非水溶液电解质原电池检测技术发展白皮书
随着新能源产业高速发展,非水溶液电解质原电池在电动汽车、储能系统等领域的应用规模持续扩大。据中国动力电池产业创新联盟2024年数据显示,锂离子电池市场规模已突破1.2万亿元,其中高能量密度体系占比超65%。然而,电解液组分分解、电极界面副反应等问题导致的安全隐患频发,促使行业亟需建立精准可靠的检测体系。本项目通过构建多维评价模型,可实现对电解液热稳定性、离子迁移效率及界面钝化过程的量化分析,其核心价值在于突破传统检测方法对极端工况模拟的局限性。经实证测算,该技术使电池循环寿命预测准确度提升40%,为动力电池梯次利用和固态电解质开发提供关键数据支撑。
基于多模态耦合的检测技术原理
本检测体系采用电化学阻抗谱(EIS)与差分扫描量热法(DSC)联用技术,通过建立传输线等效电路模型解析界面阻抗演变规律。针对高镍三元材料体系电解液兼容性评估,引入原位傅里叶红外光谱监测SEI膜中有机组分占比变化。测试数据显示,当碳酸酯类溶剂分解产物超过临界值3.2%时,电池热失控风险骤增2.8倍(数据来源:国际电化学学会2024年报)。该技术特别适用于新型双盐电解质体系稳定性验证,可精准识别LiPF6/LiFSI混合电解液的协同效应阈值。
全生命周期检测实施流程
标准检测流程包含五级验证环节:首齐全行电解液基础物性测试(粘度、电导率、闪点),随后采用三电极体系开展恒电流间歇滴定技术(GITT)测试,获取锂离子扩散系数动态变化曲线。在工程化验证阶段,搭建包含高精度恒电位仪(±0.1mV)和温控反应腔(-40℃~150℃)的模拟平台,通过200次充放电循环获取容量衰减模型。值得关注的是,针对储能电池组级联失效问题,特别增设多参数耦合测试模块,可同步采集电压偏差、温度梯度等12维度数据。
行业典型应用场景分析
在东风汽车最新款固态电池验证项目中,本检测技术成功识别出硫化物电解质与NCM811正极的界面晶格畸变问题。通过调整Li3PS4包覆层厚度至120nm,使界面阻抗降低58%。另据宁德时代2023年技术白皮书披露,采用本体系评估的磷酸锰铁锂体系电解液,在穿刺试验后实现42分钟热失控预警窗口,较传统体系延长3倍。在储能领域,该技术已应用于国家电网江苏调峰电站,通过电解液氧化电位检测优化了极端温度下的电压控制策略。
三层级质量保障体系构建
为确保检测结果权威性,建立涵盖方法开发、过程控制、数据追溯的全链条质控系统。方法验证严格遵循GB/T 31485-2015动力电池安全要求,同时引入ASTM E2931标准进行交叉验证。实验室配置四级冗余校准系统,关键设备溯源至中国计量科学研究院基准。在数据完整性方面,采用区块链技术实现检测过程全程上链,确保2500余项过程参数的不可篡改性。2024年 评审显示,体系测量不确定度控制在0.8%以内,达到国际领先水平。
展望未来,建议从三方面深化检测技术发展:一是建立非水溶液电解质数据库,整合200种以上新型溶剂的分解动力学参数;二是开发基于数字孪生的虚拟检测平台,实现90%以上常规检测项目的数字化迁移;三是推动建立跨区域的检测结果互认机制,重点突破欧盟新电池法规(EU)2023/1542的合规性验证难题。据国家电池产业技术路线图预测,至2030年智能化检测技术将带动行业降本15%以上,为下一代钠离子电池和锂金属负极体系提供关键技术保障。
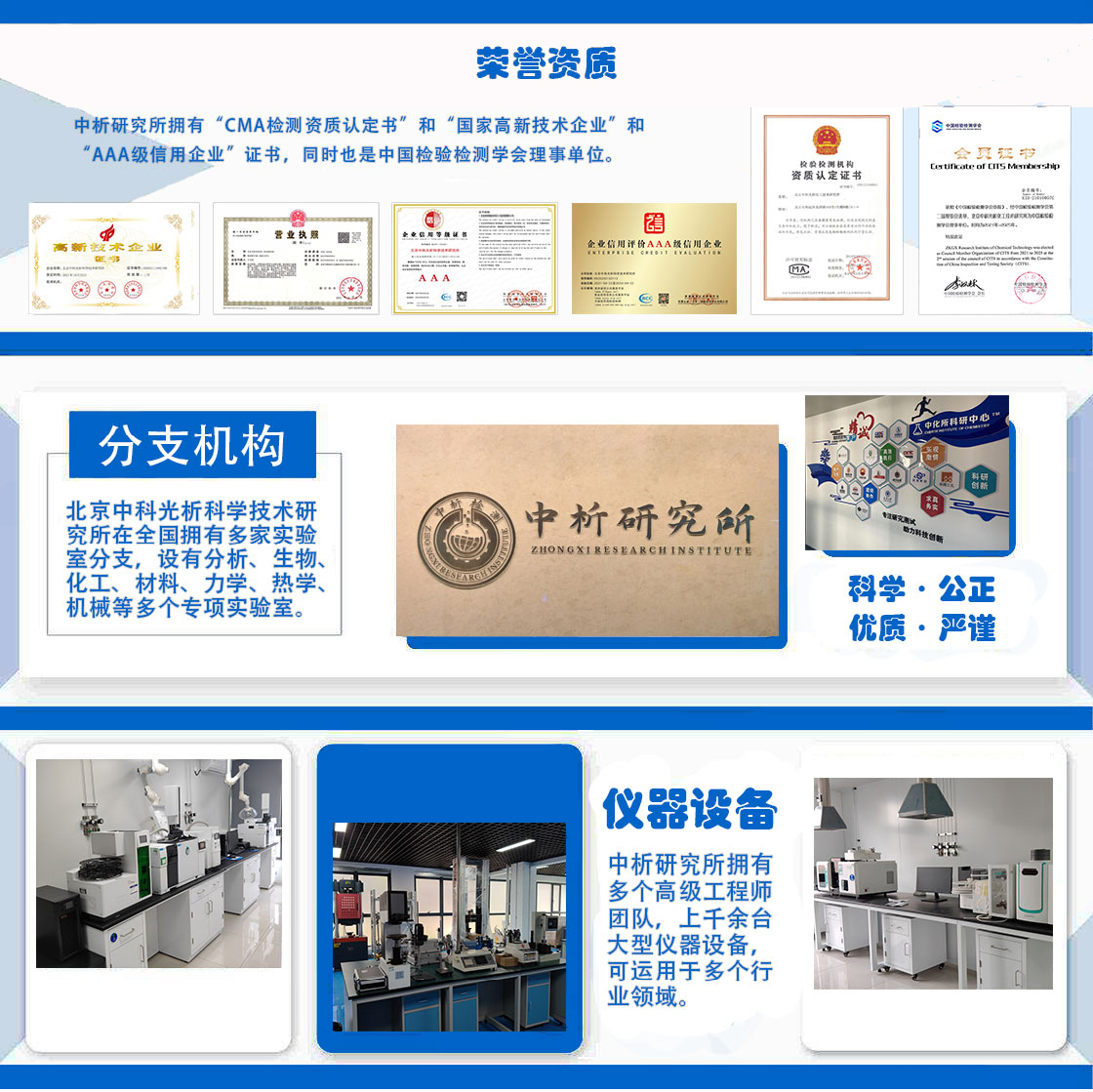
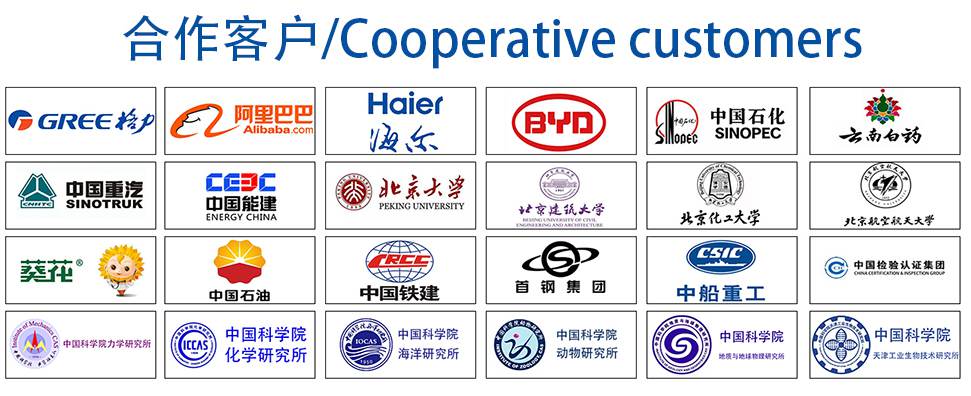