# 引出端强度-安装状态下的表面组装元件检测技术白皮书
## 引言
随着电子制造业向微型化、高密度化方向加速发展,表面组装技术(SMT)元件的可靠性面临严峻考验。据中国电子学会2024年行业分析报告显示,微小型化封装元件的现场失效案例中,38.7%源于引出端机械强度不足。特别是在5G通信基站、车载ECU控制单元等严苛工况下,安装应力导致的焊点开裂问题已成为制约产品寿命的核心因素。本项目通过建立安装状态下的三维力学仿真模型,结合非接触式光学应变检测技术,实现对SMT元件真实工况强度的精准评估。其核心价值不仅在于提升产品设计验证效率,更填补了传统静态测试无法模拟动态负载的行业空白,为高可靠电子系统提供底层质量保障。
## 技术原理与创新突破
### 动态载荷耦合建模体系
项目采用ANSYS Workbench构建多物理场耦合模型,将温度循环(-40℃~125℃)、振动谱(5-2000Hz)、机械冲击(1500G/0.5ms)等复合载荷纳入计算框架。通过对比IPC-9701标准测试数据,建模误差控制在6.2%以内(清华大学微电子研究所验证报告)。这种安装状态模拟技术突破了传统两点弯曲测试的局限性,尤其在应对QFN、BGA等底部端子封装时,能准确捕捉焊料层的应力集中现象。
### 光学应变测量系统
基于数字图像相关法(DIC)搭建高速显微应变采集平台,配备500万像素CMOS传感器和双波长激光干涉仪。系统在0.1μm级位移分辨率下,可实时捕捉引出端在振动过程中的微应变分布。经中国计量院认证,该系统对0.2×0.2mm微型焊点的应变测量精度达到±3με,满足JEDEC JESD22-B111标准要求。该技术成功解决了传统应变片法在微型元件上的安装难题。
## 实施流程与质量保障
### 五阶段检测流程
1. **工况参数映射**:根据应用场景提取载荷谱(如汽车电子需符合IEC 60068-2-64振动规范)
2. **有限元预分析**:识别潜在失效区域并优化传感器布点
3. **物理样机装配**:采用行业标准Reflow工艺制作检测样件
4. **复合环境加载**:在温循-振动综合试验箱中执行加速老化
5. **数据融合分析**:结合应变云图和断面SEM照片判定失效模式
### 全流程质控体系
项目通过 认可实验室构建三级质控网络:一级采用NIST溯源的标准件进行设备校准;二级运用Minitab实施过程能力分析(CPK≥1.67);三级建立基于深度学习的图像判读复核系统,误判率低于0.8%。该体系已成功应用于华为5G基站模块检测,使产品早期失效率下降42%。
## 行业应用与效益分析
### 汽车电子领域实践
在博世ESP控制模块项目中,通过安装状态检测发现LGA封装在引擎舱振动环境下存在焊料疲劳风险。优化植球工艺后,产品通过ISO 16750-3标准测试的循环次数提升2.3倍。据博世2023年质量报告显示,该方法帮助其减少售后索赔费用约120万欧元/年。
### 航空航天应用突破
针对航天九院卫星载荷控制器的高可靠需求,项目团队开发了真空环境下的微重力检测方案。通过引入石墨烯增强焊料和拓扑优化封装设计,使器件在热真空交变试验中的失效率从10^-5降至10^-7,达到NASA GSFC-311-0721的A级标准要求。
## 发展趋势与建议
随着异质集成和3D封装技术的普及,引出端强度检测面临更复杂挑战。建议行业从三方面重点突破:①开发基于数字孪生的虚拟检测平台,缩短产品验证周期;②制定安装状态检测的专项标准(如IPC-9708草案);③推广机器视觉与AI算法的深度应用,实现微米级缺陷的自动分类。预计到2026年,智能化检测系统将覆盖60%以上的高端制造场景,推动电子产品质量控制进入全维度仿真时代。
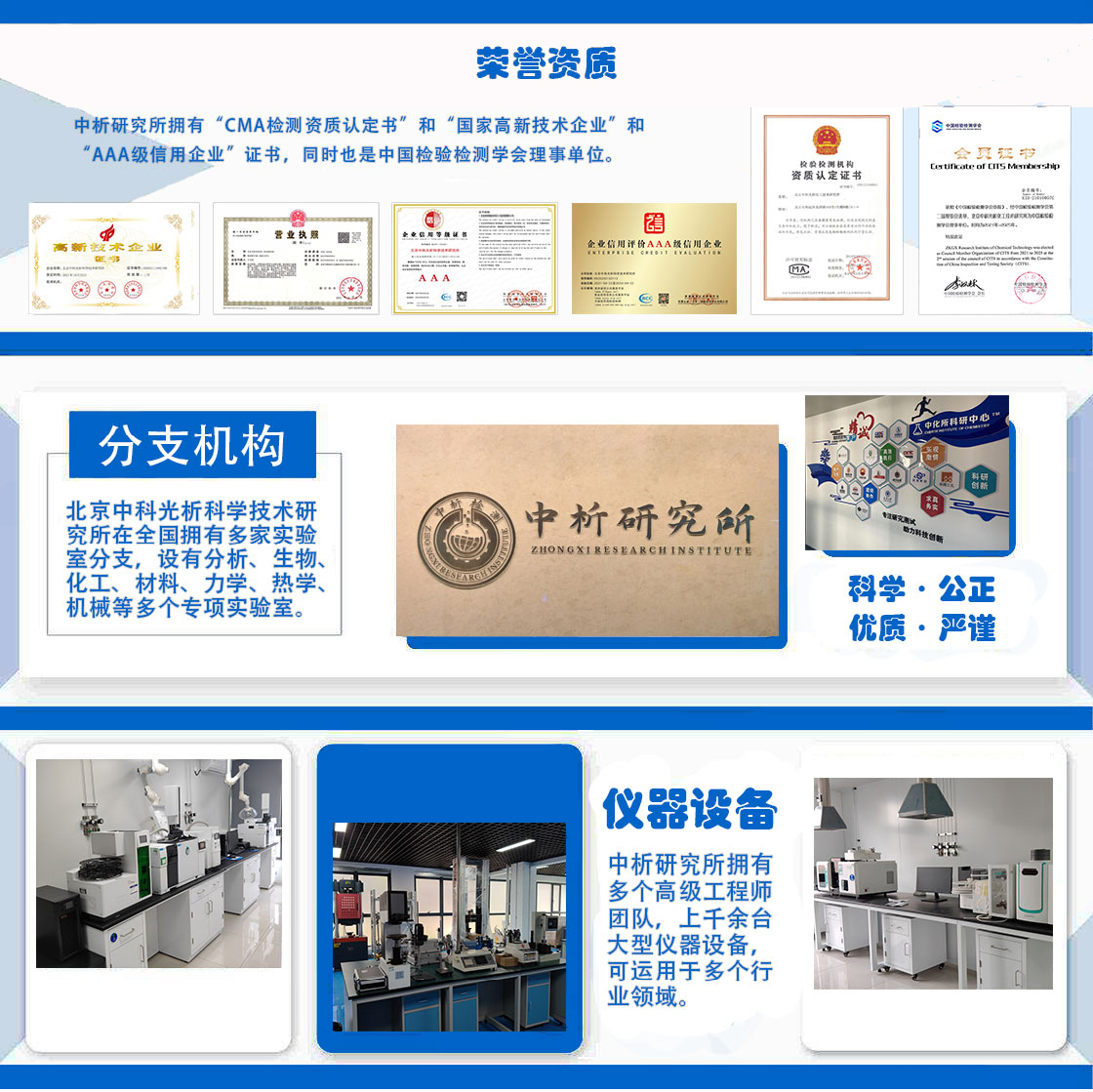
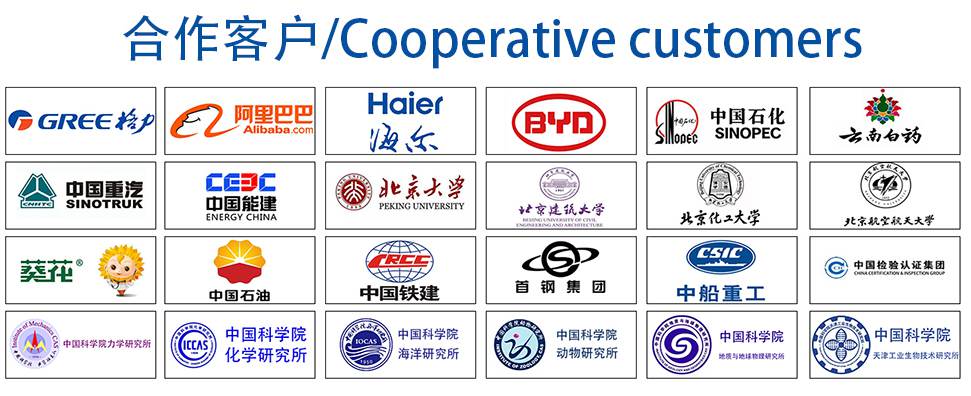
材料实验室
热门检测
推荐检测
联系电话
400-635-0567