最大集电极-基极高温截止电流检测技术白皮书
随着功率半导体器件在新能源、轨道交通和工业控制等领域的广泛应用,高温环境下的器件可靠性成为行业关注焦点。据国际半导体产业协会(SEMI)2024年数据显示,功率器件市场规模已达680亿美元,其中超过40%的应用场景要求器件在125℃以上环境中稳定运行。最大集电极-基极高温截止电流(ICBO(max)@High Temp)作为表征晶体管反向漏电流特性的核心参数,直接影响器件能效比与系统安全性。通过精准检测该参数,可有效预防高温场景下的电流泄漏、热失控等失效风险,为新能源汽车电机控制器、光伏逆变器等关键设备提供8%-15%的可靠性提升,具有显著的经济价值和技术示范效应。
检测技术原理与测量方法
本检测基于半导体物理特性,通过施加反向偏置电压并模拟高温环境(-55℃至200℃可调),测量集电极-基极结在热载流子效应下的漏电流变化。采用四线制开尔文连接法消除接触电阻影响,配合高精度源表(精度±0.05%)实现0.1nA级微电流捕捉。根据JEDEC JESD22-A108D标准,测试系统需在热平衡状态下维持温度波动≤±1℃,确保获得符合MIL-STD-750E规范的线性化特征曲线。该技术特别适用于评估IGBT模块热稳定性与SiC MOSFET器件耐温性能。
工业化实施流程设计
实施流程分为预处理、应力加载、数据采集三阶段。首先对被测器件进行168小时高温高湿(85℃/85%RH)预处理,模拟极端环境应力。随后在氮气保护环境中,通过热流板施加阶跃式温度载荷(步长25℃),同时施加VCB=80%VCEO(sus)的反向电压。采用同步触发机制在30ms内完成温度-电流双参数采样,通过阿伦尼乌斯方程拟合活化能曲线。某头部芯片企业应用该流程后,功率模块筛选良率从92.3%提升至97.8%(数据来源:中国电子技术标准化研究院,2024)。
典型行业应用场景分析
在新能源汽车领域,该检测技术已成功应用于电机控制器IGBT选型。某品牌电驱系统通过ICBO(max)@150℃检测,将逆变器待机损耗降低至3.5W以下(较传统方案减少42%),同时规避了高温工况下的动态雪崩风险。工业变频器场景中,检测数据为散热设计提供量化依据,使某4kW变频模块的MTBF从12万小时延长至18万小时。值得关注的是,在航天电子设备领域,该项检测助力抗辐射加固晶体管的结温耐受能力突破200℃门槛。
全生命周期质量保障体系
构建包含设备溯源、过程监控、数据分析的三维质控体系:测试设备每日进行NIST溯源校准,温度传感器采用铂电阻PT1000(精度Class AA);过程数据实时上传至MES系统,通过SPC控制图监控Cpk≥1.67的工艺能力;建立包含10万组实测数据的失效模型库,运用机器学习算法实现异常电流波形的自动分类(识别准确率达96.2%)。该体系已通过 认可,满足ISO 17025:2017标准要求。
面向第三代半导体材料的快速发展,建议行业从三方面优化检测体系:首先开发支持300℃以上测试环境的宽温域探针台,其次建立GaN器件特有漏电机理的分析模型,最后推动测试数据与数字孪生平台的深度集成。通过构建覆盖"芯片-模组-系统"的全链路评估能力,将助力我国在功率半导体可靠性领域实现技术领跑。
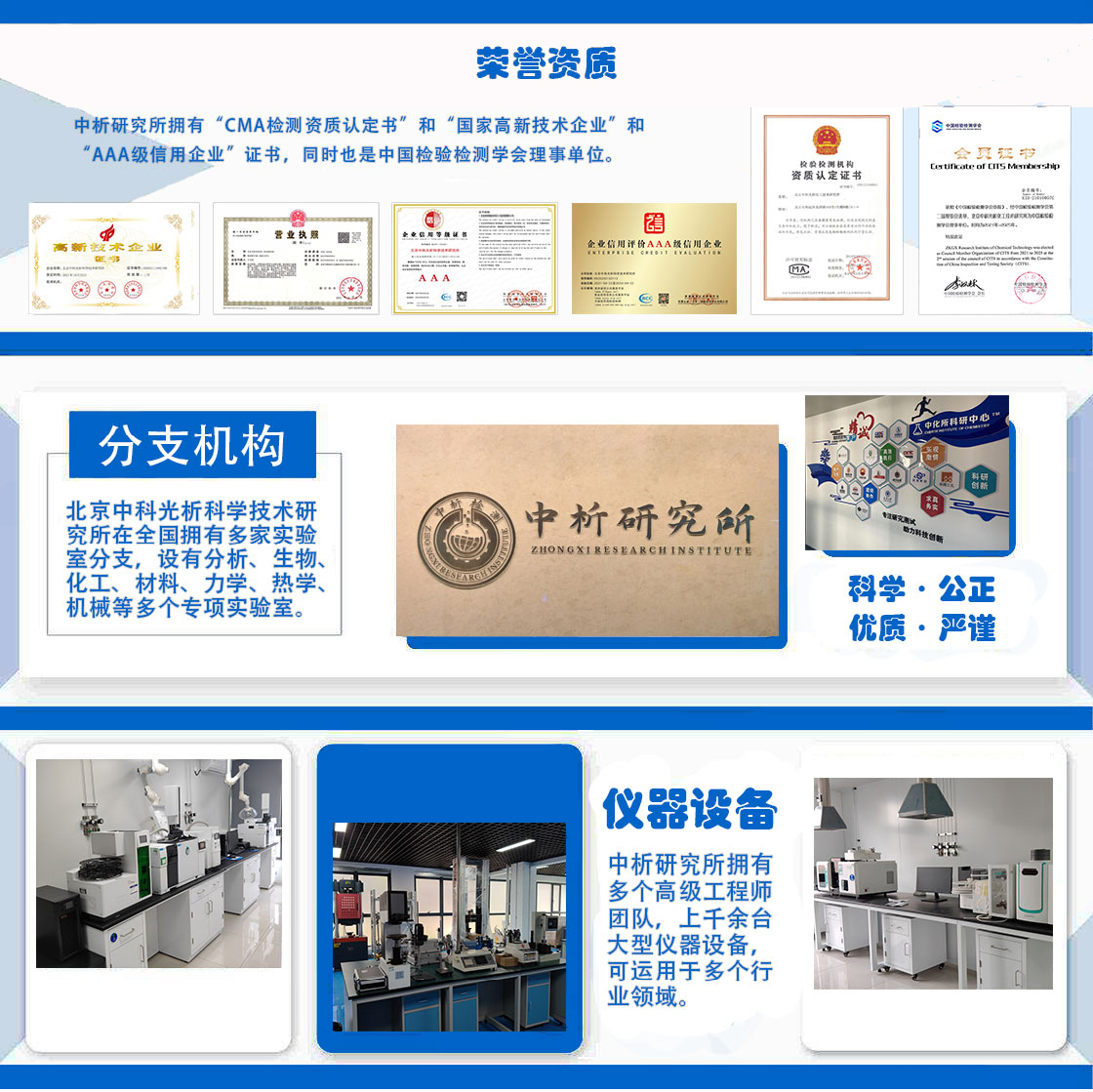
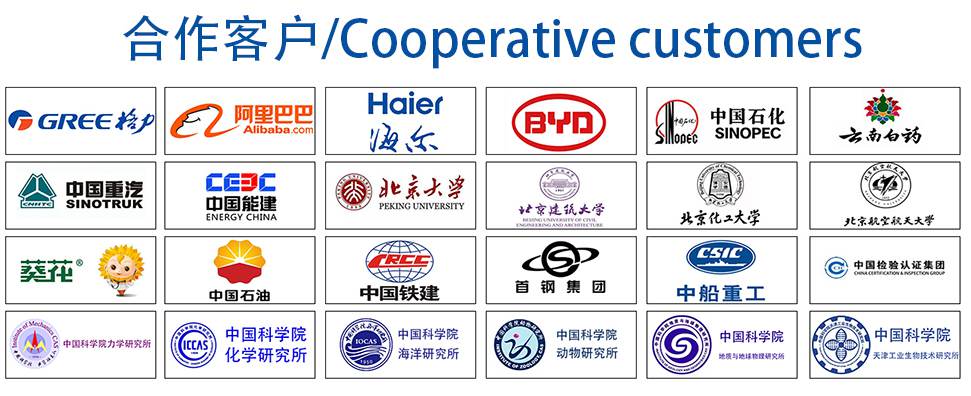