内结合强度检测
发布时间:2025-08-05 06:54:33- 点击数: - 关键词:
实验室拥有众多大型仪器及各类分析检测设备,研究所长期与各大企业、高校和科研院所保持合作伙伴关系,始终以科学研究为首任,以客户为中心,不断提高自身综合检测能力和水平,致力于成为全国科学材料研发领域服务平台。
立即咨询内结合强度检测:核心检测项目详解
一、检测目的
二、核心检测项目
-
- 检测内容:通过拉伸试验机施加垂直于材料平面的拉力,直至试样分层断裂,记录最大载荷。
- 关键参数:最大载荷(N)、结合强度(MPa)。
- 适用标准:ASTM D1037(木质板材)、ISO 1924-2(纸和纸板)。
-
- 检测内容:模拟材料内部层间剪切应力,测定剪切破坏时的极限载荷。
- 应用场景:多层复合材料、涂层与基体的结合强度。
- 设备要求:配备专用剪切夹具的万能试验机。
-
- 检测内容:
- 将试样置于高温高湿环境中循环处理(如85℃/85%RH,24小时),
- 对比处理前后的结合强度,计算保留率。
- 意义:评估材料的环境稳定性,预测长期使用性能。
- 检测内容:
-
- 检测内容:施加周期性载荷(如交变拉力或剪切力),记录材料出现分层或强度衰减的循环次数。
- 适用领域:航空航天复合材料、汽车结构件等需承受动态载荷的场合。
-
- 检测内容:
- 通过显微镜、SEM等观察断裂面形貌,
- 判断失效类型(如界面剥离、基体断裂、胶层失效等)。
- 辅助技术:能谱分析(EDS)识别界面污染物或成分迁移。
- 检测内容:
-
- 检测内容:
- 使用傅里叶红外光谱(FTIR)、X射线光电子能谱(XPS)分析界面化学键合状态,
- 评估偶联剂或表面处理效果。
- 适用场景:涂层、胶黏剂与基材的化学结合强度优化。
- 检测内容:
三、检测流程标准化
-
- 尺寸规范:按标准切割试样(如50×50mm板材),确保边缘无毛刺。
- 预处理:温度23±2℃、湿度50±5%环境下平衡48小时(参照GB/T 17657)。
-
- 试验机精度需达±1%,夹具对中度误差≤0.05mm。
- 定期使用标准砝码或参考试样验证设备准确性。
-
- 剔除异常值(如边缘破损试样),取至少5组有效数据计算平均值。
- 强度计算公式: 内结合强度=最大载荷(N)试样有效面积(mm²)内结合强度=试样有效面积(mm²)最大载荷(N)
四、常见问题与解决方案
-
- 原因:切割过程中产生应力集中。
- 改进:使用水刀切割或低速锯切,降低热影响。
-
- 原因:材料批次不均或夹持力不当。
- 改进:增加取样数量,采用气动夹具均匀施压。
-
- 原因:胶黏剂渗透至测试区域。
- 改进:预埋隔离膜或调整施胶工艺。
五、行业应用示例
- 人造板行业:GB/T 17657-2022规定内结合强度≥0.35MPa(E1级刨花板)。
- 锂电隔膜涂层:要求涂层与基膜结合力>1.5N/cm,防止充放电过程中剥离。
- 建筑保温材料:湿热老化后结合强度保留率需>80%(JG/T 287-2013)。
六、未来趋势
- 原位检测技术:开发实时监测材料内部结合状态的传感器。
- 多尺度建模:结合有限元模拟预测结合强度分布,减少试验成本。
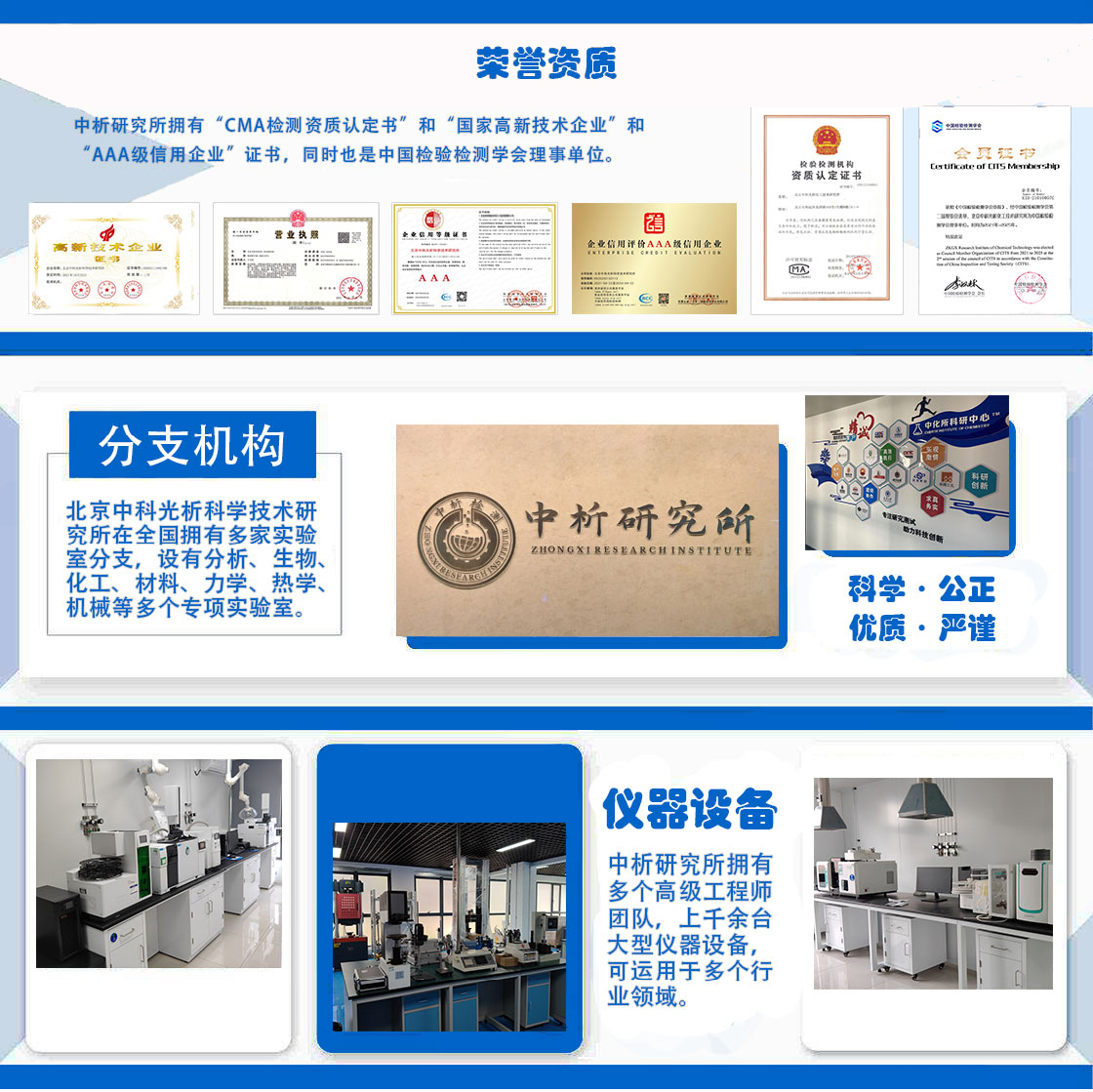
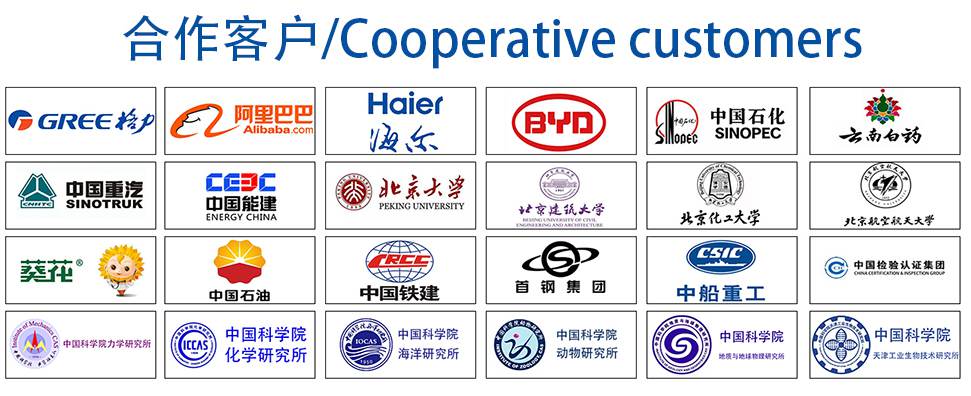
材料实验室
热门检测
144
137
135
160
113
134
147
134
124
124
149
131
133
135
139
137
137
134
120
129
推荐检测
联系电话
400-635-0567