高温贮存检测项目详解
一、核心检测项目清单
-
- 测试内容:
- 外壳是否变形、开裂或起泡;
- 涂层/镀层是否脱落、变色;
- 标识清晰度是否下降;
- 密封件(如橡胶、塑料)是否硬化、龟裂。
- 判定标准:
- 无明显物理损伤,尺寸变化需符合产品公差(如GB/T 38244-2019)。
- 测试内容:
-
- 关键指标:
- 绝缘电阻(如IEC 60664-1要求≥100MΩ);
- 耐压强度(如5kV/1min无击穿);
- 通电后功能稳定性(如信号传输速率、电流波动)。
- 失效模式:
- 元器件焊点断裂、PCB分层、电解电容干涸等。
- 关键指标:
-
- 测试项目:
- 塑料/橡胶的硬度变化(邵氏硬度计测试);
- 金属氧化程度(SEM/EDS分析表面成分);
- 高分子材料热分解温度(TGA热重分析)。
- 典型案例:
- 锂电池隔膜高温下收缩率需≤5%(GB 31241-2022)。
- 测试项目:
-
- 试验方法:
- 充压法检测壳体气密性(如IP67等级产品需承受1m水深压力);
- 粉尘/水雾渗透测试(高温后IP等级是否达标)。
- 试验方法:
-
- 测试内容:
- 紧固件扭矩保持力(如螺栓预紧力衰减率≤15%);
- 弹簧弹性模量变化;
- 轴承润滑脂蒸发率(高温下黏度损失≤30%)。
- 测试内容:
-
- 阿伦尼乌斯模型应用:
- 通过高温加速材料化学反应速率,推算产品贮存寿命(如40℃/1000h等效常温10年)。
- 阿伦尼乌斯模型应用:
二、测试条件设置规范
-
- 常规工业产品:55℃~85℃;
- 极端环境产品(如航天器件):100℃~150℃;
- 试验时间:24~1000小时(根据MIL-STD-810G标准分级)。
-
- 恒温箱波动度≤±2℃,均匀度≤±3℃(参照GB/T 2423.2-2008)。
-
- 测试后需在25℃/60%RH环境中恢复2~4小时,再进行最终检测。
三、行业差异化测试重点
行业 | 重点关注项目 | 典型标准 |
---|---|---|
消费电子 | PCB翘曲度、锂电池安全性 | IEC 62133-2 |
汽车电子 | 连接器接触电阻、ECU功能稳定性 | ISO 16750-4 |
军工装备 | 火工品安定性、复合材料强度保持率 | GJB 150.3A-2009 |
医疗器械 | 硅胶管路弹性、传感器精度漂移 | YY/T 0681.1-2018 |
四、失效分析与改进
-
- 案例1:某车载摄像头镜头组在85℃/500h测试后出现图像模糊,原因为镜片胶水高温蠕变。
- 改进方案:替换为耐高温环氧胶(TG点>150℃)。
-
- 使用正交试验法筛选关键敏感参数(如壳体厚度、散热孔布局),降低高温失效风险。
五、检测报告核心要素
- 温湿度曲线记录图;
- 关键性能前后对比数据表;
- 失效件微观分析照片;
- 符合性(根据ISO 17025认可格式)。
上一篇:外观检验检测下一篇:循环负载试验(热循环负载试验)检测
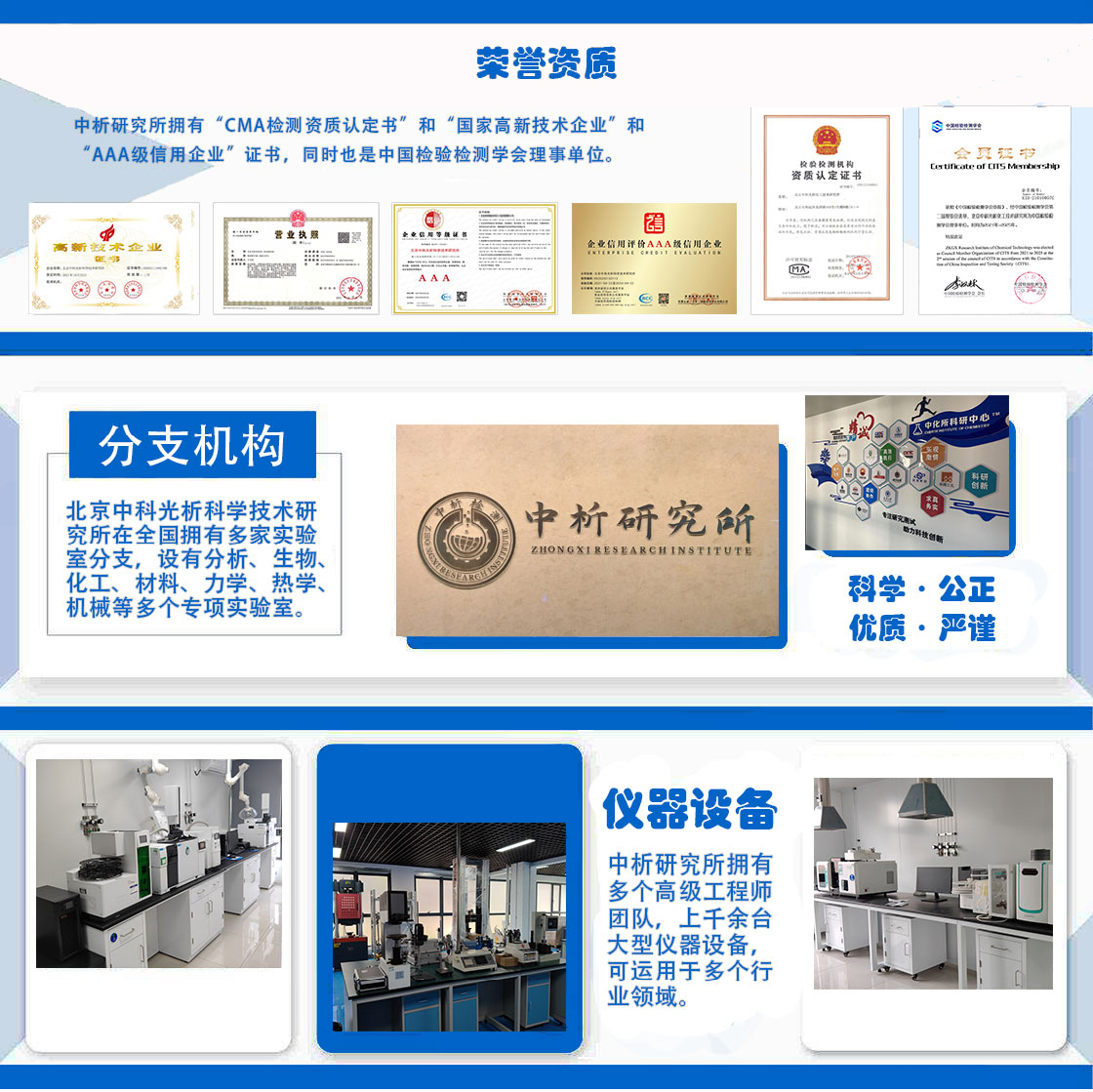
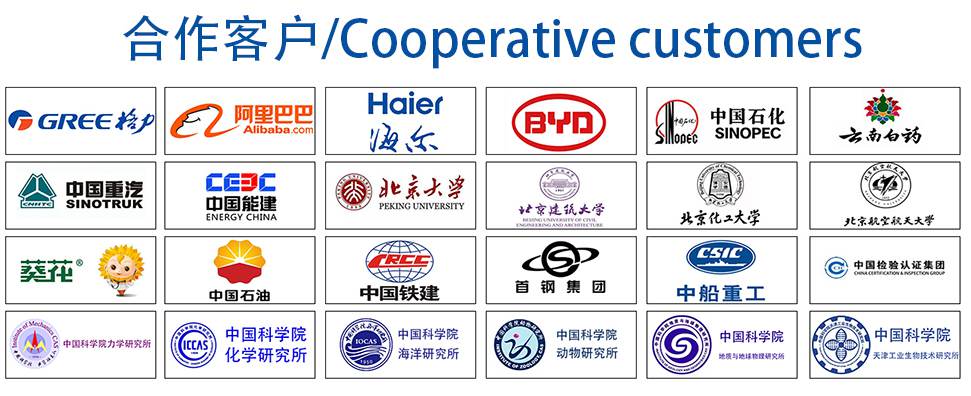
材料实验室
热门检测
252
211
188
202
194
201
206
199
205
213
200
196
194
199
193
191
204
196
205
199
推荐检测
联系电话
400-635-0567