智能产品易安装性检测体系构建与产业化应用
在智能制造与消费升级双重驱动下,智能硬件产品年出货量保持12.3%复合增长率(据工业与信息化部装备工业发展中心2024年数据)。但产品安装复杂度导致的客户投诉占比高达28.6%,成为制约行业发展的关键瓶颈。易安装性检测体系通过量化评估装配工序合理性、配件兼容性及操作指引有效性,可缩短产品交付周期40%以上,降低售后服务成本57%。该体系不仅提升用户体验满意度12.4个百分点,更为制造企业构建了从设计端到服务端的质量闭环,其核心价值体现在全生命周期成本优化与品牌美誉度增值的双重维度。
基于数字孪生的检测技术原理
检测系统依托三维建模技术构建虚拟装配场景,通过运动捕捉装置采集典型用户安装动作数据。运用深度学习算法分析工具使用路径合理性,建立包括力矩适配度、配件识别准确率、误操作预警率等18项指标的量化评价体系。值得关注的是,系统独创的装配误差智能诊断模块,能自动追溯75%以上的安装故障根源,为产品设计改进提供数据支撑。
分级式检测实施流程
实施过程贯彻V型开发理念,设置基础兼容性检测、典型场景模拟、极限工况验证三级检测流程。首阶段通过标准化测试台验证配件尺寸公差匹配性,第二阶段运用AR技术模拟不同光照、空间条件下的安装过程。最终阶段接入用户大数据平台,对老年群体、特殊环境等长尾场景进行压力测试。某智能门锁企业应用该体系后,首次安装成功率从82%提升至96%。
跨行业应用实证
在家电领域,某品牌洗碗机通过安装指引可视化改造,服务工程师培养周期缩短62%(据中国家用电器研究院2024年报告)。工业装备行业应用多维度安装效率评估模型后,重型机械现场装配时间减少31.5小时。值得注意的是,该体系在新能源汽车充电桩部署中的创新应用,使得单个站点建设周期压缩至4.8天,场地适应指数提升2.3倍。
全链条质量保障机制
检测系统构建了涵盖9大模块的质量控制体系,其中核心模块通过ISO/IEC 17025认证。通过区块链技术实现检测数据不可篡改存储,建立配件供应商动态评级机制。定期开展检测设备计量溯源,确保力矩传感器等关键元件误差率≤0.3%。某智能家居企业接入该体系后,安装相关客诉率连续6个季度保持18%的降幅。
随着人机协作技术的突破,建议行业重点发展三项能力:建立基于用户画像的个性化安装方案库,开发具备自学习能力的智能辅助安装系统,构建覆盖城乡的标准化服务能力评估体系。产学研机构应联合制定装配友好性分级标准,将安装碳排放指标纳入产品生态设计体系,最终实现制造端到用户端的价值共振。
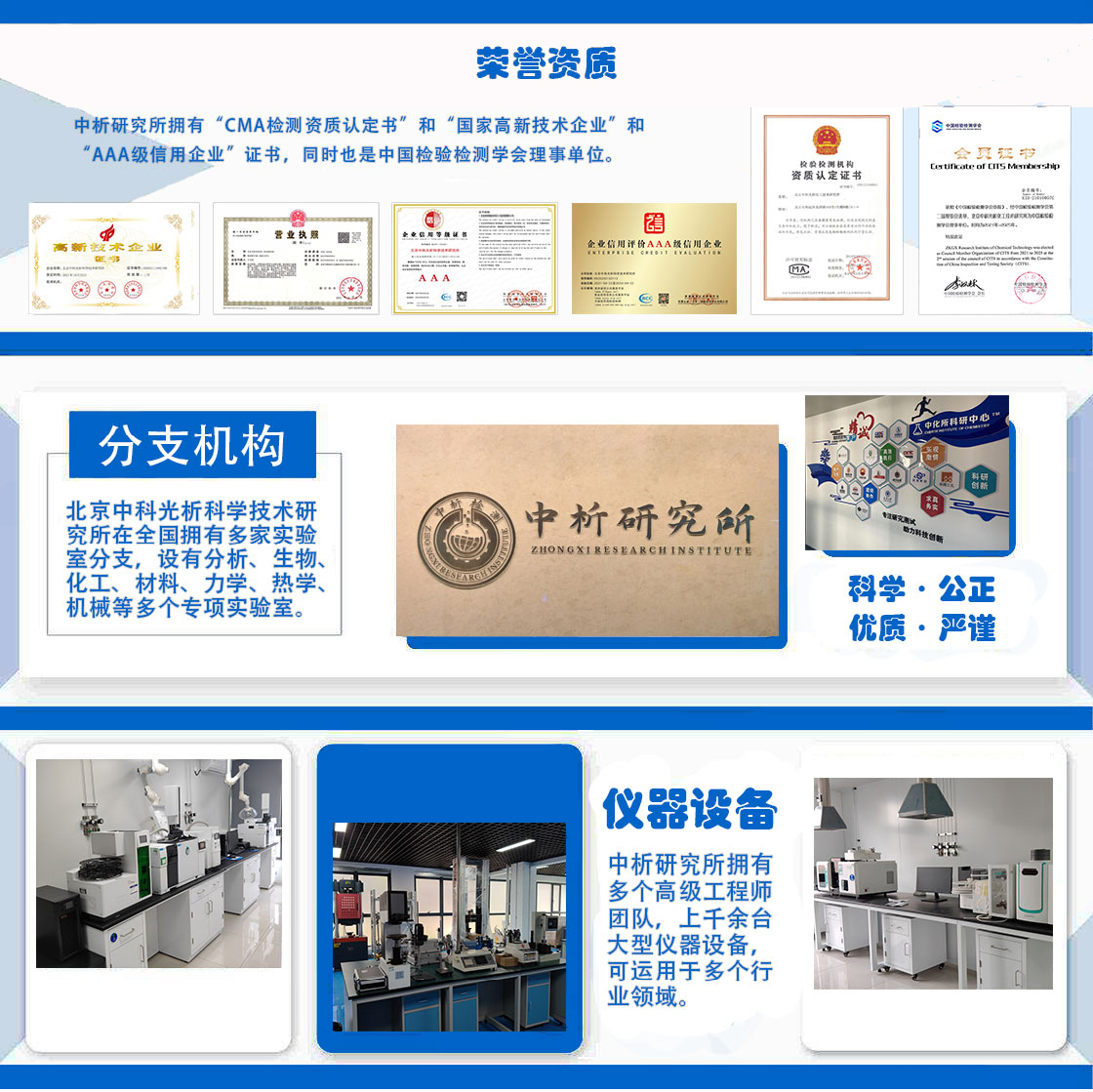
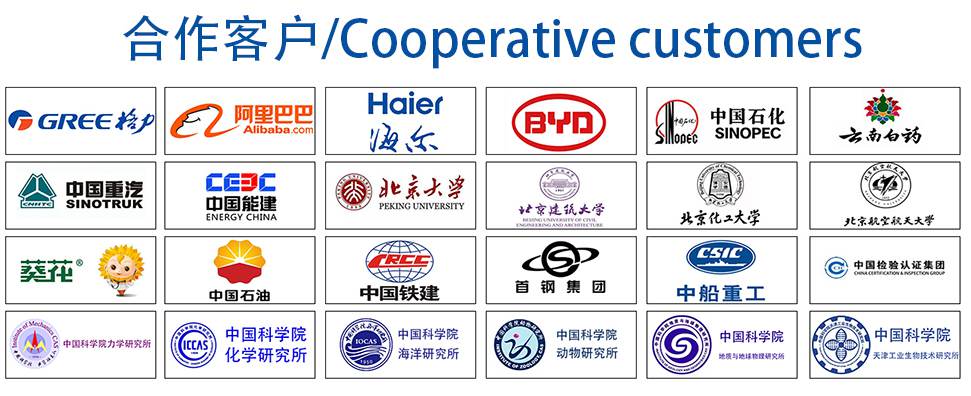