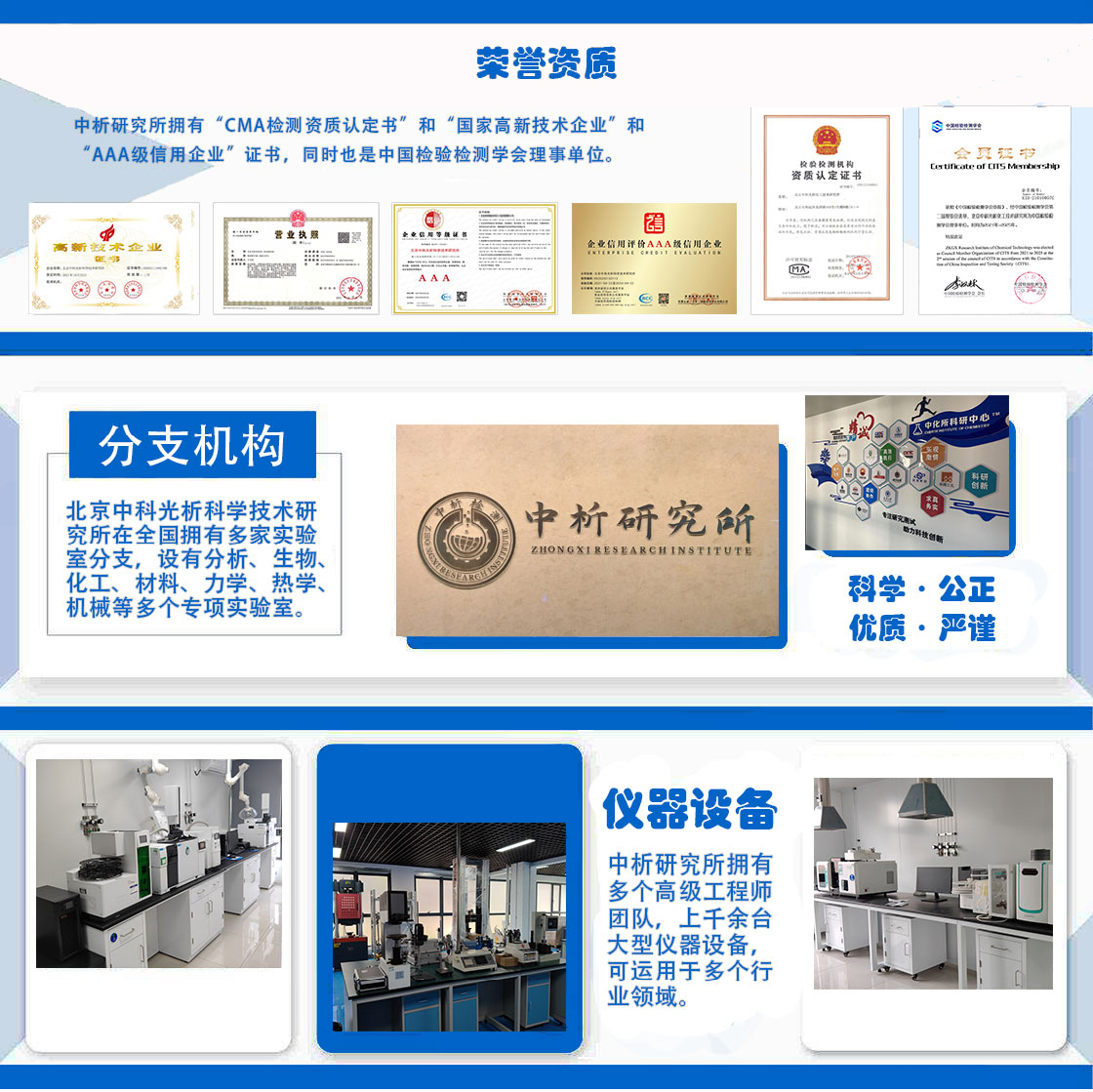
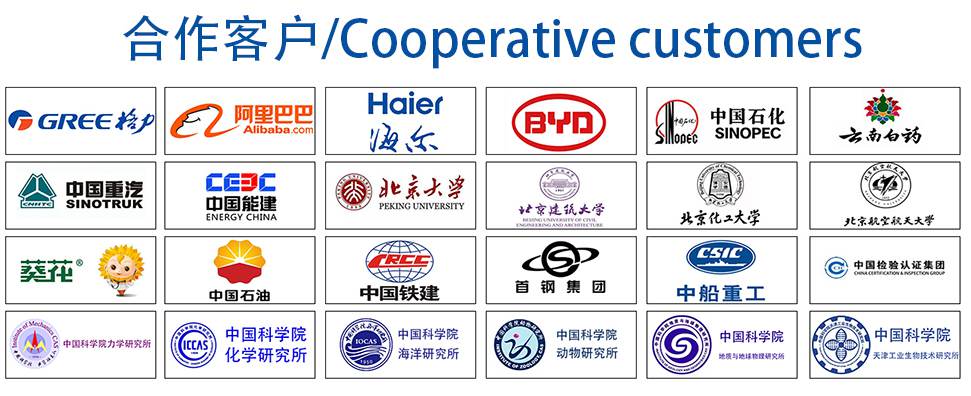
材料实验室
热门检测
139
132
128
151
105
126
141
130
118
114
139
119
121
121
127
119
120
127
107
118
推荐检测
联系电话
400-635-0567