标志耐久性检测:核心检测项目详解
一、理化性能检测
-
- 目的:评估标志涂层或印刷层与基材的结合强度。
- 方法:采用划格法(ISO 2409)、胶带剥离法(ASTM D3359)或拉开法(ASTM D4541)。
- 标准:涂层附着力等级需达到行业标准(如≥4B为合格)。
-
- 目的:模拟标志表面在摩擦或机械磨损下的耐用性。
- 方法:使用Taber耐磨试验机(ASTM D4060)或落砂试验(ASTM D968),记录磨损前后的重量损失或目视变化。
- 标准:耐磨次数或磨损深度需符合特定应用场景要求(如交通标志需满足≥5000次摩擦无脱落)。
-
- 目的:验证标志在物理冲击下的抗碎裂或变形能力。
- 方法:通过落球冲击试验(ISO 6272)或摆锤冲击测试(ASTM D2794)。
- 标准:冲击后无明显裂纹或分层。
二、环境耐受性检测
-
- 目的:评估标志在阳光暴晒下的褪色、粉化或脆化程度。
- 方法:使用QUV加速老化试验箱(ASTM G154),模拟紫外光、温度及湿度循环。
- 标准:经过1000小时测试后,色差ΔE≤3,无开裂或剥落。
-
- 目的:验证金属标志或涂层在海洋或工业环境中的耐腐蚀性。
- 方法:依据中性盐雾试验(ASTM B117)或循环腐蚀试验(ISO 9227)。
- 标准:连续喷雾72小时后,表面锈蚀面积<5%。
-
- 目的:模拟极端温度与湿度变化对标志的影响。
- 方法:高低温交变试验箱(IEC 60068-2-30),设定-40℃至85℃循环。
- 标准:循环20次后无起泡、翘曲或剥离。
三、化学耐受性测试
-
- 目的:检测标志在接触清洁剂、油污等化学物质时的稳定性。
- 方法:用棉布蘸取酒精、汽油等溶剂擦拭表面(ASTM D5402)。
- 标准:擦拭50次后无明显褪色或溶解。
-
- 目的:评估标志在工业污染或酸雨环境中的耐受能力。
- 方法:浸泡于pH=2的硫酸溶液或pH=12的氢氧化钠溶液中(ISO 2812)。
- 标准:浸泡24小时后无变色或腐蚀。
四、特殊应用场景测试
-
- 目的:验证标志材料的防火性能(适用于公共场所)。
- 方法:垂直燃烧试验(UL94)或氧指数测试(ASTM D2863)。
- 标准:达到V-0级或氧指数≥28%。
-
- 目的:防止非法广告粘贴(常见于公共设施标志)。
- 方法:施加胶粘剂后剥离,检测残留物比例(EN ISO 16931)。
- 标准:残留面积<5%。
-
- 目的:检验标志在低温结冰状态下的结构完整性。
- 方法:将样品浸泡水中后冻结,再解冻重复数次(ASTM C666)。
- 标准:50次循环后无开裂或分层。
五、功能性检测
-
- 目的:确保夜间或低光照条件下的可见性。
- 方法:使用逆反射系数测量仪(ASTM E810)。
- 标准:符合《GB/T 18833-2012》中关于逆反射系数的要求。
-
- 目的:验证LED屏等电子标志的寿命与稳定性。
- 方法:连续通电老化试验(IEC 60068-2-1)及防水测试(IP等级)。
- 标准:MTBF(平均无故障时间)≥10,000小时,防水等级≥IP65。
六、检测标准选择依据
- 应用场景:户外、室内、高温、高湿等;
- 材料类型:金属、塑料、反光膜、陶瓷等;
- 行业规范:交通、建筑、电子、化工等领域的特定标准(如ISO、GB、DIN)。
上一篇:集电极-发射极截止电流检测下一篇:语音检听检测
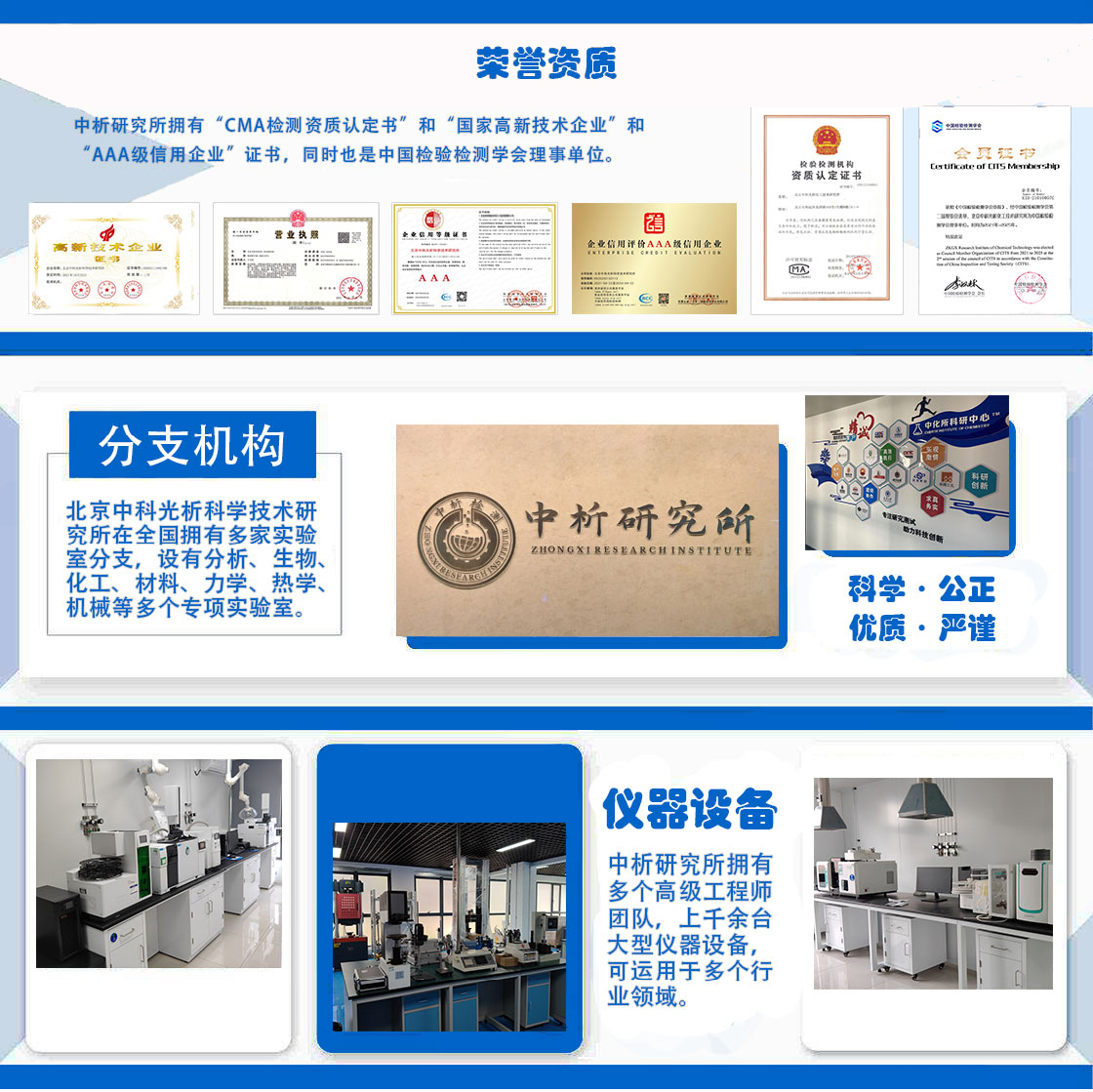
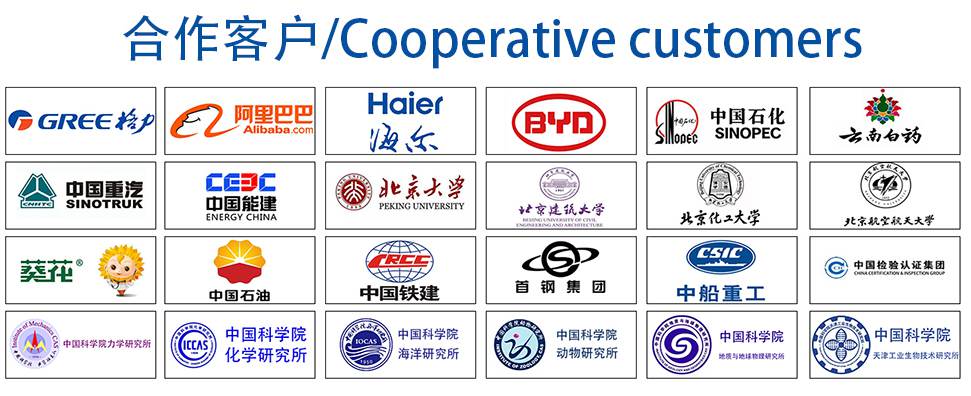
材料实验室
热门检测
254
214
189
203
196
204
209
201
207
217
203
199
197
203
195
194
207
198
209
201
推荐检测
联系电话
400-635-0567