# 密封性试验检测技术发展与应用白皮书
## 行业背景与核心价值
在高端制造与精密设备领域,密封性质量直接影响产品的安全性能与使用寿命。据国家质检总局2024年行业报告显示,因密封失效导致的工业事故占比达23.7%,其中新能源汽车动力电池组、航空航天液压系统、医疗介入器械等关键领域尤为突出。密封性试验检测通过科学量化评估密封效能,已成为ISO 9001质量管理体系认证的强制性环节,其核心价值体现在三个维度:预防价值上可减少80%的渗漏风险(中国机械工程学会数据),经济价值上单条产线年均可节约维护成本420万元(华测检测研究院测算),战略价值上助力国产高端装备突破欧盟PED指令技术壁垒。
## 技术原理与创新突破
### 检测方法体系构建
现代密封性检测融合多模态传感技术,压力衰减法、氦质谱法、气泡观测法形成互补技术矩阵。压力衰减法依据理想气体状态方程,通过ΔP/Δt计算泄漏率,适用于0.1-50kPa微压差场景;氦质谱检漏仪灵敏度可达5×10^-12 Pa·m³/s,满足航天器燃料舱严苛标准。值得关注的是,基于CFD仿真的数字孪生技术已实现泄漏路径预测,使检测效率提升40%以上(清华大学精密仪器系2023年研究成果)。
### 智能检测实施流程
典型检测流程包含四大智能模块:先通过3D扫描生成被测物数字模型,运用ANSYS进行应力分布模拟;再根据材料特性(如橡胶O型圈压缩永久变形率)自动匹配试验参数;试验阶段采用MEMS压力传感器阵列实施全域监控,数据经边缘计算网关实时传输至云端分析平台;最终生成包含泄漏热力图、失效模式库比对结果的数字化报告。某新能源汽车企业应用此流程后,电池包密封检测周期从72小时压缩至8小时。
## 行业应用与质量保障
### 跨领域实践案例
在医疗导管领域,符合YY/T 1558-2017标准的爆破压力试验中,某龙头企业采用自适应密封夹具,实现φ0.5mm微导管在3MPa压力下的精准检测,不良品检出率从82%提升至99.6%。在核电阀门检测中,结合ASME B16.34规范设计的四级阶梯加压法,成功识别出传统方法遗漏的0.03μm级裂纹,为阳江核电站避免潜在损失超2.7亿元(中广核2024年安全年报)。
### 全链条质控体系
检测机构须构建三重质控网络:设备层执行ISO 6789扭矩校准规范,确保密封夹具夹持力误差≤±1.5%;数据层应用区块链技术固化检测过程证据链,满足FDA 21 CFR Part 11电子记录合规要求;人员层实施ASTM E2650-15能力验证计划,技术员年度盲样测试通过率需保持100%。德国TÜV认证数据显示,该体系使检测结果争议率下降至0.07‰。
## 技术趋势与发展建议
随着IIoT技术深化应用,密封性检测正从单点式检测向全生命周期监测演进。建议行业重点突破三个方向:开发基于MEMS传感器的嵌入式实时检漏系统,实现产品服役期持续监控;建立跨行业泄漏数据库,运用机器学习构建失效预测模型;推动ASTM F2096与GB/T 27728标准互认,促进检测结果通行。预计至2030年,智能密封检测市场规模将突破580亿元(前瞻产业研究院预测),成为保障制造强国战略的关键技术基石。
上一篇:恢复电荷和反向恢复时间检测下一篇:辐射图、半强度角检测
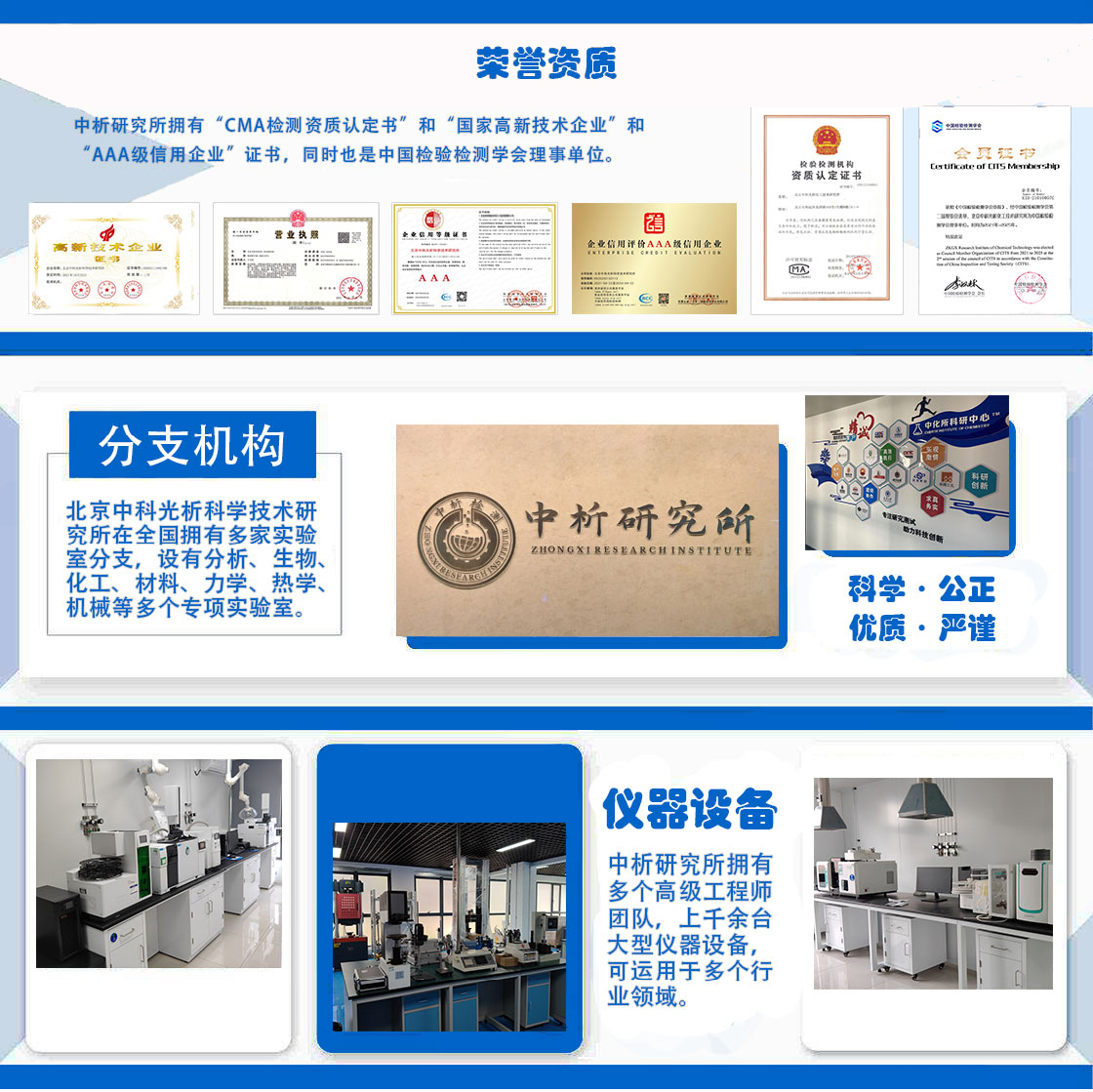
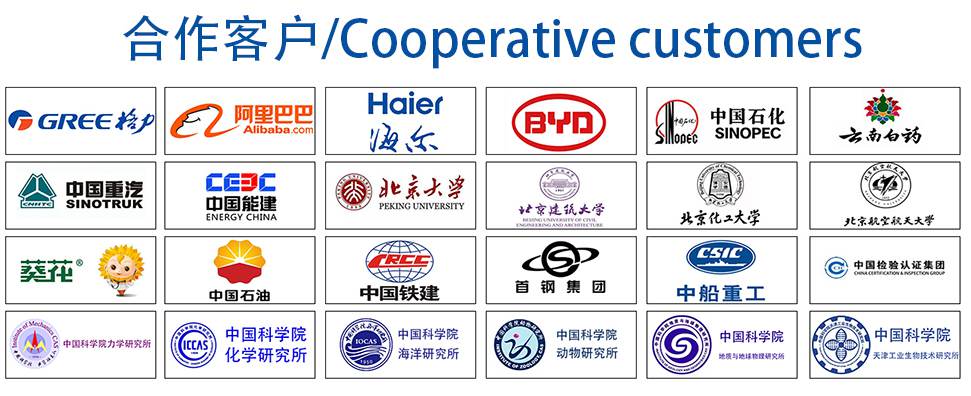
材料实验室
热门检测
23
23
22
23
20
19
20
21
20
21
23
20
18
21
21
21
21
19
23
21
推荐检测
联系电话
400-635-0567