机械耐久性检测:检测项目与核心内容
1. 疲劳寿命测试
- 目的:测定材料或结构在交变载荷下的循环寿命,预测其在长期使用中的断裂风险。
- 检测内容:
- 高周疲劳测试(10^4~10^7次循环):适用于低应力、高频率场景(如发动机曲轴)。
- 低周疲劳测试(<10^4次循环):模拟高应力、低频载荷(如压力容器)。
- 裂纹扩展速率测试:通过预制裂纹试样,分析裂纹生长规律。
- 测试方法:轴向加载、旋转弯曲、三点/四点弯曲试验。
- 设备:伺服液压疲劳试验机、电磁谐振式试验机。
- 标准参考:ASTM E466、ISO 12107。
2. 振动与冲击测试
- 目的:评估机械在振动或冲击环境下的结构稳定性与功能可靠性。
- 检测内容:
- 正弦振动:模拟周期性振动(如电机运行)。
- 随机振动:复现真实环境中的无规律振动(如车辆颠簸)。
- 冲击测试:评估瞬时高加速度冲击下的抗变形能力(如运输跌落)。
- 测试方法:振动台试验、冲击锤试验、跌落试验。
- 设备:电动振动台、液压振动台、冲击试验机。
- 标准参考:IEC 60068-2-6(振动)、MIL-STD-810G(冲击)。
3. 耐磨性测试
- 目的:分析材料或表面涂层在摩擦条件下的磨损速率与失效机制。
- 检测内容:
- 磨粒磨损(如砂纸摩擦):评估硬质颗粒造成的磨损(适用于矿山机械)。
- 粘着磨损(金属间接触):模拟齿轮啮合或轴承滑动。
- 疲劳磨损:循环载荷下的表面剥落(如滚动轴承)。
- 测试方法:销-盘磨损试验、往复式摩擦试验、Taber磨耗试验。
- 设备:摩擦磨损试验机、硬度计、表面轮廓仪。
- 标准参考:ASTM G99、ISO 20808。
4. 环境耐久性测试
- 目的:验证机械在极端环境(温度、湿度、腐蚀)下的性能稳定性。
- 检测内容:
- 高低温循环测试:-40°C~150°C范围内的温度冲击(如汽车零部件)。
- 盐雾测试:评估金属件的抗腐蚀能力(ASTM B117)。
- 湿热老化测试:模拟高温高湿环境(如热带地区设备)。
- 设备:环境试验箱、盐雾试验箱、恒温恒湿箱。
5. 加速寿命试验(ALT)
- 目的:通过强化载荷或环境条件,快速预测产品的实际使用寿命。
- 检测方法:
- 应力加速:提高载荷或频率(如3倍额定负载)。
- 温度加速:利用阿伦尼乌斯模型推算寿命(适用于电子元件)。
- 数据建模:威布尔分布、Arrhenius方程。
6. 功能性耐久测试
- 目的:验证机械在重复操作中的功能保持性(如开关、铰链、阀门)。
- 检测内容:
- 动作循环测试:模拟开关、按钮等部件的操作寿命(如车门铰链10万次开合)。
- 密封性测试:评估密封件在长期压缩后的泄漏率变化。
- 设备:多关节机器人、气密性检测仪。
7. 特殊应用场景测试
- 生物医学器械:人工关节的磨损颗粒分析(ISO 14242)。
- 航空航天:复合材料层压板的热-机械疲劳测试。
- 汽车行业:传动系统的台架耐久试验(如10万公里等效测试)。
检测流程与结果分析
- 需求分析:明确测试目标(寿命预测、失效分析或合规性验证)。
- 载荷谱设计:根据实际工况制定载荷类型(静态、动态、随机)。
- 数据采集:记录应力-应变曲线、温度变化、振动频谱等。
- 失效判定:通过裂纹检测(渗透探伤)、性能衰减阈值或功能异常界定失效。
- 寿命预测:结合S-N曲线(应力-寿命曲线)或损伤累积模型(Miner法则)。
行业意义与发展趋势
- 重要性:避免因机械失效导致的安全事故,降低维护成本(如风电齿轮箱的20年寿命保障)。
- 技术趋势:
- 智能化检测:集成传感器与AI算法实现实时健康监测。
- 多物理场耦合测试:同步模拟机械-热-化学联合作用(如燃料电池双极板)。
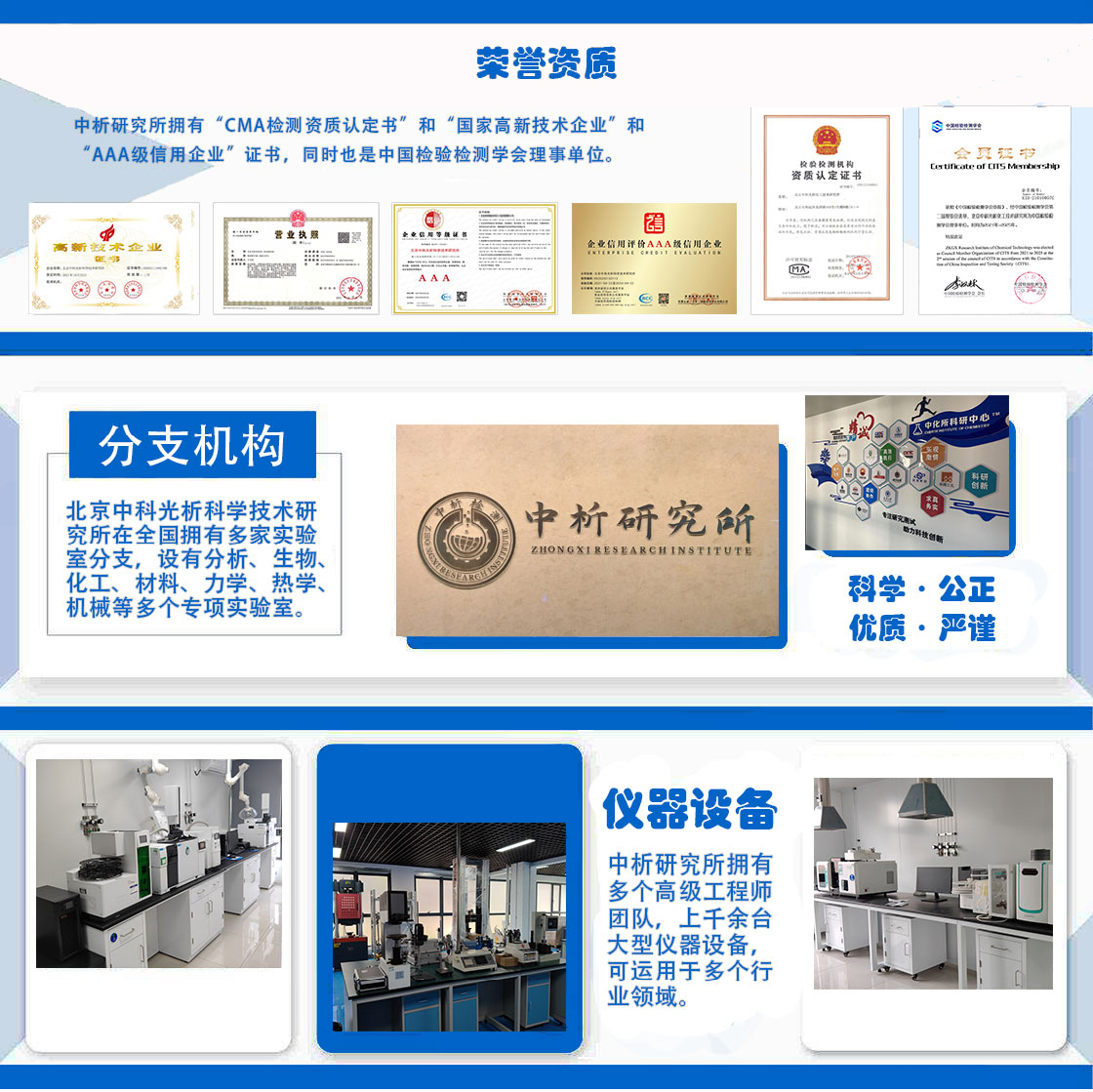
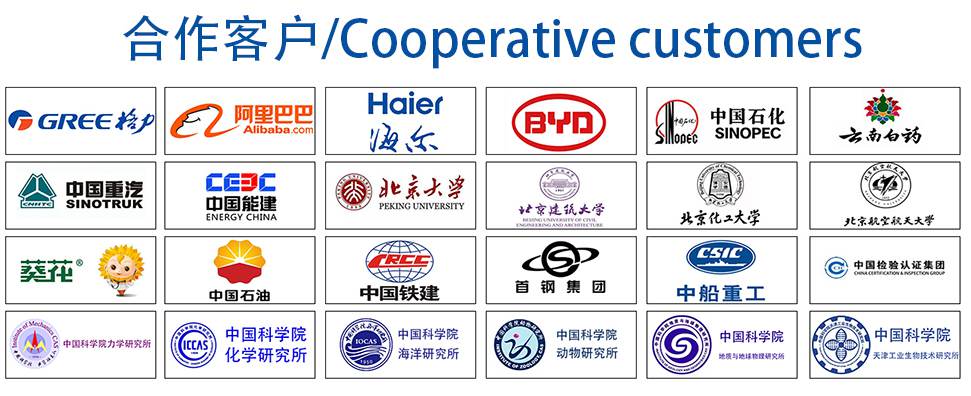
材料实验室
热门检测
271
228
202
211
210
215
225
218
228
229
215
214
218
216
210
205
221
207
220
214
推荐检测
联系电话
400-635-0567