流动混合气体腐蚀检测:核心检测项目与技术解析
一、检测原理与实验装置
二、核心检测项目
1. 腐蚀速率测定
- 方法:通过失重法(ASTM G1)、电化学测试(Tafel极化曲线、EIS)或表面形貌分析(SEM/EDS)计算材料单位时间的腐蚀深度。
- 关键参数:腐蚀速率(mm/year)、质量损失率(g/m²·h)。
- 适用材料:金属(铜、铝、钢)、合金及镀层。
2. 气体成分分析
- 检测内容:
- 实时监测混合气体中各组分浓度(如H₂S、SO₂的ppm级变化)。
- 检测腐蚀产物气体(如H₂释放量)。
- 仪器:气相色谱(GC)、质谱仪(MS)、红外光谱(FTIR)。
3. 表面形貌与成分变化
- 检测项目:
- 腐蚀产物层厚度(截面SEM测量)。
- 表面粗糙度变化(AFM或激光共聚焦显微镜)。
- 元素分布(EDS面扫分析硫、氯等腐蚀性元素富集区域)。
- 案例:电子接插件镀金层在含Cl₂气体中的点蚀评估。
4. 电化学性能测试
- 方法:
- 开路电位(OCP)监测腐蚀倾向。
- 电化学阻抗谱(EIS)分析钝化膜稳定性。
- 动电位极化测试评估局部腐蚀敏感性。
- 标准参考:ISO 17475(电化学腐蚀测试方法)。
5. 力学性能退化
- 检测内容:
- 拉伸强度、硬度变化(ASTM E8/E18)。
- 疲劳寿命(循环载荷测试)。
- 典型应用:汽车排气管材料在含SO₂高温气体中的强度损失评估。
6. 密封性与功能失效
- 检测项目:
- 气密性测试(氦质谱检漏法)。
- 电子元件导通电阻变化(四线法测量)。
- 光学器件透光率下降(分光光度计)。
- 示例:半导体封装在H₂S环境中因银导线硫化导致的短路风险。
7. 长期老化模拟
- 加速试验设计:
- 通过提高气体浓度(10-100倍实际环境)或温湿度,实现数周内模拟数年腐蚀效果。
- 验证模型:Arrhenius方程(温度加速)、Peck模型(温湿度耦合加速)。
三、检测流程标准化
- 样品预处理:清洁、干燥、初始质量/形貌记录。
- 实验条件设置:按ISO 22479或IEC 60068-2-60标准设定气体比例、温湿度及流速。
- 动态监测:每隔24-72小时采集腐蚀数据。
- 终止条件:达到预设时间或腐蚀失效阈值(如电阻上升50%)。
- 后处理分析:清洗腐蚀产物(ASTM G1)、对比失效模式。
四、行业应用场景
- 电子行业:PCB焊点抗硫化、LED芯片防氯腐蚀。
- 汽车工业:燃料电池双极板耐SO₂性能。
- 能源领域:油气管道在H₂S/CO₂混合气体中的应力腐蚀开裂(SCC)评估。
- 航空航天:钛合金部件在含盐雾与NO₂环境中的耐久性测试。
五、质量控制关键点
- 气体纯度:避免杂质气体干扰(如O₂含量需控制在±0.1%)。
- 流速均匀性:采用多孔分流器确保样品表面气流分布一致。
- 温湿度校准:使用NIST可追溯传感器,湿度误差≤±2% RH。
- 重复性验证:平行样品数≥3组,数据偏差<15%。
六、未来技术趋势
- 智能监测系统:集成AI算法实时预测腐蚀临界点。
- 微区分析技术:飞行时间二次离子质谱(TOF-SIMS)实现纳米级腐蚀机理研究。
- 多因素耦合测试:同步施加机械应力、电场等复合载荷。
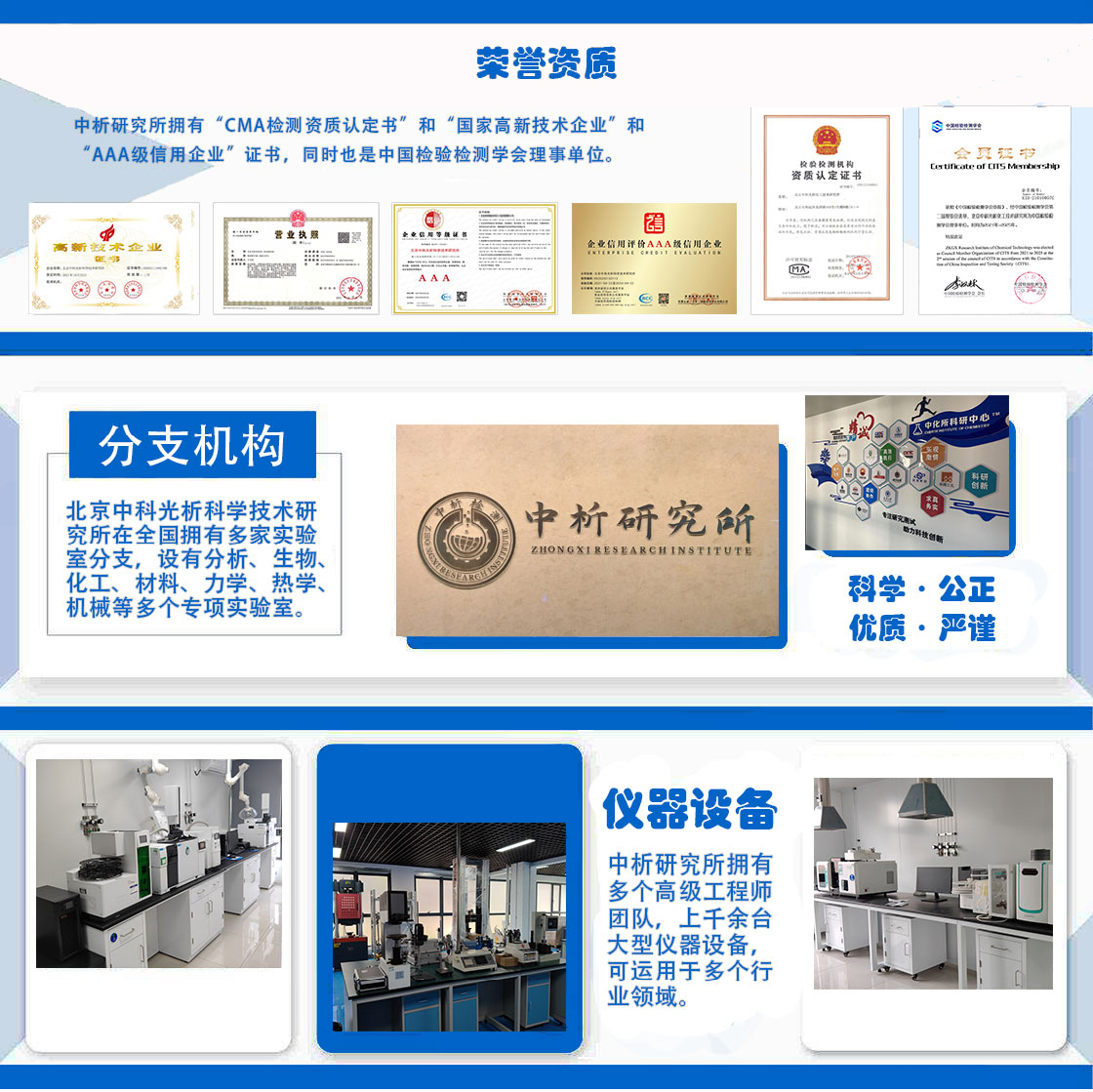
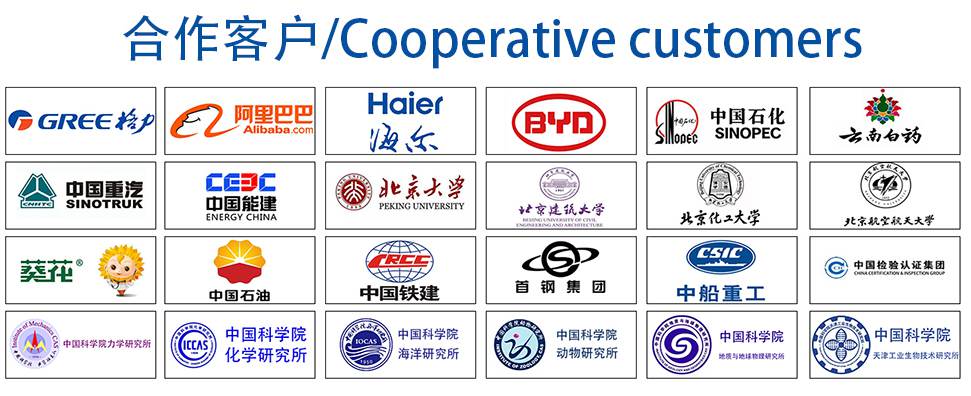
材料实验室
热门检测
254
215
189
203
197
204
209
201
207
217
203
199
197
203
196
195
207
199
209
201
推荐检测
联系电话
400-635-0567