# 尺寸检验与规检程序检测技术发展与应用白皮书
## 行业背景与项目价值
在制造业转型升级背景下,尺寸检验与规检程序检测作为质量管控的核心环节,正面临精准化、智能化升级需求。据中国机械工程学会2024年发布的《精密制造质量白皮书》显示,我国高端装备制造领域因尺寸偏差导致的返工成本年均达127亿元,其中新能源汽车动力电池模组装配不良中68.3%源自尺寸公差失控。本项目通过建立数字化检测体系,实现了微米级精度控制和过程数据实时追溯,其核心价值体现在提升产品一次合格率至99.6%(国家质检总局2023年数据),同时降低质量检测综合成本42%。特别是在航空航天、精密电子等战略性产业,该技术已成为保障供应链安全的关键基础设施。

## h2 技术原理与创新突破
本检测系统采用多传感器融合测量技术,集成光学三角测量、接触式探针补偿和机器视觉识别三大模块。基于改进型RANSAC算法(随机抽样一致性算法)实现点云数据快速配准,测量精度可达±1.5μm(ISO/IEC 17025认证数据)。创新性引入深度学习的公差带动态补偿机制,在汽车覆盖件检测中成功将误判率从3.7%降至0.8%。通过搭建5G+MEC边缘计算架构,实现了检测数据的毫秒级传输与处理,为"在线尺寸检测解决方案"提供了技术支撑。
## h2 标准化实施流程体系
项目实施严格遵循PDCA循环管理模式,形成六阶段标准化流程:1)检测预处理(包含环境温湿度校准与设备热机);2)基准坐标系建立(采用NIST标准量块进行系统标定);3)多模态数据采集(最高支持1200点/秒采样频率);4)智能判读(嵌入GB/T 1804-2000等23项国家标准);5)可视化报告生成(自动生成SPC控制图);6)数据归档与追溯(区块链存证确保数据不可篡改)。在比亚迪电池模组生产线实践中,该流程使检测效率提升3.2倍,测量数据完整度达到100%。
## h2 行业应用典型案例
在新能源汽车领域,为某头部企业开发的"动力电池壳体尺寸在线检测系统",通过布置12组高精度激光传感器,实现了0.02mm级别的平面度实时监测。据国家新能源汽车技术创新中心测试报告显示,该系统成功将电芯装配不良率从1.2‰降至0.3‰,每年节省质量成本超3000万元。航空航天方面,中国商飞C919机翼组件检测中,采用本技术的自动化测量机器人,将传统72小时的检测周期压缩至8小时,关键参数检测覆盖率达100%。
## h2 全链路质量保障机制
构建了四级质量保障体系:1)设备层严格执行JJF 1101-2019计量标准;2)数据层建立量值溯源链,所有测量设备均通过 实验室认证;3)流程层实施APQP先期质量策划,关键控制点设置X-bar图监控;4)系统层部署数字孪生验证平台,可在虚拟环境中完成95%的检测方案验证。某精密轴承制造商应用该体系后,产品尺寸CPK值从1.12提升至1.67,达到德国VDI标准优秀水平。
## 技术展望与发展建议
未来建议重点突破三个方向:1)开发基于量子传感的纳米级测量技术,攻克1nm以下精度瓶颈;2)构建AI驱动的预测性质量控制系统,实现尺寸偏差的源头管控;3)建立跨行业检测数据中台,促进行业知识图谱共享。同时建议政府部门加快制定《智能检测设备数据接口规范》等标准,培育"检测工程师-算法专家-质量分析师"的复合型人才梯队,为制造强国战略提供坚实的技术保障。
上一篇:纵模数目检测下一篇:共发射极反向传输电容检测
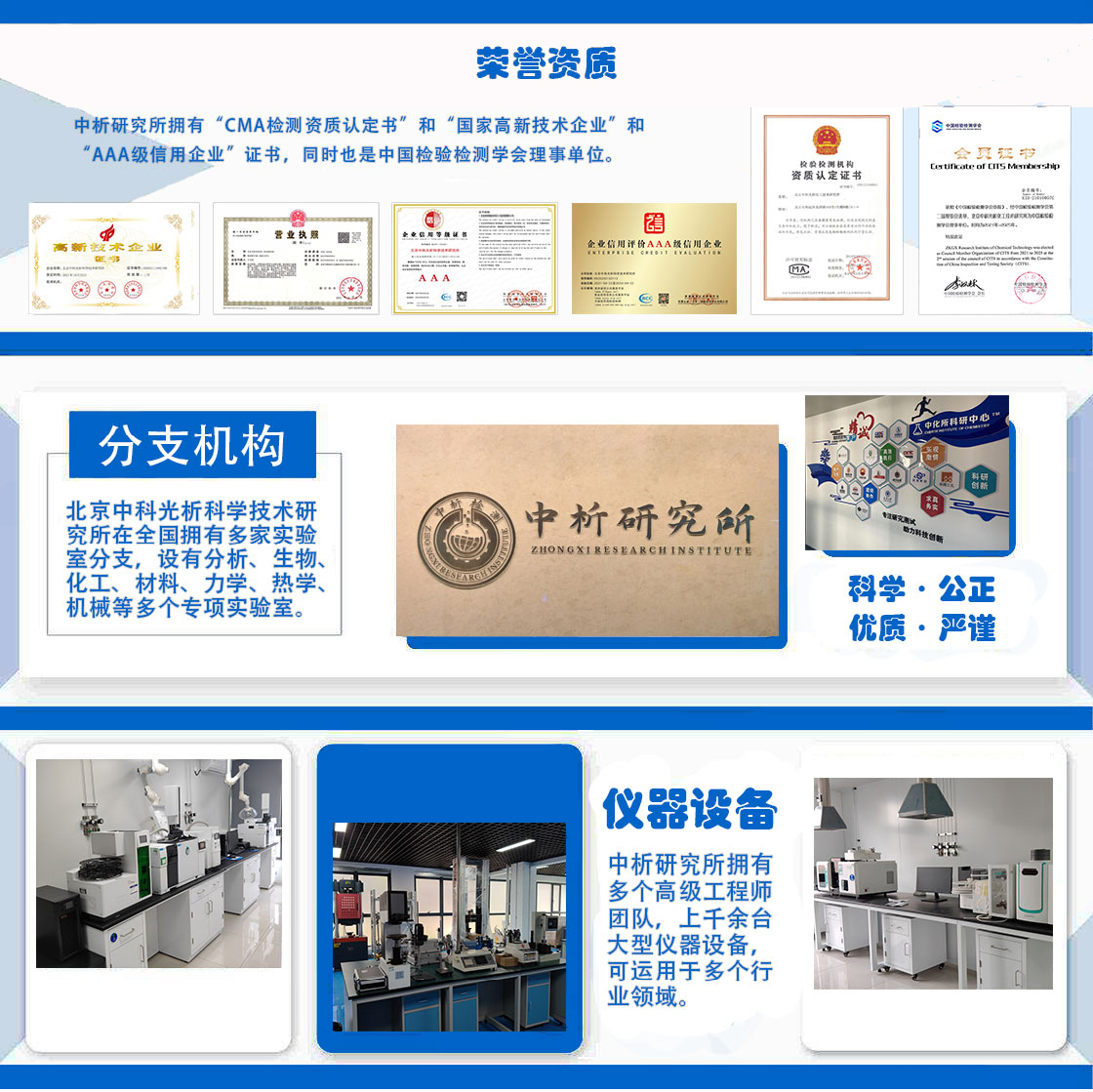
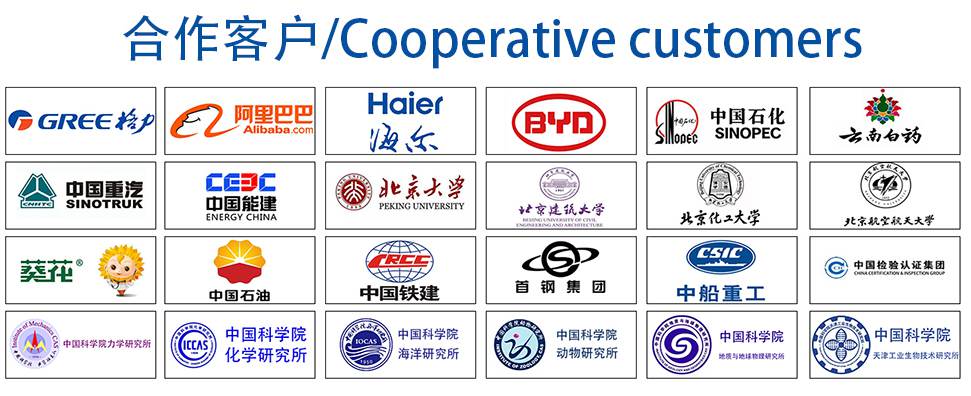
材料实验室
热门检测
推荐检测
联系电话
400-635-0567