缝毡缝合质量检测
发布时间:2025-08-03 09:44:01- 点击数: - 关键词:
实验室拥有众多大型仪器及各类分析检测设备,研究所长期与各大企业、高校和科研院所保持合作伙伴关系,始终以科学研究为首任,以客户为中心,不断提高自身综合检测能力和水平,致力于成为全国科学材料研发领域服务平台。
立即咨询缝毡缝合质量检测关键项目与技术规范
一、核心检测项目及技术要求
1. 视觉外观检测
- 检测内容:
- 缝合线迹的直线度与均匀性
- 针距误差控制在±1.5mm内(按GB/T 13759标准)
- 线头残留长度≤3mm
- 杜绝跳针(连续5针以上视为严重缺陷)
- 缝线颜色与毡体匹配度(色差ΔE≤1.5 NBS)
- 检测方法: 采用LED冷光源放大镜(50倍)配合标准比色卡,参照ISO 105-J03色牢度评价体系。
2. 尺寸精度验证
- 关键参数:
- 缝合部位宽度偏差≤±2%
- 叠合缝错位量<1.5mm
- 长度方向收缩率≤0.8%(高温工况产品)
- 检测工具: 激光测距仪(精度0.01mm)配合恒温恒湿环境箱(温度23±2℃,湿度50±5% RH)
3. 力学性能测试
(1)缝合强度测试
- 剥离强度: 采用90°剥离试验(ASTM D2724),要求≥150N/5cm(建筑用毡)/≥80N/5cm(民用产品)
- 断裂强力: 万能材料试验机(加载速度100mm/min),接缝处断裂强力需达基材的85%以上
(2)抗滑移性能
- 施加50N预张力后,接缝滑移量≤2mm(参照QB/T 2853标准)
4. 线迹工艺指标
- 线迹密度:
- 常规产品:8-12针/英寸
- 高压密封产品:14-16针/英寸(需配合双针三线链式线迹)
- 张力检测: 使用缝线张力计(测量范围0-50cN),面线与底线张力比控制在1.2:1~1.5:1
5. 环境耐受性测试
- 湿热老化: 温度70℃/湿度95%环境下处理240h,接缝开裂长度<5mm(GB/T 7141)
- 冻融循环: -25℃(16h)→常温解冻(8h),20次循环后接缝强度损失率≤15%
- 化学腐蚀: 在pH=2的H2SO4溶液和pH=12的NaOH溶液中浸泡48h,接缝无分层失效
二、专项检测技术方案
1. X射线探伤检测
- 应用场景:航空航天用高密度缝毡
- 技术参数: 电压80-120kV,电流3-5mA,检测针脚穿透深度及内部线结形态
2. 红外热成像检测
- 检测原理:通过温差分析接缝处热传导均匀性
- 判定标准:接缝区域温差ΔT≤1.5℃(EN 13187)
3. 透气性测试(仅功能性缝毡)
- 测试方法: 使用FX3300透气度测试仪,压差125Pa时透气量偏差≤15%
三、质量管理体系要求
-
- 上线前缝线捻度检测(20捻/10cm±2)
- 每2小时在线张力自动记录
- 针板温度监控(丙纶线<80℃,芳纶线<150℃)
四、常见缺陷成因及改进措施
缺陷类型 | 成因分析 | 解决方案 |
---|---|---|
接缝起皱 | 送布齿磨损/底面线张力失衡 | 更换送布机构/采用差动送料系统 |
线迹漂浮 | 针板孔磨损/压脚压力不足 | 使用镀钛针板/气压压脚压力增至40kPa |
断线率超标 | 针尖粗糙度Ra>0.2μm | 采用纳米涂层机针(摩擦系数降低60%) |
上一篇:抹面砂浆可操作时间检测下一篇:增强竖丝岩棉复合板的尺寸稳定性检测
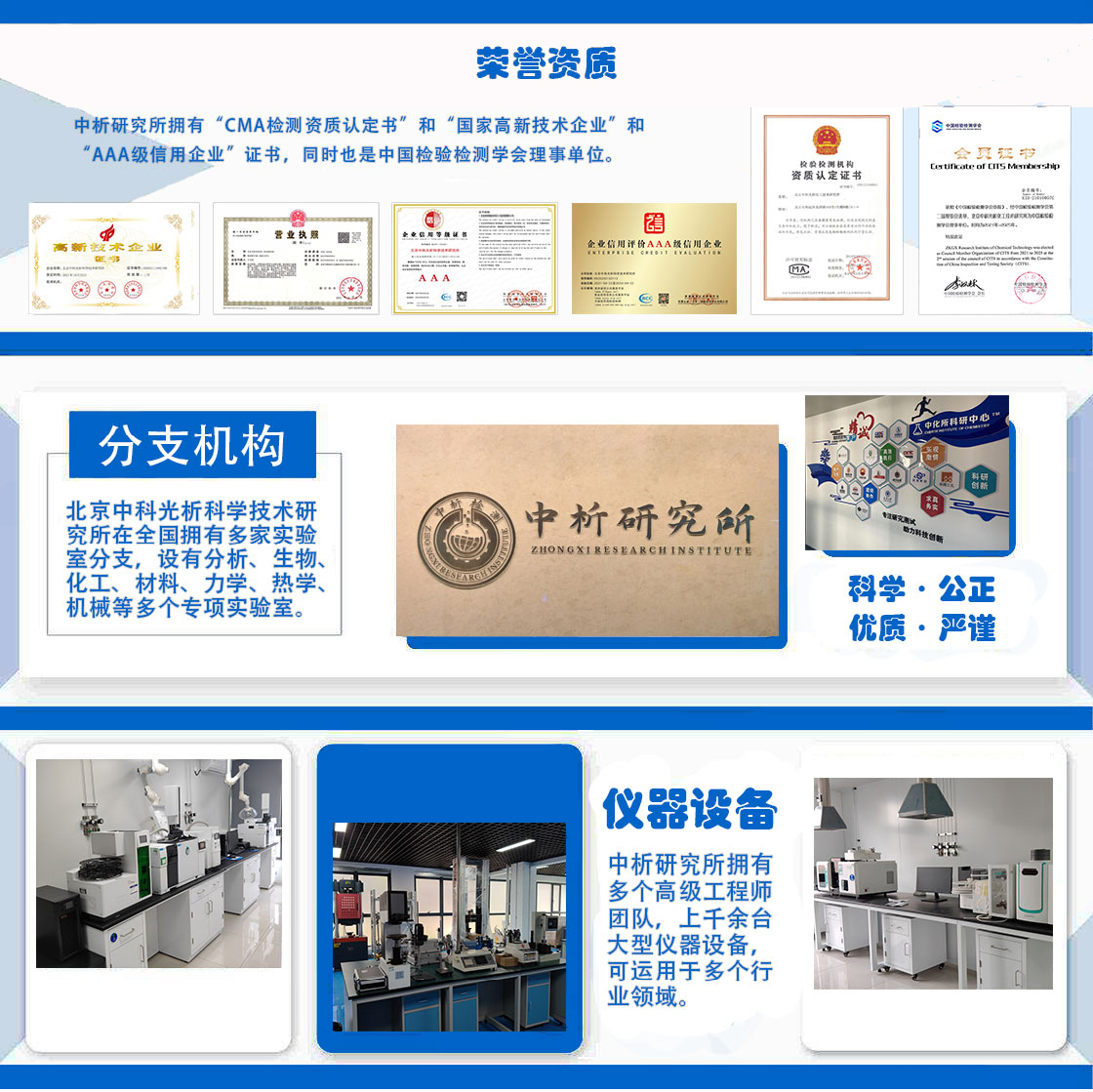
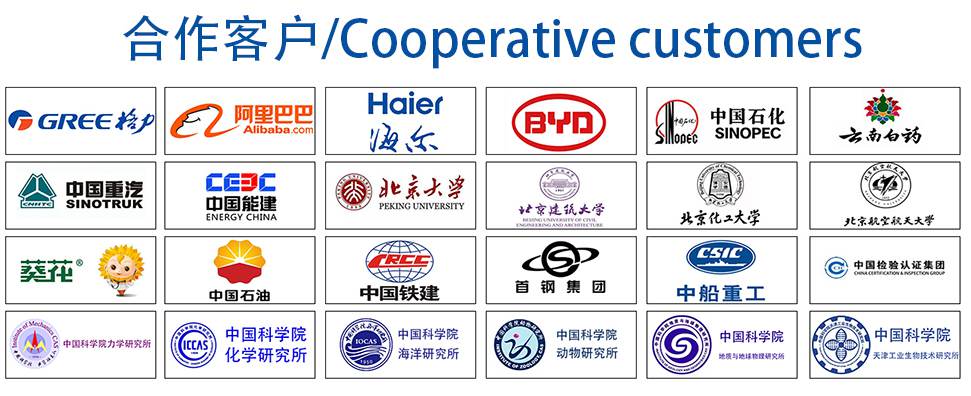
材料实验室
热门检测
140
133
129
152
106
127
142
130
120
116
142
123
123
125
131
124
124
127
111
120
推荐检测
联系电话
400-635-0567