循环负载试验(热循环负载试验)检测项目详解
一、核心检测项目分类
1. 机械循环负载试验检测项目
- 项目内容:检查试件在反复机械应力(如拉伸、压缩、弯曲、振动)下的裂纹扩展、断裂或松动现象。
- 检测方法:高频次载荷循环(如数万次至百万次)后,通过目视检查、X射线探伤或超声波检测评估内部结构损伤。
- 判定标准:无可见裂纹、焊接点无脱落、紧固件无松动。
- 项目内容:测定材料或组件在交变载荷下的疲劳极限(S-N曲线)。
- 方法:通过应力-循环次数曲线判断试件失效阈值,常用于金属部件(如弹簧、轴承)和复合材料。
- 项目内容:测量试件在循环加载下的位移、应变或变形量。
- 工具:应变片、激光位移传感器、数字图像相关(DIC)技术。
- 意义:评估材料弹性变形范围及塑性变形累积程度。
2. 热循环负载试验检测项目
- 项目内容:验证试件在高温→低温→高温交替环境中的功能稳定性。
- 典型条件:-40℃至+150℃范围内快速温变(如15℃/min),循环次数通常为500~1000次。
- 检测指标:
- 热膨胀系数匹配性:多层材料界面是否因膨胀差异导致分层或开裂。
- 温度骤变耐受性:密封件、涂层在热冲击下是否失效。
- 适用对象:电子元器件(芯片、PCB)、电池、传感器等。
- 关键参数:
- 电阻/电容漂移:温变过程中导电通路是否因材料形变而劣化。
- 信号传输完整性:高频电路在热应力下的阻抗匹配变化。
- 项目内容:评估高分子材料(塑料、橡胶)在热循环下的脆化、硬化或软化现象。
- 方法:通过DSC(差示扫描量热法)检测玻璃化转变温度(Tg)变化,或通过拉伸试验对比老化前后力学性能。
3. 综合循环负载(机械+热)检测项目
- 热-机械耦合变形:高温下机械负载导致的蠕变行为分析。
- 界面可靠性:焊接、粘接部位在热胀冷缩与振动联合作用下的失效模式。
二、试验设备与执行流程
-
- 机械负载设备:液压伺服疲劳试验机、电磁振动台。
- 热循环设备:高低温交变试验箱(温变速率≥10℃/min)。
- 集成设备:三综合试验箱(温湿度+振动)。
-
- 预处理:试件在标准温湿度下稳定24小时。
- 负载施加:按预设程序交替施加机械/热负荷(如:高温保持1h→机械振动2h→低温保持1h)。
- 中间检测:每100次循环暂停,进行功能测试与缺陷记录。
- 最终评估:解剖试件,分析微观结构(SEM/金相)与化学成分(EDX)。
三、行业标准与判定依据
领域 | 常用标准 | 核心指标示例 |
---|---|---|
电子器件 | JEDEC JESD22-A104(热循环) | 焊点空洞率≤5%,电阻变化率≤10% |
汽车部件 | ISO 16750-3(机械振动) | 无功能退化,紧固扭矩衰减≤20% |
航空航天 | RTCA DO-160G(综合环境试验) | 结构无永久变形,疲劳寿命≥设计值 |
四、典型案例分析
-
- 检测项目:模拟车辆行驶振动+充放电产热导致的温度循环(-30℃~60℃)。
- 失效模式:电芯连接片断裂、绝缘膜龟裂。
- 改进措施:优化焊接工艺,选用耐低温硅胶密封材料。
-
- 条件:85℃/-40℃各保持30分钟,循环200次。
- 关键指标:电池片隐裂增长≤2mm,功率衰减≤5%。
五、数据解析与报告输出
- 趋势图:形变量、电阻值等参数随循环次数的变化曲线。
- 失效分析:明确失效机理(如热疲劳、应力腐蚀)。
- 改进建议:材料替换、结构优化或工艺参数调整方案。
结语
上一篇:高温贮存检测下一篇:螺钉、载流部件和连接件检测
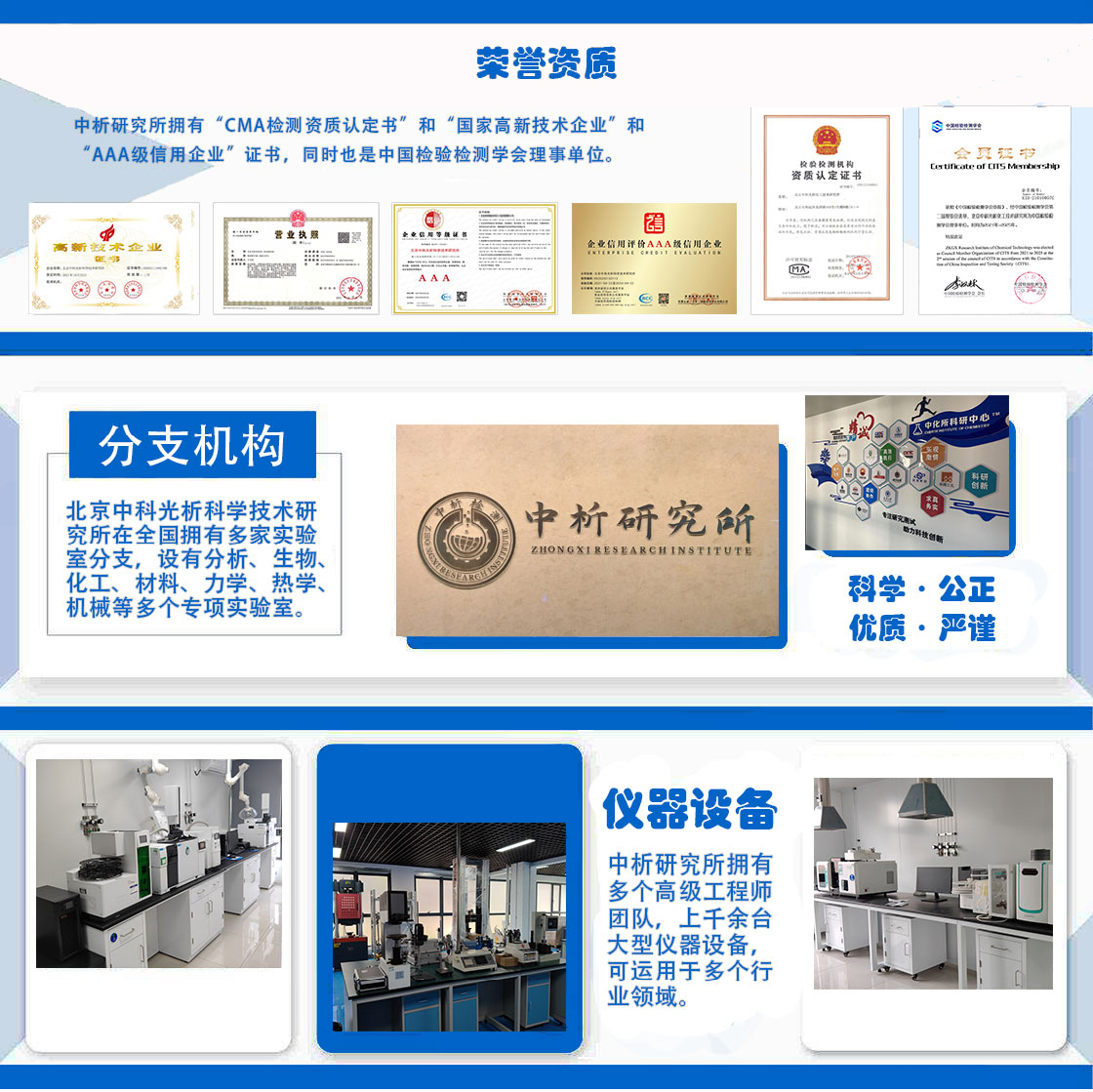
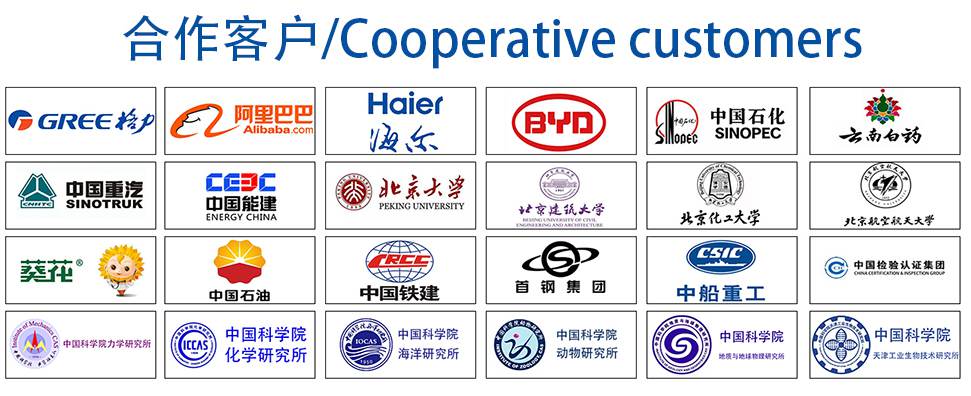
材料实验室
热门检测
253
211
188
202
195
202
207
200
206
214
202
197
195
200
194
192
205
197
206
200
推荐检测
联系电话
400-635-0567