一、基本概念
二、核心检测项目
-
- 频率依赖性测试(1 kHz~10 GHz):评估材料在不同频率下的介电响应,识别适用频段。
- 温度稳定性测试(-50°C~200°C):分析ε与tanδ随温度的变化规律,确保极端条件下的可靠性。
- 湿度敏感性测试:验证材料在潮湿环境中的介电特性退化情况。
-
- 批次一致性检测:通过对比同一材料不同批次的ε和tanδ,确保生产稳定性。
- 行业标准符合性测试(如IEC 60250、ASTM D150):验证材料是否符合国际或行业规范。
-
- 老化试验:通过长期施加电场或高温应力,监测介电性能的退化速率。
- 缺陷定位:利用局部放电检测结合tanδ变化,识别材料内部裂纹或杂质。
-
- 信号完整性分析:针对5G通信、毫米波雷达等场景,测试高频(>1 GHz)下tanδ对信号衰减的影响。
- 阻抗匹配优化:通过ε值调整电路基板设计,减少信号反射。
三、主流检测方法
-
- 原理:利用阻抗比测量电容和损耗。
- 设备:LCR表、高频电桥(如Agilent 4294A)。
- 适用场景:低频(1 kHz~1 MHz)精确测量,适用于电容器介质和绝缘材料。
-
- 原理:通过谐振腔频率偏移计算ε和tanδ。
- 设备:同轴谐振器、微带线谐振器。
- 适用场景:高频(1 MHz~10 GHz)测试,适合微波基板材料评估。
-
- 原理:分析电磁波在材料中的传播时延与衰减。
- 设备:矢量网络分析仪(VNA)。
- 适用场景:高频/高速信号完整性验证(如PCB基材)。
四、标准化检测流程
-
- 加工成标准尺寸(如圆片或矩形),确保表面平整无污染。
- 金属电极镀膜(银浆或溅射)以减少接触阻抗。
-
- 温湿度箱调控测试环境(如25°C±1°C,湿度<30%)。
- 高频测试需屏蔽电磁干扰。
-
- 设定频率范围、电场强度及扫描步长。
- 多点测量取平均值,降低随机误差。
-
- 绘制ε(f)和tanδ(f)曲线,计算温度系数(TCC)。
- 对比行业标准,出具合格性判定。
五、典型应用领域
-
- PCB基材(如FR-4、PTFE)的介电特性筛选。
- 半导体封装材料的吸水率与损耗关联分析。
-
- 变压器绝缘油的tanδ在线监测,预防击穿事故。
- 电缆绝缘层老化评估。
-
- 雷达罩透波材料的宽频介电性能测试。
- 极端温度下航天器介电涂层的稳定性验证。
六、常见问题与解决方案
- 电极边缘效应误差
- 采用保护环电极设计或修正公式补偿。
- 高频测试中的谐振干扰
- 优化样品尺寸与夹具匹配,使用宽带吸波材料。
- 温度漂移影响
- 引入实时温度传感器进行动态校正。
七、
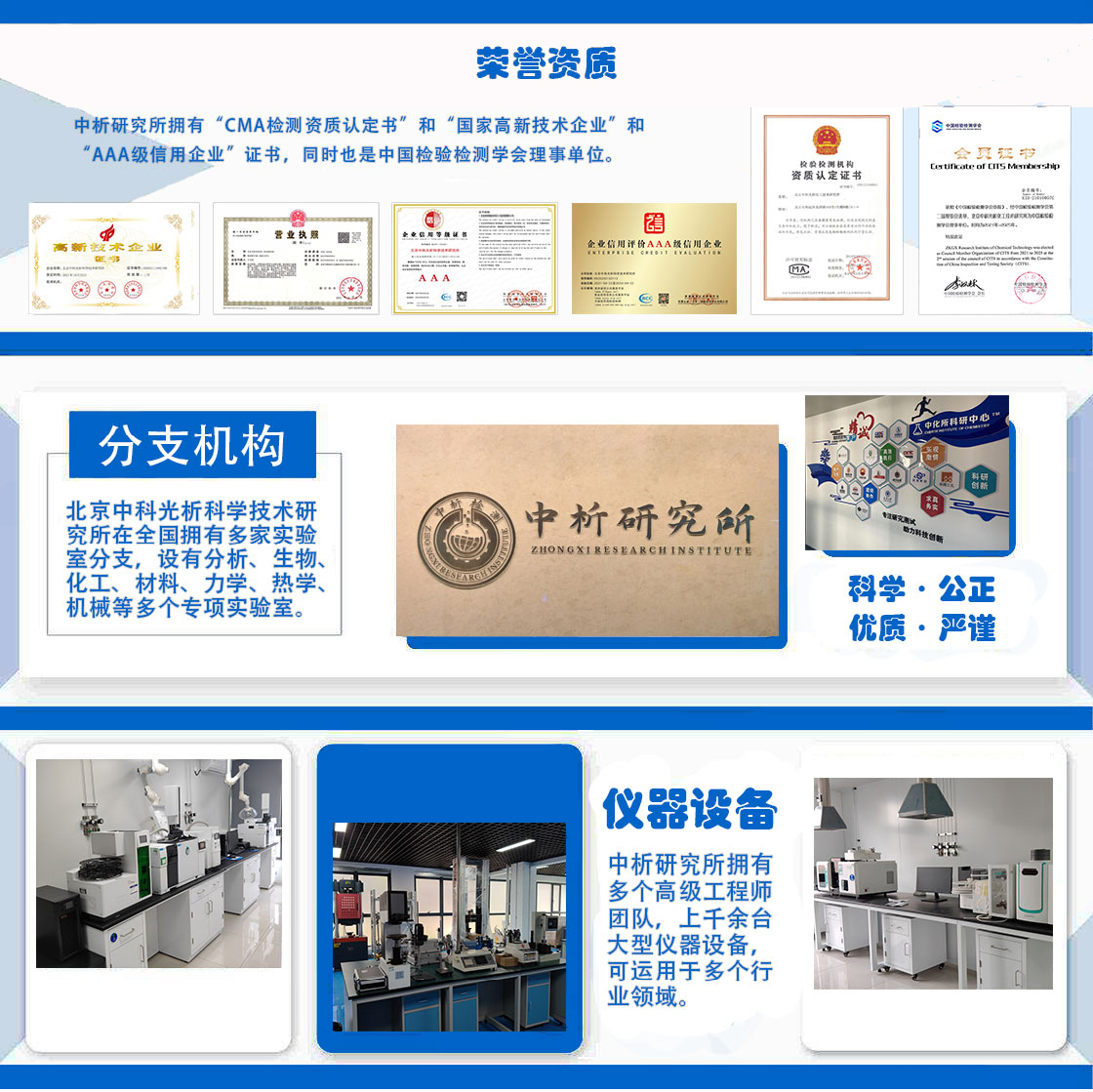
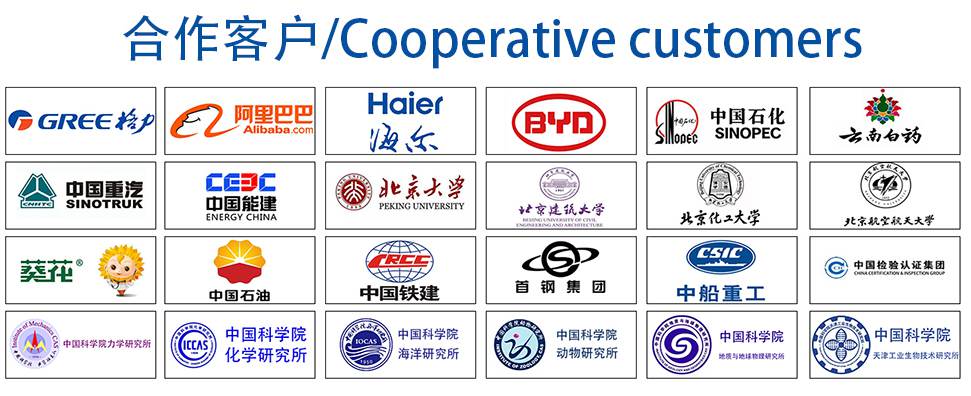
材料实验室
热门检测
271
228
202
211
210
215
225
218
228
229
215
214
218
216
210
205
221
207
220
214
推荐检测
联系电话
400-635-0567