外部目验检测:核心检测项目与应用指南
一、外部目验检测的定义
二、适用领域
- 建筑工程:建筑外墙、屋顶、桥梁、管道等。
- 工业设备:压力容器、管道、阀门、机械结构件等。
- 交通运输:车辆底盘、飞机蒙皮、船舶甲板等。
- 电力设施:输电线路、绝缘子、变压器外观等。
- 制造业:产品表面质量、焊接接缝等。
三、核心检测项目分类
1. 表面缺陷检测
- 开裂/裂缝:检查材料表面或接缝处的裂纹(如混凝土结构、焊接部位)。
- 腐蚀/锈蚀:金属部件的氧化、锈斑或涂层脱落。
- 变形/凹陷:结构件因外力导致的弯曲、扭曲或凹痕。
- 磨损/划痕:机械部件因摩擦产生的表面损伤(如齿轮、轴承)。
2. 连接件与密封性检测
- 螺栓/铆钉状态:检查松动、缺失或断裂。
- 焊缝质量:观察焊缝的连续性、气孔、夹渣等缺陷。
- 密封性检查:管道法兰、阀门处是否存在泄漏痕迹(如油渍、水渍)。
3. 涂层与防护层检测
- 油漆剥落:评估防腐涂层的完整性。
- 覆层破损:如管道保温层开裂、防水卷材起鼓。
- 镀层磨损:电镀或热浸锌层的局部缺失。
4. 环境适应性检测
- 生物侵蚀:木材或混凝土上的霉菌、虫蛀痕迹。
- 气候老化:紫外线导致的塑料脆化、橡胶龟裂。
- 污染物附着:化学物质残留或积尘情况。
5. 功能性部件检查
- 机械设备:皮带松弛度、链条润滑状况。
- 电气设备:电缆表皮破损、接头氧化。
- 车辆部件:轮胎胎纹深度、车灯是否完好。
四、辅助工具与技术要求
- 基础工具:手电筒(侧光观察表面纹理)、放大镜(细查微裂纹)、卷尺/卡尺(测量缺陷尺寸)。
- 进阶设备:工业内窥镜(狭窄空间检测)、无人机(高空或大面积区域扫描)。
- 标准依据:需参照行业规范(如ASTM E94、ISO 9712)制定检测标准。
五、检测流程
- 前期准备:明确检测目标,收集图纸或历史数据。
- 环境确认:确保光照充足,必要时清理检测面。
- 系统检查:按顺序覆盖所有关键部位(如从顶部到底部)。
- 记录与评级:拍照、绘图或填写检测报告,按缺陷严重性分级。
- 后续处理:提出维修建议或进一步无损检测(如超声波、渗透检测)。
六、局限性及注意事项
- 局限性:仅能识别表面缺陷,无法检测内部损伤。
- 人员要求:检测员需具备经验,熟悉常见缺陷形态。
- 安全防护:高空或危险环境需配备安全装备(如安全带、防毒面具)。
七、总结
上一篇:射频电磁场辐射抗扰度检测下一篇:恒定加速度检测
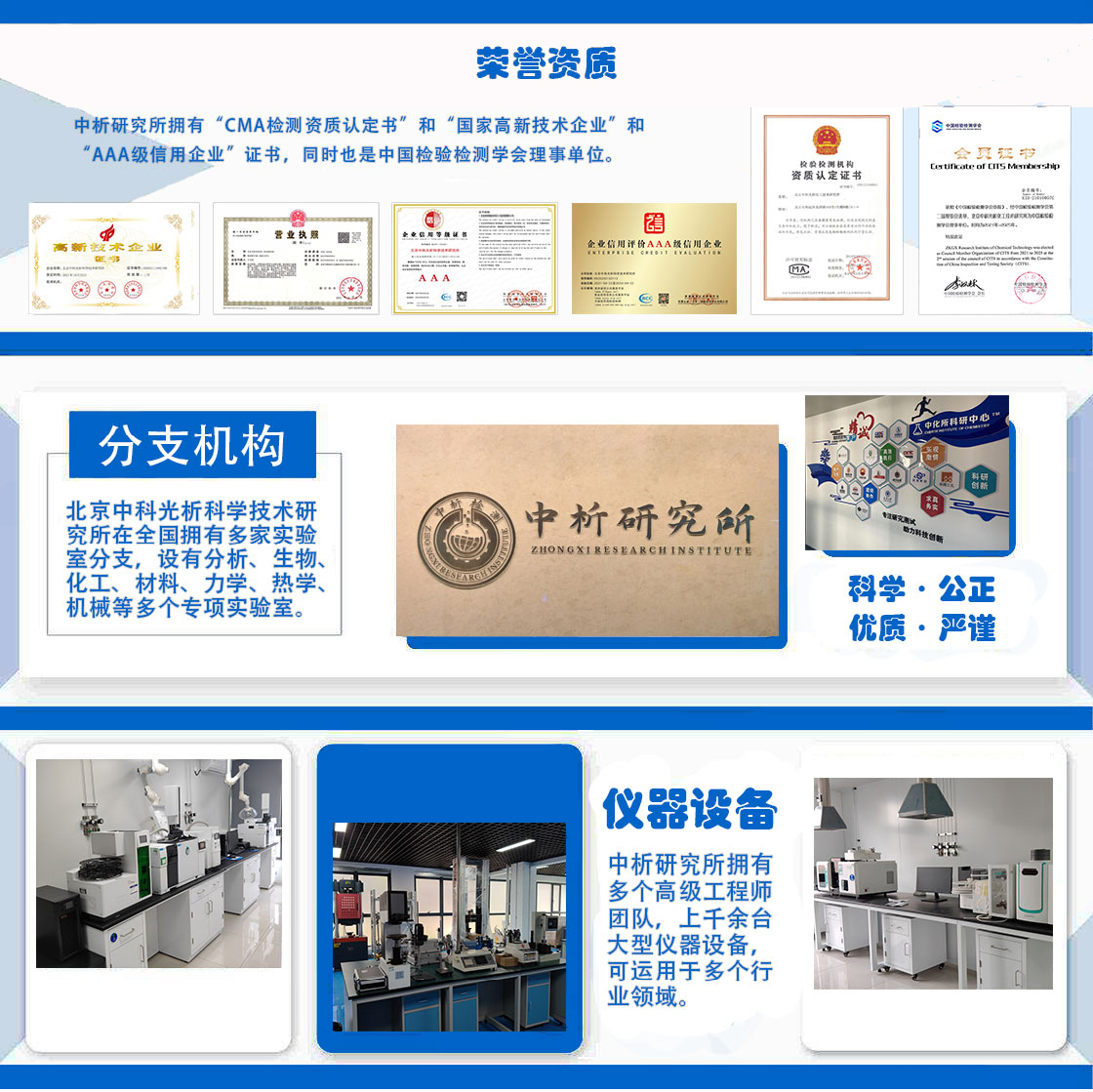
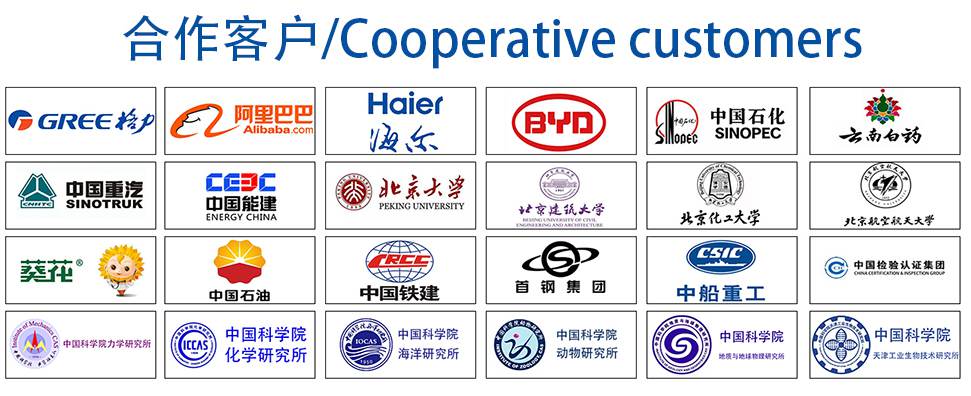
材料实验室
热门检测
251
211
186
201
193
198
205
198
204
210
200
195
192
198
193
189
203
195
204
198
推荐检测
联系电话
400-635-0567