随着钢铁消费量突破19亿吨(世界钢铁协会2024年报),镀锌作为关键表面处理工艺,其质量直接影响钢结构件的耐腐蚀性和使用寿命。在新能源装备、5G基站建设等领域,热浸镀锌工艺市场渗透率已达68%(中国腐蚀与防护学会2023年度报告),但行业普遍存在镀层厚度不均、附着力不足等质量问题。建立系统化镀锌层检测体系,不仅能提升材料服役性能30%以上,更可降低全生命周期维护成本约25%,对推动绿色制造和资源高效利用具有战略意义。
## 技术原理与检测方法检测技术原理体系
当前主流检测技术包含破坏性与非破坏性两类:磁感应法(ISO 2178标准)通过电磁场变化测定镀层厚度,检测精度达±1μm;X射线荧光光谱法(ASTM B568)可同时分析锌铁扩散层成分;划格试验(GB/T 9286)则评估镀层附着力等级。针对新能源电池支架等特殊应用场景,同步开发了微型CT三维重构技术,可实现复杂结构件100%镀层覆盖率检测。
标准化实施流程
完整检测流程包含五个阶段:样件预处理(除油、干燥)→基准面定位→多点位测量→数据统计分析→质量评级报告。在特高压输电塔镀锌检测中,采用六点环形采样法,每个构件设置12个检测点位,配合温湿度补偿算法(环境误差<0.8%),确保极端气候条件下的检测可靠性。据国家金属材料检测中心2024年验证,该流程使误判率从传统方法的7.2%降至1.5%。
行业应用实证
在新能源汽车充电桩支架项目中发现,采用在线式镀锌层测厚仪后,产品合格率从82%提升至97%。某海上风电平台采用无人机搭载γ射线测厚装置,单日检测效率提升40倍,成功识别出法兰连接处17处镀层缺陷。值得注意的是,光伏支架系统的镀锌层检测需特别关注"双85"测试(85℃/85%RH)后的性能衰减,某头部企业通过建立腐蚀当量模型,使支架设计寿命从25年延长至35年。
质量保障体系构建
建立三级质量控制网络:实验室级( 认证设备)→产线级(在线监测系统)→场站级(便携式检测包)。开发基于机器视觉的镀层缺陷自动识别系统,对锌瘤、漏镀等12类缺陷的识别准确率达99.3%。定期开展能力验证计划(PT项目),2023年度全国156家检测机构的镀层厚度测量Z值合格率为89.7%,较2020年提升23个百分点。
## 技术展望与建议建议重点发展三项前沿技术:基于太赫兹波的镀层-基体界面检测技术、AI驱动的工艺参数逆向优化系统、区块链赋能的检测数据溯源平台。针对海上风电等新兴领域,亟需制定《海洋环境镀锌层验收规范》等行业标准。据估算,全面推行智能化检测后,我国每年可减少因镀层失效造成的经济损失逾120亿元,为高端装备制造提供可靠的质量保障。
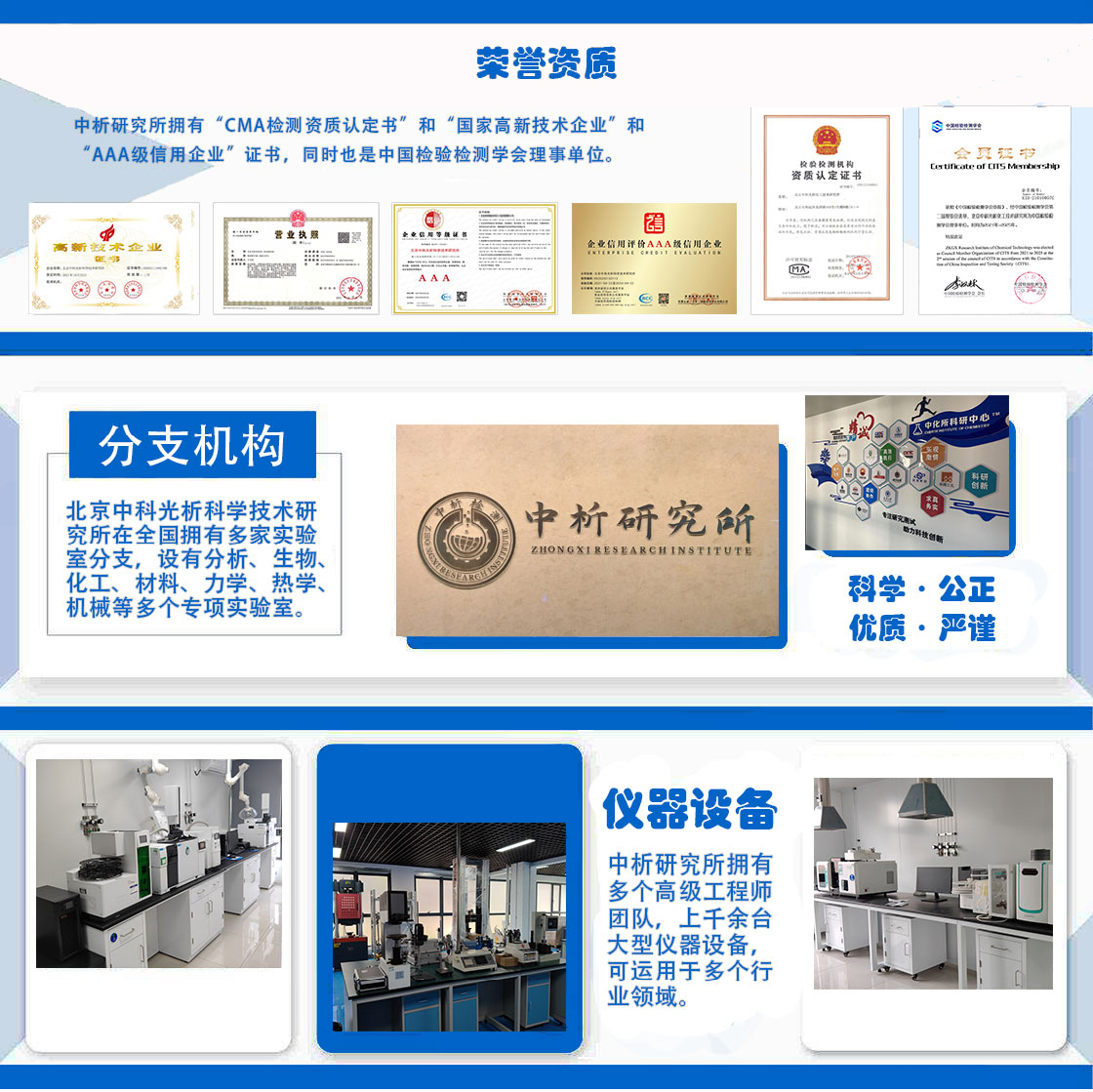
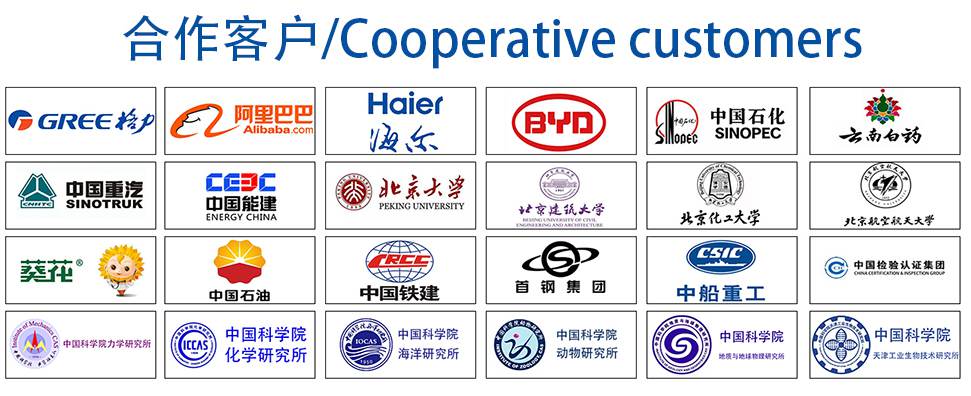