集电极-基极截止电流(ICBO)检测项目详解
一、ICBO的定义与重要性
二、核心检测项目及方法
1. 常温ICBO测试
- 测试条件:
- 环境温度:25℃ ±2℃。
- 集电极-基极电压(V_CB):按器件规格书设定(通常为额定最大值)。
- 基极开路,发射极接地。
- 步骤:
- 连接电路(集电极接可调电源正极,基极悬空,发射极接地)。
- 施加V_CB至目标电压,稳定后记录电流值。
- 判定标准:测量值需低于规格书标称的最大ICBO(如100nA)。
2. 高温ICBO测试
- 测试条件:
- 温度:根据应用场景选择(如85℃、125℃)。
- V_CB保持常温测试值。
- 步骤:
- 将器件置于恒温箱,升温至目标温度并稳定30分钟。
- 重复常温测试步骤,记录高温下ICBO。
- 意义:验证器件在高温环境下的漏电流特性,通常ICBO随温度指数级增长。
3. 反向击穿电压(_CBO)测试
- 测试目的:确定集电结反向击穿临界点。
- 步骤:
- 逐步增加V_CB,监测电流变化。
- 当电流急剧上升时记录电压值,即为_CBO。
- 注意事项:需限流保护,防止器件永久损坏。
4. 电压依赖性测试
- 测试内容:分析ICBO随V_CB变化的趋势。
- 方法:
- 在V_CB额定范围内选取多个电压点(如10V、20V、30V),测量对应电流。
- 绘制ICBO-V_CB曲线,评估线性度是否符合预期。
5. 温度循环测试
- 目的:验证器件在温度冲击下的稳定性。
- 流程:
- 将器件在-40℃~125℃间循环多次(如50次)。
- 每次循环后测试ICBO,观察参数漂移。
6. 长时间稳定性测试
- 方法:
- 在额定V_CB和高温下持续通电48~72小时,定时记录ICBO。
- 分析电流随时间的变化率,评估器件寿命。
三、测试设备与注意事项
- 关键设备:
- 高精度电流表(分辨率≤1nA)。
- 可编程直流电源(稳定性±1mV)。
- 恒温箱(控温精度±1℃)。
- 注意事项:
- 避免静电放电(ESD),测试前对设备及人员接地。
- 确保测试夹具接触良好,减少接触电阻引入误差。
- 校准仪器,消除零点漂移影响。
四、结果分析与案例
- 典型失效模式:
- ICBO超标:可能是晶圆污染或封装缺陷导致漏电路径。
- _CBO过低:集电结掺杂工艺异常。
- 案例:某开关电源中晶体管高温ICBO骤增,导致待机功耗超标。经检测发现封装内部存在湿气,重新烘烤后参数恢复。
五、
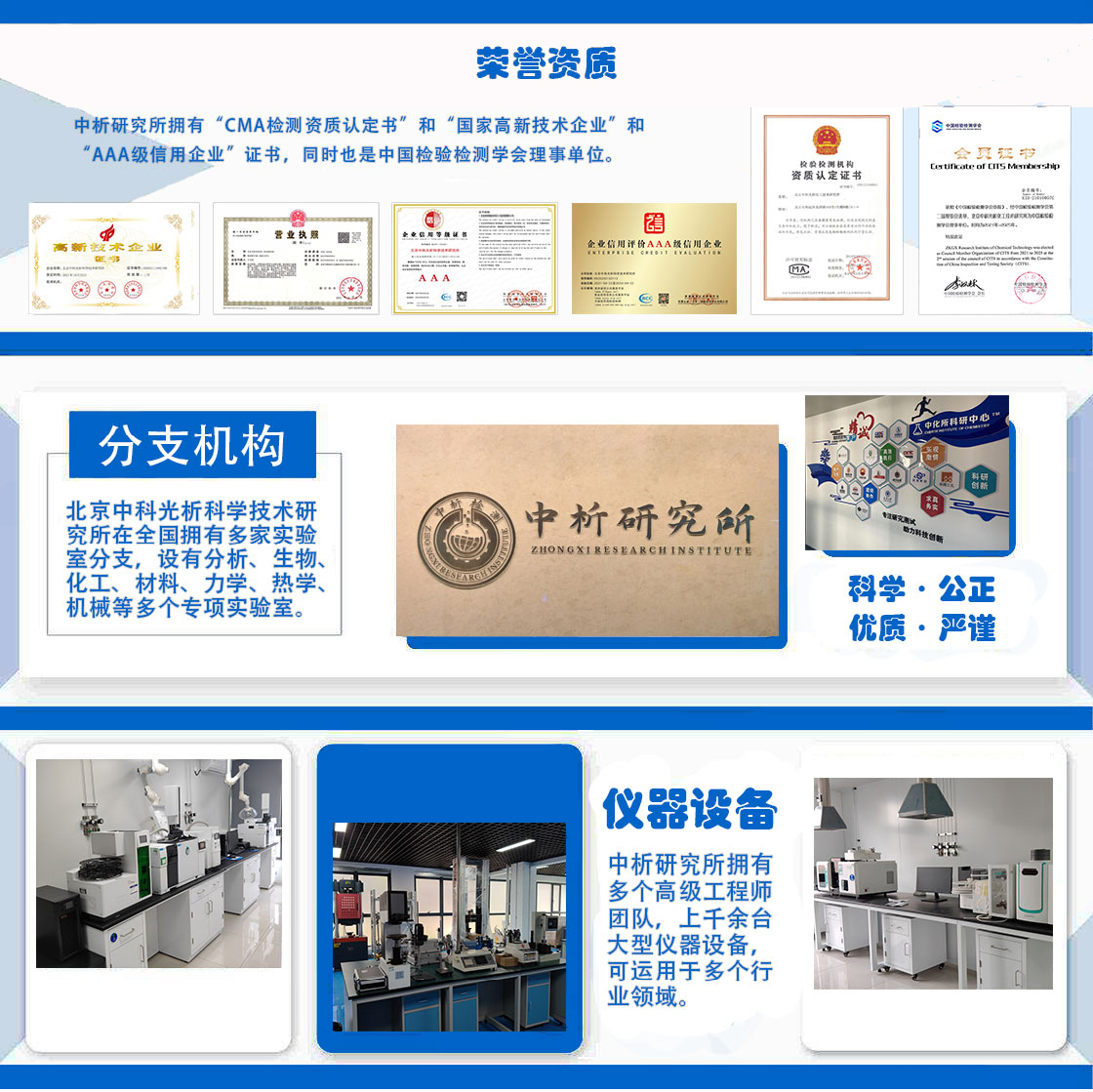
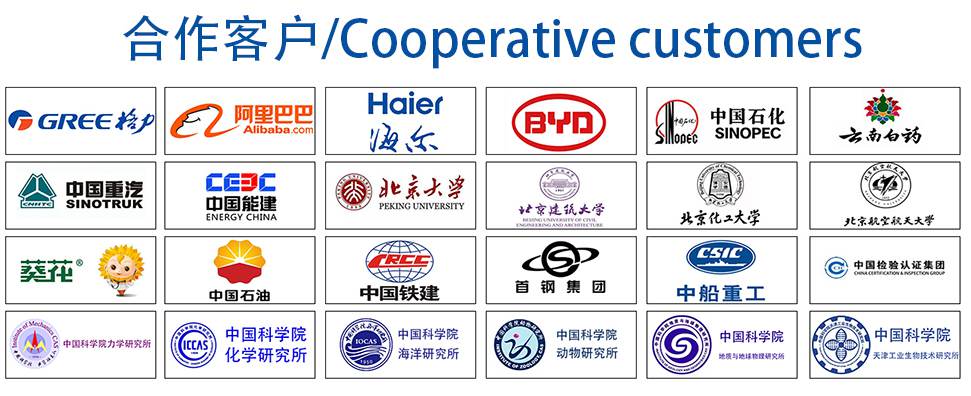
材料实验室
热门检测
254
215
189
203
197
204
209
201
207
217
203
199
198
203
197
195
209
199
209
202
推荐检测
联系电话
400-635-0567