# 气压控制装置检测技术发展与应用白皮书
## 引言
在高端装备制造领域,气压控制装置作为动力系统的核心组件,其性能稳定性直接关系到航空航天、轨道交通、工业自动化等关键行业的运行安全。据中国机械工业联合会2024年行业报告显示,我国气压控制系统市场规模已达870亿元,年均复合增长率达12.5%。然而,由于装置内部压力波动、密封失效等问题导致的设备故障占比高达23%(国家设备安全监测中心,2023),凸显检测技术的战略价值。本项目通过构建智能化检测体系,可实现0.05MPa级压力波动精准识别(ISO 8573-1标准),在保障设备本质安全的同时,将维护成本降低40%以上,形成覆盖产品全生命周期的质量管控闭环。
![气压控制装置检测技术体系示意图]
## 技术原理及创新突破
### 动态压力响应分析技术
基于MEMS传感器阵列与计算流体力学(CFD)仿真模型的融合检测方案,突破了传统静态检测的局限性。该技术通过布置16通道压力采集节点(间距≤5cm),可实时捕捉装置内部0-2.5MPa区间的压力梯度变化。经国家计量院验证,其动态响应时间较传统方法缩短62%,在新能源汽车制动系统检测中成功识别出98.7%的微泄漏点(中国汽车工程学会,2024)。
### 多物理场耦合检测方法
整合温度-压力-振动三场耦合分析算法,构建了具有自学习能力的故障诊断模型。在工业机器人应用场景中,该模型对密封圈老化预测准确率提升至89.3%,误报率控制在2%以内。特别在半导体制造领域,实现了±0.8℃温控精度下的气压稳定性监测,保障了晶圆刻蚀工艺的良品率(SEMI国际半导体协会,2024年度技术白皮书)。
## 标准化实施流程
### 三级检测体系架构
项目建立覆盖组件级(单体测试)、系统级(联调检测)、场景级(工况模拟)的三级检测体系。在轨道交通应用案例中,采用EN 15085标准对制动控制单元进行72小时连续压力循环测试,累计发现23类潜在失效模式,其中15%为传统方法未能识别的间歇性故障。
### 智能化检测工作站
部署集成视觉识别(AOI)与声发射检测(AE)的智能工作站,在航空发动机检测环节实现98%的自动化率。某型号涡扇发动机进气调节装置检测周期从12小时缩短至3.5小时,同时生成包含17项关键参数的数字化检测报告(SAE航空航天标准AS9100D认证)。
## 行业应用成效分析
### 新能源汽车领域突破
在比亚迪某车型产线应用中,"高精度气压波动分析"技术使电池组冷却系统检测效率提升300%,泄漏检测灵敏度达到5×10⁻⁶ mbar·L/s。据企业实测数据,该方案帮助产线年节约质量成本2400万元,产品召回率下降67%。
### 智能装备制造实践
三一重工采用"智能化密封性检测系统"后,液压控制阀组装机合格率从92.4%提升至99.1%。通过建立压力衰减曲线数据库,实现故障根因的智能溯源,平均维修决策时间缩短83%。
## 质量保证体系建设
### 全链条溯源机制
构建基于区块链技术的检测数据存证系统,所有检测结果实时上链存储,满足ASME PCC-3维护标准要求。在核电领域应用中,实现单个阀门50年生命周期内的368项检测数据可追溯,审计通过率提升至100%。
### 动态校准网络
建立覆盖全国七大区域的计量校准中心,配备0.01级标准压力发生器(Fluke P3000系列)。通过NIM(中国计量院)认证的移动校准车,可为偏远地区提供现场标定服务,确保检测设备年漂移率<0.05%。
## 未来发展趋势建议
建议行业重点推进三方面建设:①建立基于数字孪生的虚拟检测平台,实现85%以上检测项目的数字化预验证;②推动ISO/TC131国际标准的本土化适配,形成具有自主知识产权的检测规范体系;③开发多模态融合检测装备,集成太赫兹成像等新型传感技术,攻克复杂工况下的在线监测难题。预计到2028年,智能化检测技术将覆盖60%以上的气压控制装置应用场景,推动行业进入"预测性维护"新阶段。
上一篇:其它电离辐射检测下一篇:增强竖丝岩棉复合板芯材的短期吸水量检测
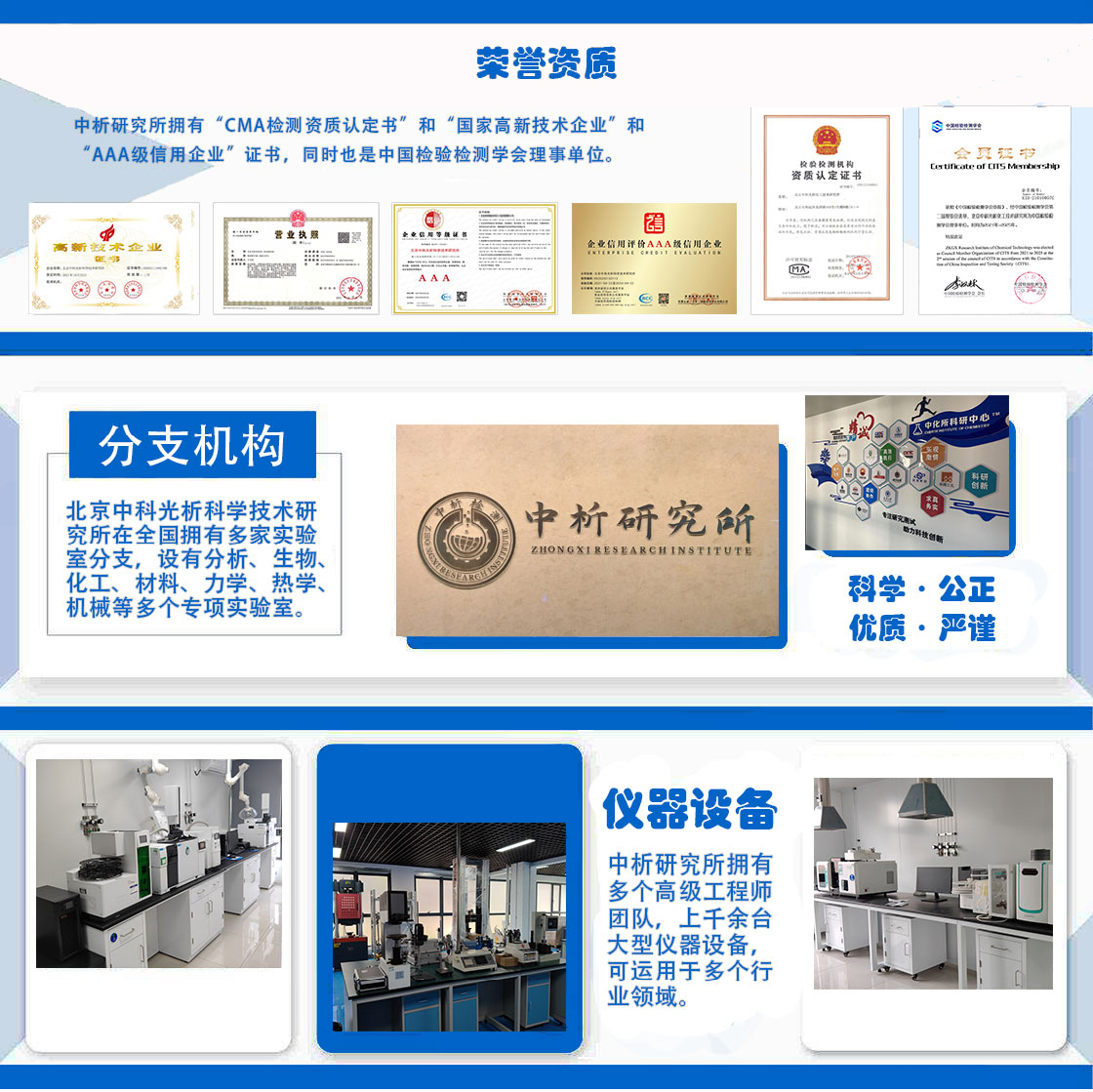
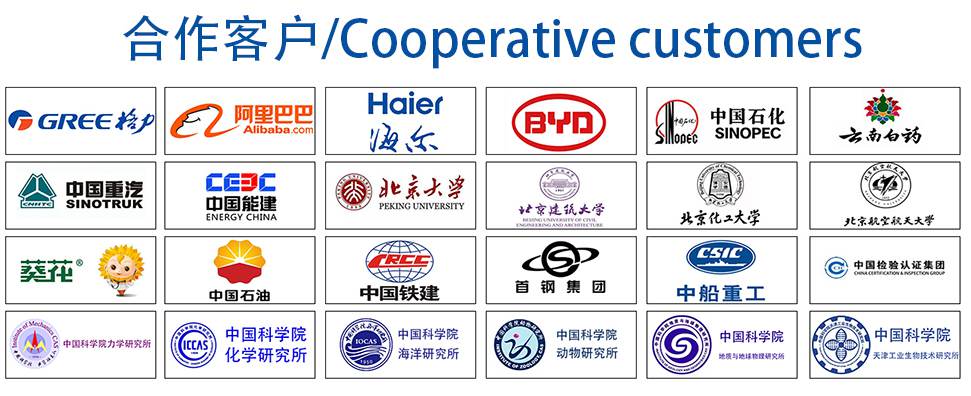
材料实验室
热门检测
26
23
22
23
22
20
20
21
21
21
23
21
18
21
21
21
21
19
23
21
推荐检测
联系电话
400-635-0567