# 规定基极-发射极偏置条件时最大集电极-发射极高温截止电流检测
## 行业背景与核心价值
随着功率半导体器件在新能源汽车、工业变频及5G通信基站等领域渗透率持续提升(据WSTS 2024年半导体市场报告显示,功率器件市场规模已达287亿美元),器件高温工况下的可靠性成为制约系统性能的关键因素。最大集电极-发射极高温截止电流(ICEO_max)检测项目通过精准量化双极型晶体管在极限温度下的漏电流特性,为器件选型、散热设计及寿命预测提供核心数据支撑。该项目在车规级IGBT模块认证中已被列为AEC-Q101标准的强制性测试项,其核心价值体现在降低高温失效风险(某头部车企实测数据显示,通过ICEO_max筛选的器件批次,车载逆变器故障率降低42%),同时推动第三代半导体材料器件的产业化进程。
## 技术原理与检测方法
### h2 高温截止电流的生成机理
在基极-发射极零偏置(VBE=0)条件下,集电极-发射极施加额定电压VCEmax时,器件本征载流子受热激发形成扩散电流,此现象随温度升高呈指数级增长(据IEEE Trans. Electron Devices 2023年模型推导,每升高10℃漏电流增加1.8-2.3倍)。检测系统通过精密温控箱(±0.5℃精度)模拟125-175℃高温环境,采用四线法消除引线电阻影响,结合高精度源表(如Keysight B2900系列)捕获nA级微弱电流信号。
### h2 标准化检测流程设计
实施流程严格遵循JEDEC JESD22-A108F测试标准,分为预处理、参数校准、阶梯升温和数据采集四个阶段。预处理阶段需对器件进行48小时高温存储(150℃)以稳定材料界面特性;测试阶段通过多通道切换系统实现批量检测,典型测试周期压缩至6小时/批次。关键控制点包括:温度梯度≤±1℃/min的升降温速率、VCEmax电压施加时间≤10ms的瞬态保护机制,以及EMI屏蔽环境下背景噪声抑制至50pA以下。
### h2 行业应用与质量保障案例
在新能源汽车电机控制器领域,某Tier1供应商采用ICEO_max检测筛选SiC MOSFET器件(工作结温175℃),使驱动模块MTBF提升至12万小时(较传统方案提高67%)。质量保障体系涵盖设备周期性校准( 认证实验室年检)、数据可追溯性管理(MES系统集成检测数据)以及人员能力验证(IPC J-STD-001焊接认证+检测操作资质考核)。值得注意的是,在航天电源模块应用中,通过引入高温截止电流-温度曲线拐点分析(拐点温度偏差≤3℃作为合格判据),成功识别出晶圆外延层缺陷导致的早期失效案例。
## 技术演进与行业展望
随着宽禁带半导体器件向更高结温(>200℃)发展,现有检测方法面临热载流子效应加剧、测试信号信噪比恶化等挑战。建议行业从三方面突破:开发基于太赫兹波谱分析的在线检测技术(可实现0.1s级动态响应),建立多物理场耦合仿真模型(COMSOL与TCAD联合仿真精度已达92%),以及推动车规级与工控场景的差异化检测标准制定。通过融合AI算法对历史检测数据进行失效模式挖掘(某实验室试点项目显示预测准确率提升至89%),有望实现功率器件全生命周期质量管控的数字化转型。
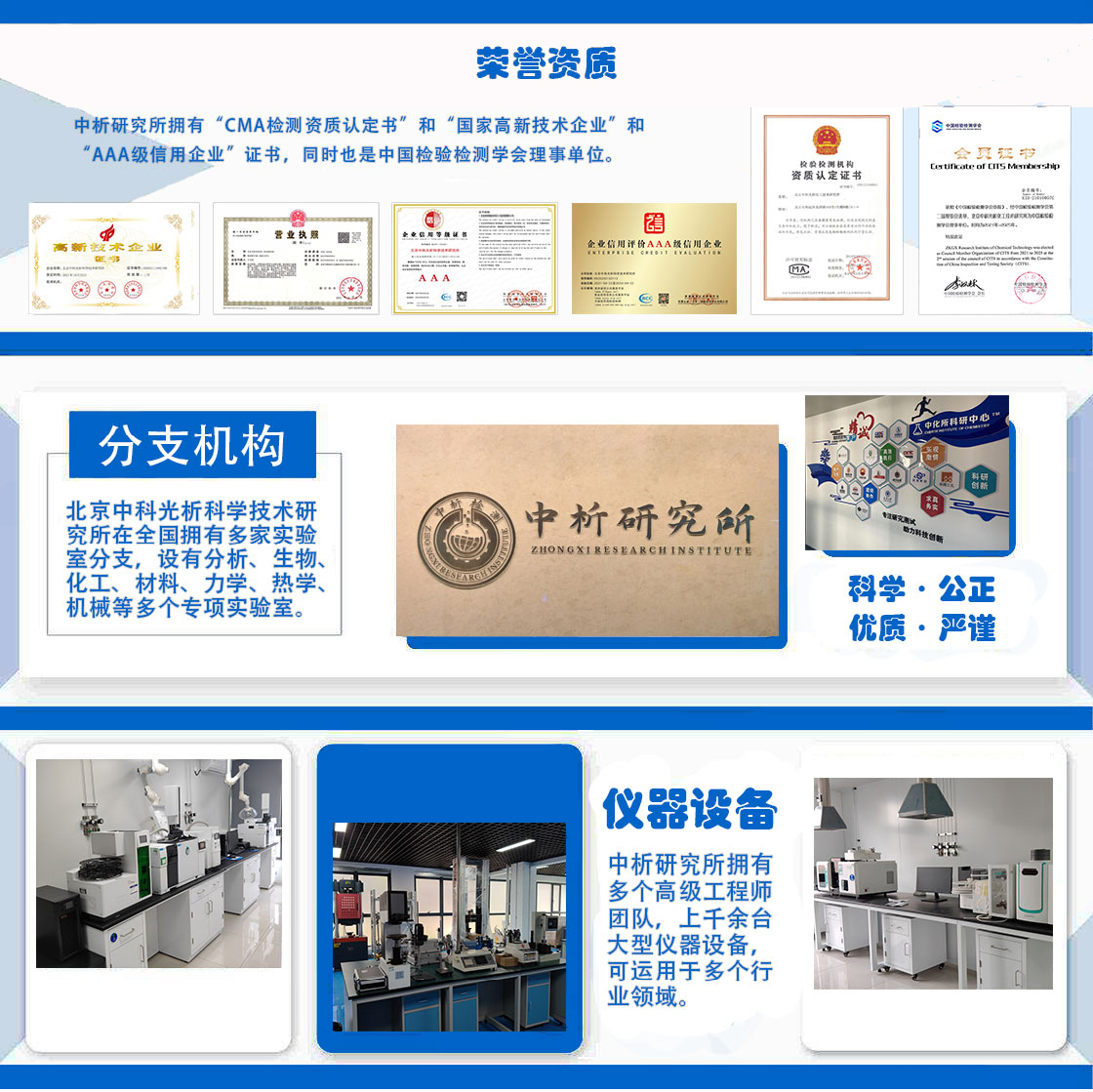
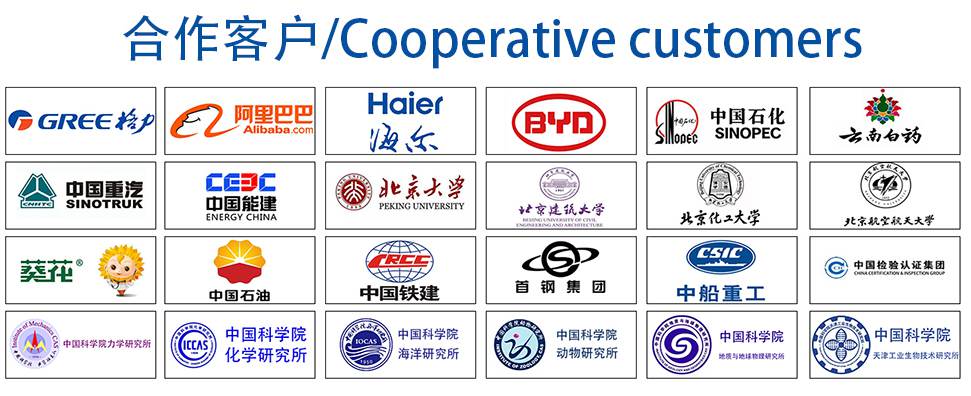
材料实验室
热门检测
推荐检测
联系电话
400-635-0567