额定夹力检测:核心检测项目与方法详解
一、静态夹力测试
- 传感器校准:使用经过标定的力传感器(如应变片式或压电式传感器)安装在夹持面与被夹持物之间。
- 加载测试:逐步增加夹持力至额定值,记录最大夹持力及稳定时间。
- 误差分析:计算实测值与理论值的偏差(通常要求误差≤±5%)。
二、动态夹力测试
- 模拟运动环境:在振动台或冲击试验机上运行设备,施加周期性或随机性载荷。
- 实时监测:通过高速数据采集系统记录夹持力的瞬时变化,分析峰值、谷值及频率响应特性。
- 失效判定:若动态夹力波动超过额定值的±10%,则判定为不合格。
三、重复性测试
- 循环测试:在固定时间间隔内(如每分钟10次)重复执行夹持-释放动作,循环次数≥1000次。
- 数据统计:计算每次夹持力的标准差,要求重复精度≤±3%。
- 磨损检查:测试后检查夹持部件(如钳口、液压密封件)的磨损情况,分析是否影响性能。
四、过载能力测试
- 渐进加载:以额定夹力的120%~150%作为测试载荷,持续加压至设备触发保护(如泄压阀开启或电机停机)。
- 安全评估:检查设备是否在过载后自动复位,且关键部件无永久性变形或损坏。
五、夹持力保持性能测试
- 模拟故障:在夹持状态下切断动力源(如关闭气泵、液压阀或电源)。
- 力值衰减监测:记录夹持力随时间的变化曲线,要求30分钟内衰减量≤5%。
六、环境适应性测试
- 高低温测试:在-20℃~60℃温度范围内运行设备,检测夹持力波动是否在允许范围内。
- 防尘防水测试:依据IP防护等级标准,模拟粉尘或喷淋环境,评估密封性能对夹持力的影响。
七、安全保护装置检测
- 阈值触发测试:通过人为设置超限夹持力,验证报警信号、急停功能的响应速度和准确性。
- 冗余保护检查:如双传感器监测、机械限位装置等冗余设计是否有效。
八、数据记录与报告
- 所有测试数据需通过数字化系统记录,并生成时间-夹持力曲线、统计图表。
- 检测报告应包含:测试条件、设备型号、检测项目、实测值、判定结果及改进建议。
上一篇:流动混合气体腐蚀检测下一篇:光谱辐射带宽检测
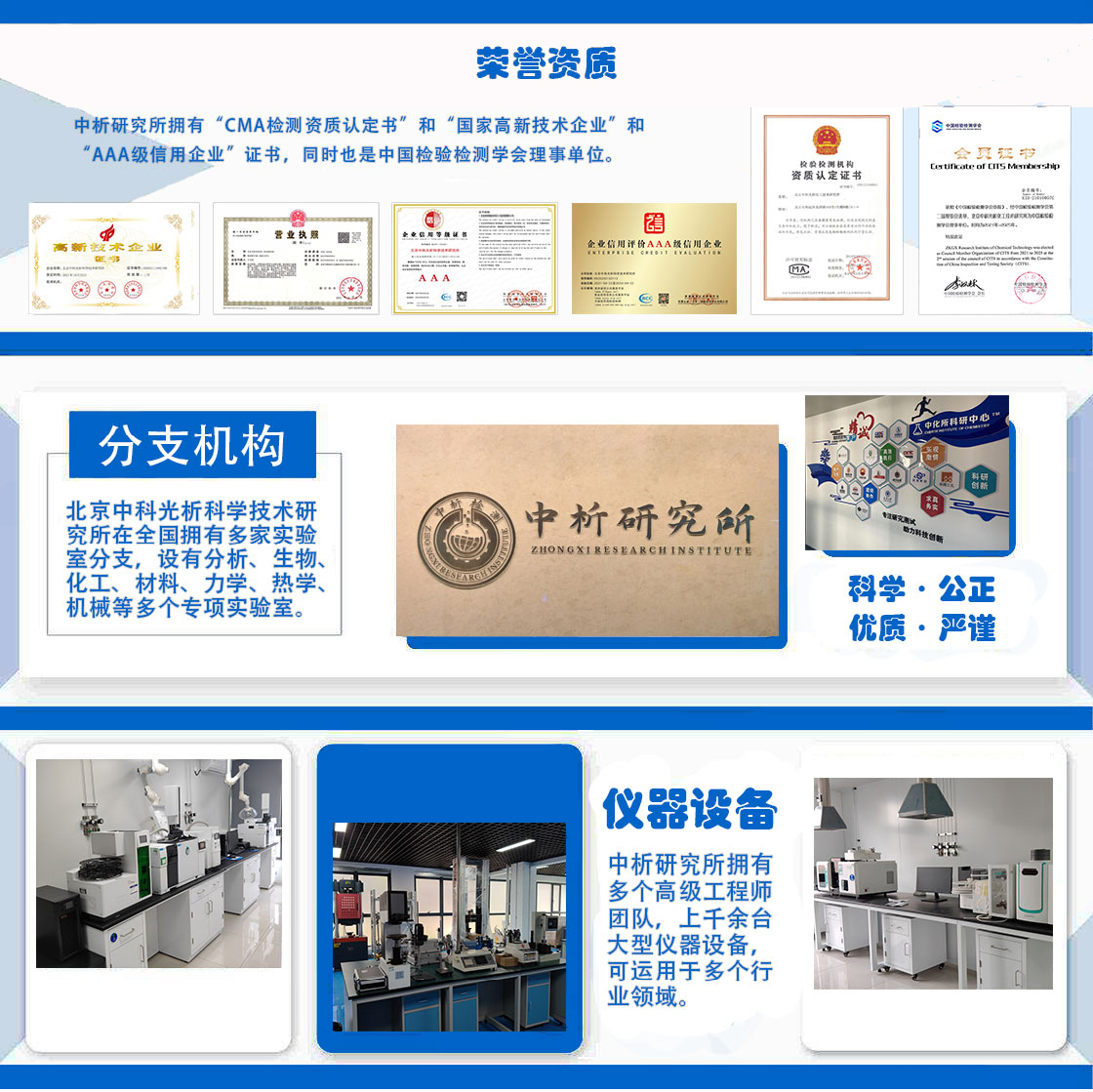
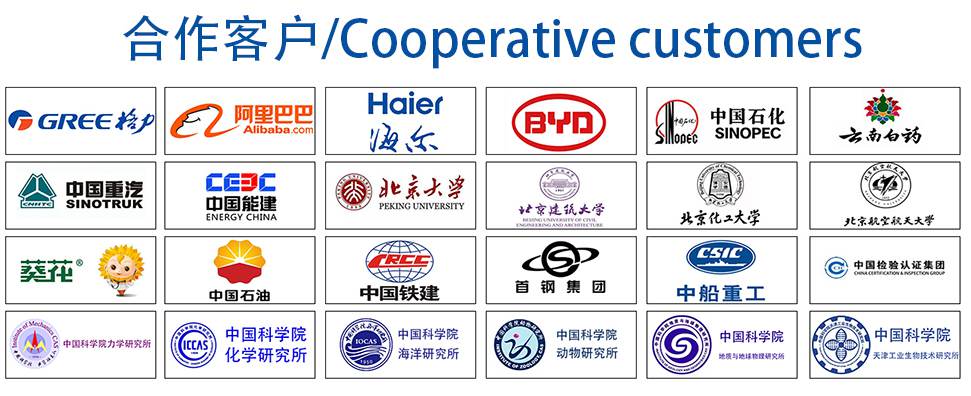
材料实验室
热门检测
254
215
190
203
198
204
210
202
207
217
204
199
204
203
198
195
210
199
209
202
推荐检测
联系电话
400-635-0567