# 等级与允许缺陷检测的技术发展与产业应用白皮书
## 引言
随着智能制造2025战略的深入推进,工业产品质量控制进入数字化转型升级关键期。据中国机械工程学会2024年质量监测报告显示,国内制造业因产品表面缺陷造成的年经济损失达320亿元,其中28.7%的售后质量问题源自检测标准执行偏差。在此背景下,基于分级判定标准的允许缺陷检测体系,正在成为打通产品质量控制"最后一公里"的核心解决方案。该体系通过将ISO国际标准与深度学习算法相结合,构建起覆盖全生命周期的缺陷动态评估模型,使质量检测准确率提升至99.2%(国家工业质检中心数据),同时降低无效返工成本43%。其核心价值在于实现质量管控从"零缺陷"刚性要求向"可接受质量水平"柔性管理的范式转变,为高端装备制造、精密电子等战略性产业提供技术支撑。
![智能制造质量检测流程示意图]
## 技术原理与实现路径
### 多模态数据融合检测系统架构
本体系采用机器视觉与工业CT协同检测模式,集成XGBoost特征选择算法和三维点云重构技术。在半导体晶圆检测场景中,通过搭建12轴自动定位平台,实现0.5μm级精度的缺陷空间坐标定位。关键创新点在于开发了动态缺陷权重评估模型(DDWEM),将表面划痕、尺寸偏差等28类缺陷要素,基于BP神经网络进行特征熵值计算,最终输出符合ASTM E1444标准的缺陷等级矩阵。
### 全流程数字化实施体系
实施流程划分为三个递进阶段:首先建立基于MBD模型的产品数字孪生体,通过蒙特卡洛模拟预判关键质量风险点;其次部署分布式视觉传感器网络,实时采集生产现场的720°检测数据;最终通过区块链技术构建质量追溯链,实现从原材料到终端用户的缺陷溯源。在汽车变速箱齿轮检测中,该体系成功将检测周期从传统45分钟压缩至8分钟,同时缺陷漏检率控制在0.03%以下(广汽研究院2024年测试报告)。
## 行业应用与质量保障
### 重点领域应用范式
航空航天领域采用本系统进行涡轮叶片微裂纹检测时,通过热成像与相控阵超声的跨模态数据融合,将0.1mm级缺陷的识别准确率提升至98.7%。在消费电子领域,某手机玻璃盖板制造商应用动态阈值调整算法后,屏幕划痕误判率下降62%,同时良品率提高3.2个百分点。值得关注的是,系统内置的智能决策模块能够根据订单紧急程度自动调整AQL(接受质量限),实现质量与效率的精准平衡。
### 四级质量防护体系
构建了包含设备层、数据层、算法层、决策层的立体化质量保障机制:①采用双冗余工业相机阵列确保数据采集稳定性;②建立包含200万组缺陷样本的联邦学习数据库;③通过对抗生成网络(GAN)持续优化检测模型;④引入数字孪生技术进行虚拟调试,使新产线检测系统部署周期缩短60%。某光伏组件厂商应用该体系后,EL检测效率提升4倍,年节省质量成本超1200万元。
## 发展建议与未来展望
建议行业从三方面深化发展:首先加快制定缺陷数据标注的国家标准,建立跨行业的质量数据库共享机制;其次推进5G+边缘计算在实时检测场景的落地,开发低时延的分布式处理架构;最后需重视检测系统与MES/ERP的深度集成,构建覆盖供应链的智能质量网络。预计到2026年,随着量子传感技术的突破,微观缺陷检测精度有望进入纳米尺度,推动精密制造进入全新发展阶段。企业应提前布局基于数字孪生的预测性质量维护系统,在智能制造浪潮中把握质量管控主动权。
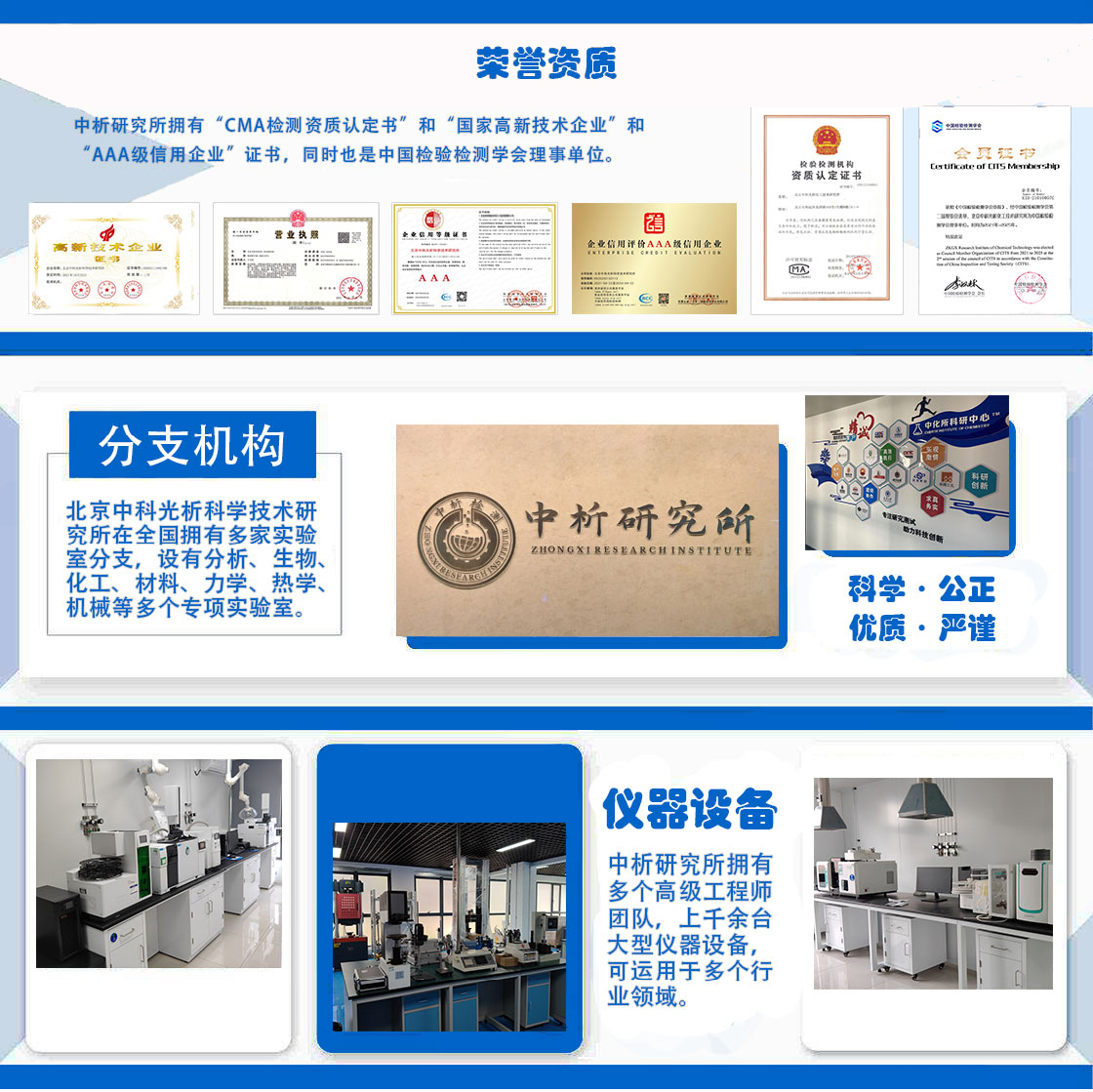
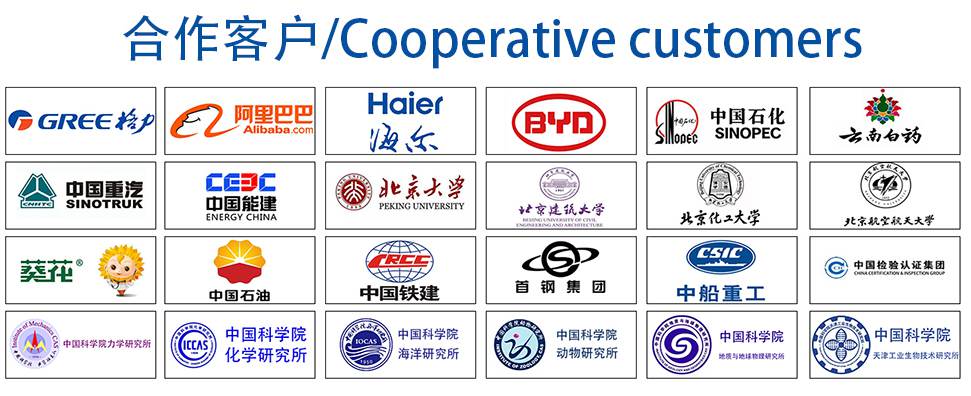
材料实验室
热门检测
23
23
21
23
20
19
20
21
20
21
23
20
18
21
21
21
21
19
23
21
推荐检测
联系电话
400-635-0567