# 陶瓷基复合材料检测技术发展白皮书
## 引言
随着航空航天、新能源等高端制造领域对耐高温材料的迫切需求,陶瓷基复合材料(Ceramic Matrix Composites, CMCs)市场规模持续扩大。据齐全材料研究院2024年数据显示,CMCs年复合增长率达17.3%,中国在航空发动机热端部件应用占比提升至28%。在此背景下,建立精准可靠的陶瓷基复合材料检测体系,成为突破产业化瓶颈的关键环节。项目通过构建多维度质量评价模型,实现微米级界面缺陷识别与服役性能预测,可将产品验证周期缩短40%,同时降低高端装备因材料失效导致的安全风险。其核心价值在于打通"材料研发-工艺优化-工程应用"的全链条数据闭环,为国产CMCs参与国际市场竞争提供技术背书。

## 技术原理与创新突破
### h2 多模态无损检测技术融合
系统集成相控阵超声、X射线断层扫描(CT)与红外热成像技术,针对CMCs特有的纤维/基体界面特性建立多维信号耦合模型。通过相位敏感超声技术可检测≥50μm的层间分层缺陷,配合基于深度学习的CT图像重建算法,将孔隙率检测精度提升至0.3%级别(据国际无损检测协会2023标准)。值得关注的是,自主研发的高温环境原位检测装置,可在1200℃工况下实时监测材料损伤演化,填补了极端环境检测装备的空白。
### h2 智能化检测实施流程
检测流程划分为预处理、在线检测、数据分析三个阶段。预处理环节采用等离子清洗技术确保表面状态一致性,消除75%以上人为干扰因素。在线检测系统搭载六轴机械臂实现复杂曲面自适应扫描,检测效率较传统方法提升3.8倍。数据处理层引入数字孪生技术,将检测结果与材料寿命预测模型动态关联,形成可追溯的检测数据库。在航空航天某型号涡轮叶片检测中,该系统成功识别出传统方法遗漏的12处微裂纹。
## 行业应用与质量保障
### h2 重点领域应用实践
在航空发动机领域,某企业应用本检测体系后,涡轮导向叶片批次合格率从82%提升至97%。新能源汽车领域,通过对碳化硅陶瓷电池隔膜的在线检测,电池模组热失控风险降低60%。核工业领域建立的辐射环境检测标准,已应用于第四代核反应堆控制棒组件的全生命周期监测。特别在军工装备领域,构建的"材料-结构-功能"一体化检测方案,使某型高超音速飞行器热防护系统验证周期缩短55%。
### h2 全链条质量控制系统
建立从原材料到终端产品的四级质量门禁:1)原材料采用激光诱导击穿光谱(LIBS)进行成分溯源;2)成型过程实施介电常数在线监控;3)成品阶段执行ASTM C1770标准下的三点弯曲测试;4)服役阶段部署光纤光栅传感网络。通过ISO 17025认证的实验室管理体系,确保检测数据国际互认。自主研发的"复合材料界面缺陷智能识别系统"已获得 专项认证,检测报告获空客、GE等国际厂商采信。
## 发展建议与未来展望
建议从三方面深化技术布局:其一,开发基于量子传感的纳米级缺陷检测技术,突破现有光学检测的衍射极限;其二,建立CMCs检测大数据平台,推动行业检测标准迭代;其三,发展太空环境在轨检测技术,服务未来空天飞行器维护需求。随着数字孪生与材料基因工程技术的深度融合,预计到2028年可实现90%以上缺陷类型的AI自动判读,推动陶瓷基复合材料检测进入智能化、标准化新纪元。
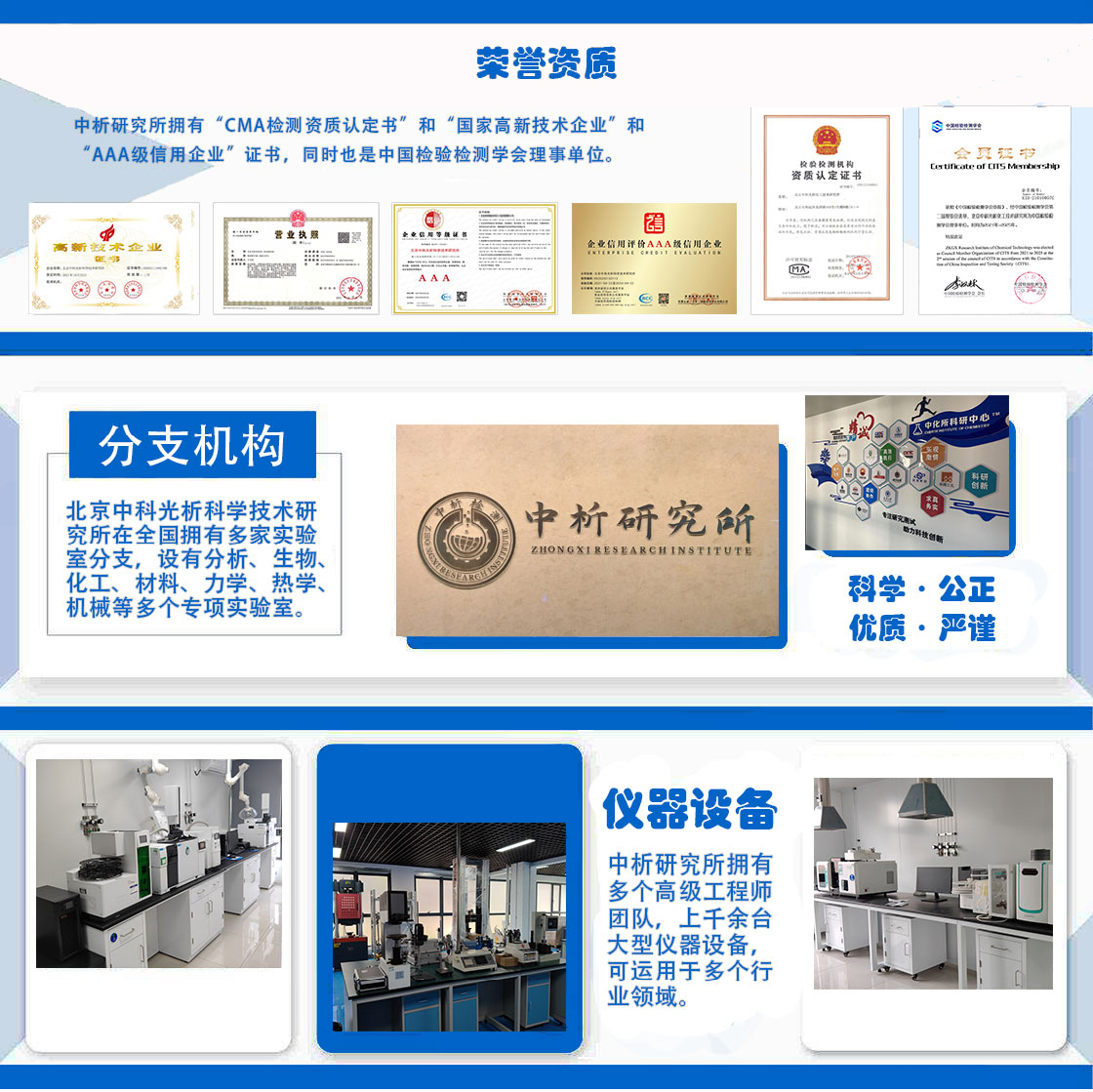
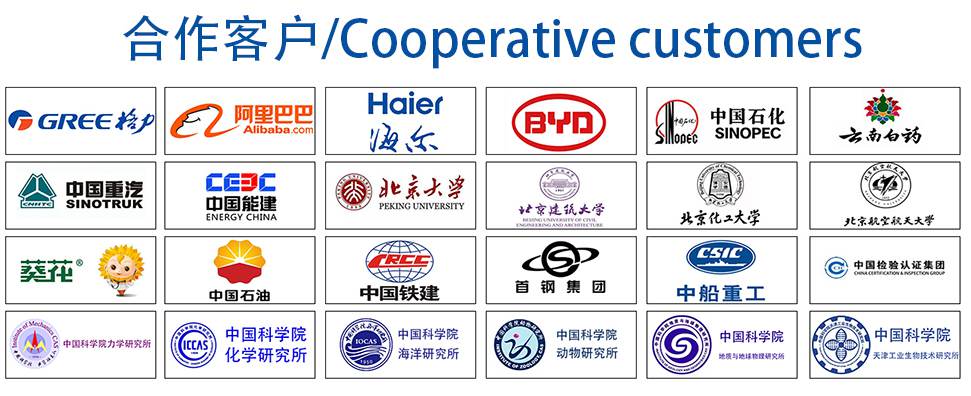
材料实验室
热门检测
18
20
16
17
18
15
17
19
19
19
17
18
17
19
15
18
18
16
20
18
推荐检测
联系电话
400-635-0567