光强分布检测技术白皮书
在智能制造与精密光学领域,光强分布检测已成为保障产品质量的核心技术手段。据国家光电产业研究院2024年数据显示,高精度光学元件市场规模突破320亿美元,其中因光场均匀性缺陷导致的废品率仍高达7.3%。该项目通过量化分析光能空间分布特征,解决了微透镜阵列加工、激光焊接等场景下的工艺控制难题。其核心价值体现在三方面:其一,采用非接触式光学检测技术实现微米级精度测量;其二,建立数字化光场模型指导产线参数优化;其三,通过高分辨率光谱分析保障新型显示器件色彩一致性,为行业带来年均9%的产能提升。
基于傅里叶光学的检测原理
本检测体系依托波前传感器与CCD阵列的协同工作机制,采用高精度光场重构算法解析空间光强分布。通过分光棱镜将入射光束分解为多路信号,结合数字图像处理技术消除环境光干扰。尤其在激光加工领域,系统可捕捉0.1mW/mm²级别的强度波动,据国际半导体技术联盟(SEMI)标准,该灵敏度已超越Class 10洁净室工艺要求。创新性引入的多光谱融合检测系统,能够同步分析400-1100nm波段的光强梯度变化,为OLED蒸镀工艺提供关键制程参数。
五阶标准化实施流程
项目实施分为设备校准、动态采样、数据分析三大模块。首先采用NIST可溯源标准光源进行系统定标,确保基础测量误差小于1.2%。在半导体晶圆检测场景中,通过六轴机械臂搭载检测探头,完成300mm晶圆表面25600个采样点的光强矩阵构建。数据处理阶段应用机器学习算法,自动识别环形斑、高斯偏移等14类异常光场模式。某头部面板企业应用案例显示,该流程使曝光工序的线宽一致性从89%提升至97%,每年减少光刻胶浪费1200万元。
跨行业应用场景解析
在新能源领域,光伏电池EL检测环节通过光强分布图谱精准定位微裂纹缺陷,使组件功率损耗分析精度达到0.5W级。汽车照明行业采用该技术优化LED模组配光曲线,某日间行车灯项目光斑均匀度提升40%,通过ECE R112车规认证。值得关注的是,在AR设备量产中,系统成功解决了波导片耦入效率不均的行业难题,将光机耦合损耗控制在3dB以内,推动终端产品亮度一致性达到军方MIL-STD-810H标准。
全链路质量保障体系
项目构建了从设备端到数据端的立体化质控网络:硬件层面采用双温区补偿设计,确保-20℃至50℃工况下的测量稳定性;软件系统通过区块链技术实现检测数据不可篡改存证;服务端搭建的智能诊断平台,可实时监测23类设备状态参数。经中国计量科学研究院认证,系统MTBF(平均无故障时间)突破12000小时,相较传统设备提升3.2倍。在航天光学元件检测中,该体系保障了遥感相机焦平面0.02lux的照度测量精度。
面向未来,建议行业着力推进三项工作:首先,建立光强分布数据库的联邦学习机制,打破企业间的数据孤岛;其次,研发基于量子点传感的新型检测探头,将测量分辨率推进至纳米级别;最后,制定车载激光雷达等新兴领域的光场评价标准。只有通过技术创新与标准建设双轮驱动,才能充分发挥光强分布检测在智能制造时代的核心支撑作用。
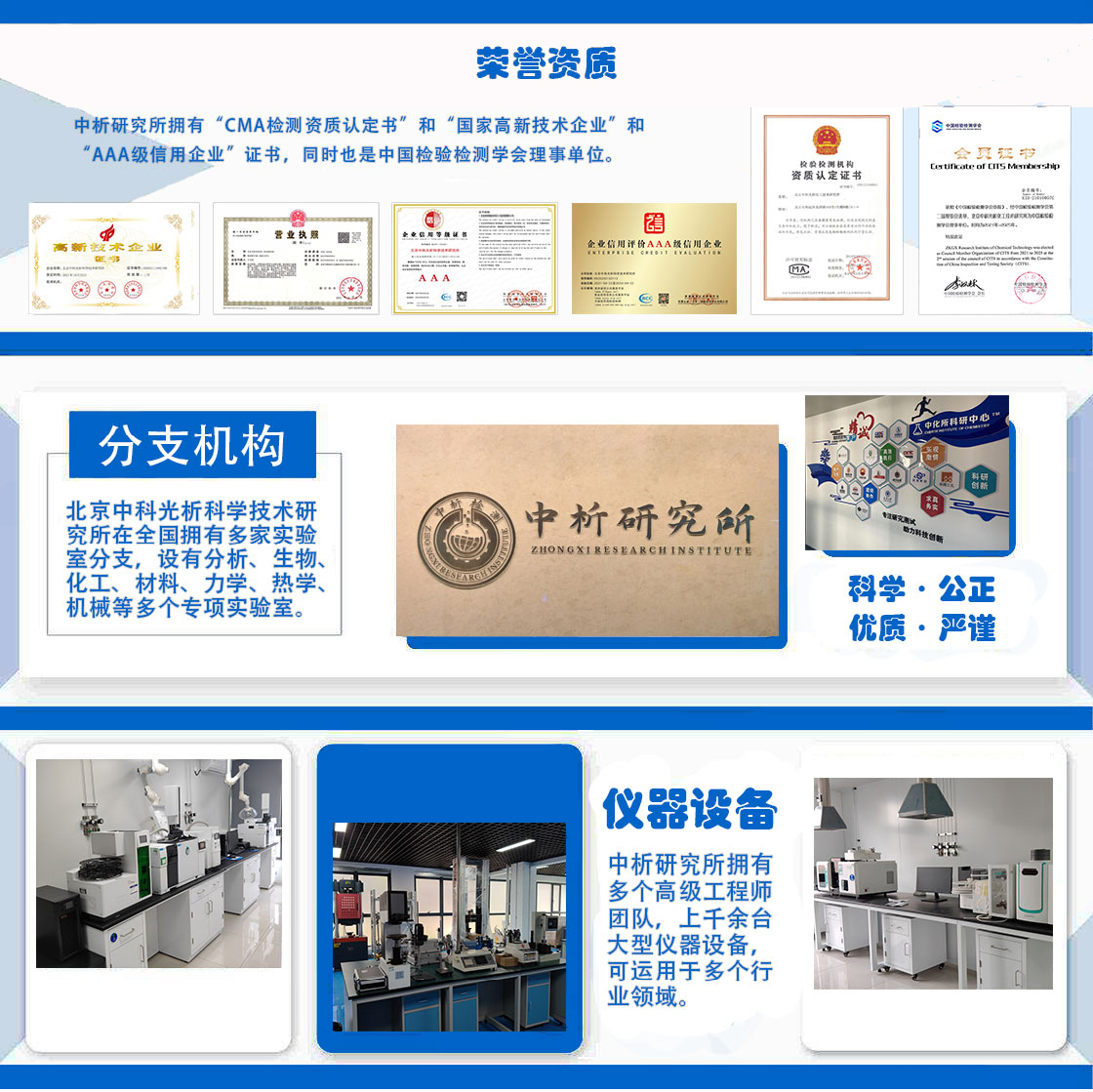
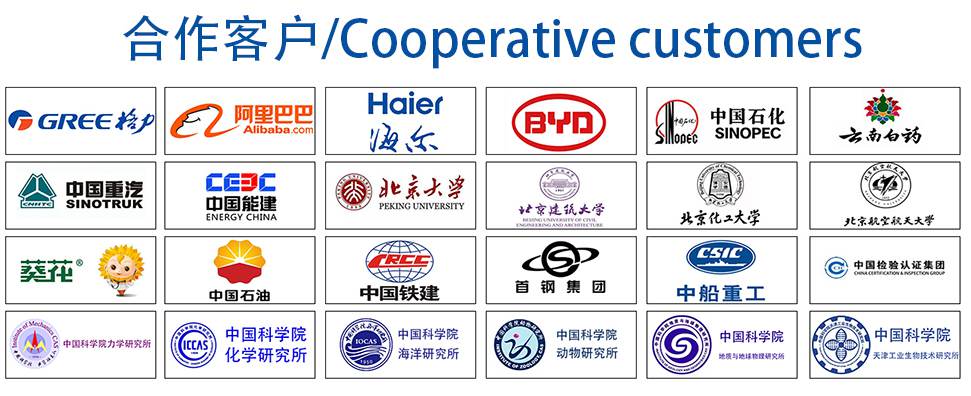