静电耐受性检测:核心检测项目详解
一、核心检测项目
-
- 原理:直接对设备导电部位(如金属接口)施加静电脉冲。
- 测试电压:通常为2kV至8kV(消费电子),汽车电子可达15kV。
- 适用场景:USB端口、按键等人体可接触区域。
-
- 原理:通过电弧对非导电表面(如塑料外壳)放电,模拟人体持金属物接近设备的场景。
- 测试电压:最高30kV(如工业设备)。
- 关键点:放电枪头形状(尖头/圆头)影响结果。
-
- 模拟对象:附近物体放电产生的电磁场耦合干扰。
- 方法:对水平耦合板(HCP)或垂直耦合板(VCP)放电,设备置于10cm外。
- 典型应用:汽车电子控制单元(ECU)的抗干扰测试。
-
- 目的:确定设备失效的临界电压值。
- 步骤:阶梯式增加电压(如±2kV、±4kV),监测功能异常点。
-
- 特点:模拟带电人体通过金属工具(如钥匙)对系统放电。
- 适用对象:整机设备(如服务器、车载中控屏)。
二、检测流程标准化
-
- 温度23±3℃,湿度30%-60%(防止环境干扰结果)。
- 设备测试状态:通电运行并满载工作。
-
- 高风险区域:接口、缝隙、散热孔等易放电部位。
- 覆盖率要求:每个类型至少选3个点,确保全面性。
-
- IEC 61000-4-2:消费电子主流标准,规定放电次数(单点10次正/负极化)。
- ISO 10605:汽车电子标准,测试电压更高(如25kV接触放电)。
- ANSI/ESDA/JEDEC JS-001:半导体器件敏感度分级依据。
三、结果评估关键指标
-
- A级:无性能下降,完全正常。
- B级:暂时性故障,可自动恢复。
- C级:需人工重启才恢复。
- D级:永久损坏。
-
- 记录每次放电的电压、波形、设备响应(如屏幕闪烁、通信中断)。
- 使用高速示波器捕捉瞬态电压(如纳秒级脉冲)。
四、行业应用差异
行业 | 测试重点 | 典型标准 |
---|---|---|
消费电子 | 接触/空气放电(±8kV) | IEC 61000-4-2 |
汽车电子 | 间接放电、30kV空气放电 | ISO 10605 |
医疗设备 | 严苛阈值(±15kV接触放电) | IEC 60601-1-2 |
军工航天 | 全项目覆盖、极端环境适应性 | MIL-STD-883G Method 3015 |
五、常见误区与对策
- 误区1:仅测试常温环境。 对策:增加高低温循环测试(-40℃~85℃),验证材料膨胀导致的放电风险。
- 误区2:忽略软失效(Soft Failure)。 对策:监测隐蔽性故障(如数据包错误率、时钟偏移)。
- 误区3:未更新标准版本。 对策:跟踪标准修订(如IEC 61000-4-2:2008 vs. 2018版差异)。
六、未来趋势
- 智能化测试:AI自动识别敏感点,优化测试路径。
- 微型化挑战:5G设备中纳米级芯片的ESD防护设计。
- 材料创新:石墨烯、导电聚合物在屏蔽中的应用。
上一篇:接触电阻检测下一篇:集电极-发射极截止电流检测
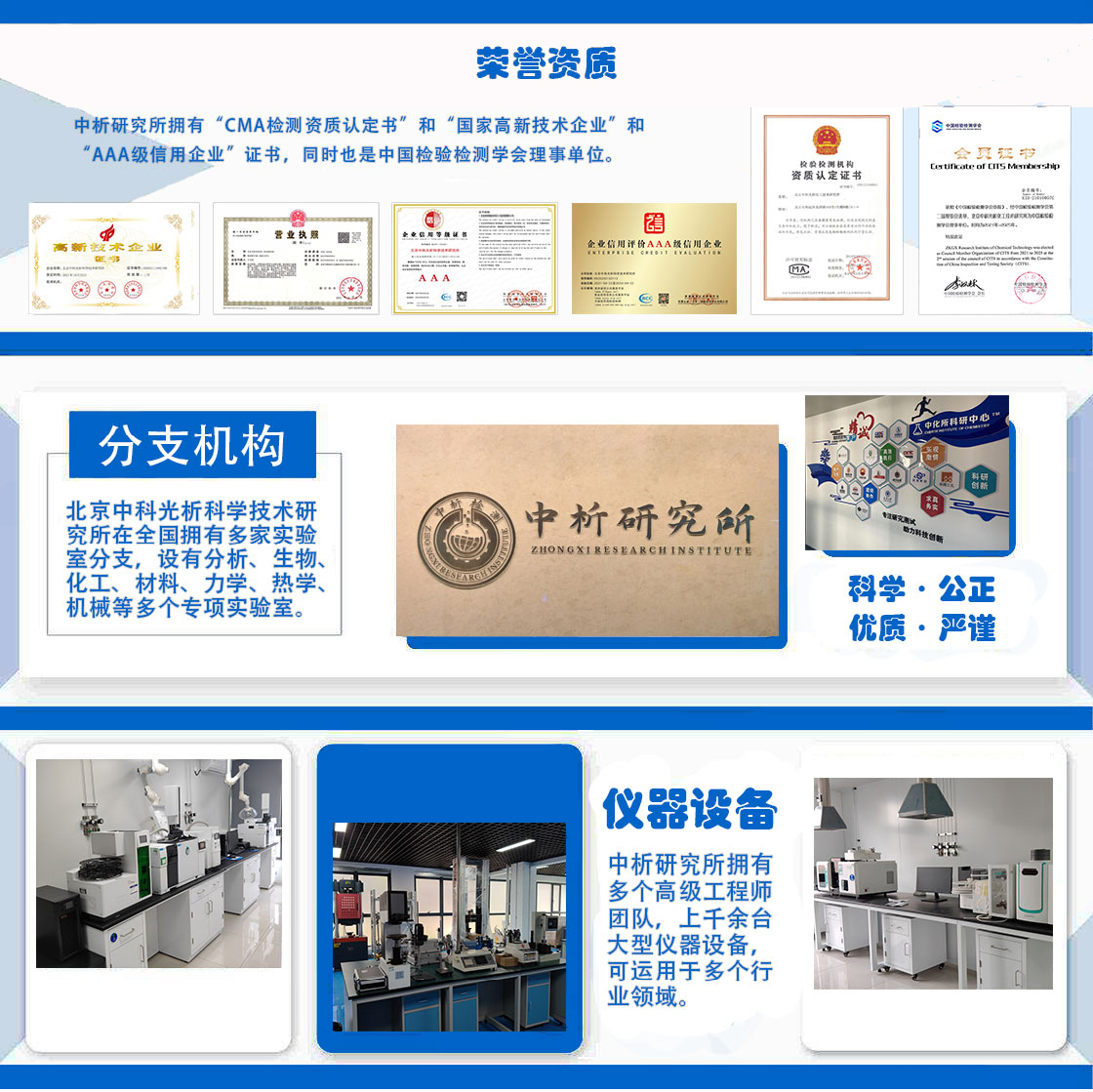
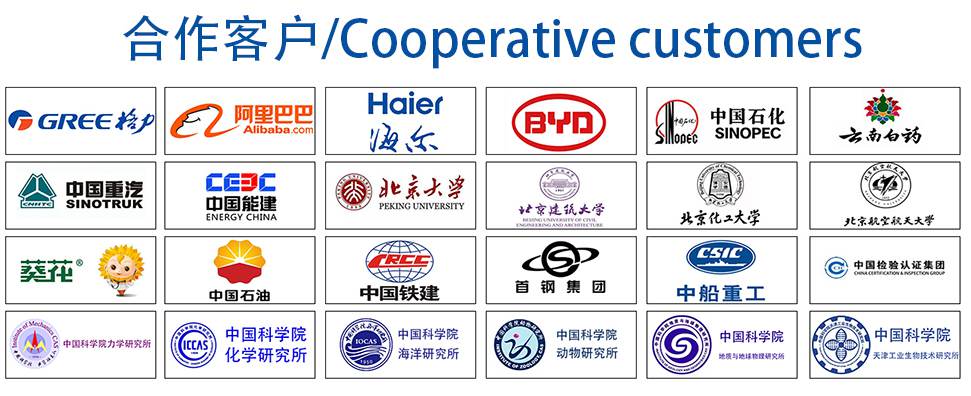
材料实验室
热门检测
254
214
189
203
196
204
209
201
207
217
203
199
197
203
195
193
207
198
209
201
推荐检测
联系电话
400-635-0567