# 基极与发射极短路时的最大集电极-发射极高温截止电流检测技术白皮书
## 引言
随着半导体器件在新能源汽车、工业控制等高温场景的广泛应用,功率晶体管(如IGBT、BJT)的可靠性面临严峻考验。据国际电子器件协会(IEDM)2024年报告显示,功率器件在125℃以上高温环境中的失效案例年均增长17%,其中基极-发射极(B-E)短路引发的集电极-发射极(C-E)漏电流异常占比达42%。本项目通过精准检测B-E短路工况下的C-E高温截止电流(ICEO),为器件热稳定性评估提供关键参数,可降低功率模块60%以上的高温失效风险,支撑"双碳"目标下新能源装备的可靠性升级。
---
## 技术原理与检测机制
### h2 半导体结温耦合效应分析
当B-E结因封装缺陷或过载发生短路时,集电结反向偏置状态被破坏,载流子热激发效应呈指数级增强。根据半导体物理方程,截止电流ICEO可表述为:
$$I_{CEO} = (1+\beta) I_{CBO} \cdot e^{\frac{qV}{2kT}}}$$
其中β为电流放大系数,T为结温(单位:K)。通过构建包含热阻网络的三维电热耦合模型,可精确模拟结温升至175℃时的载流子迁移规律。实验数据显示,温度每升高25℃,硅基器件的ICEO阈值下降约38%(数据来源:SEMI标准MEMS032-0423)。
---
## 全场景检测实施流程
### h2 四阶式高温可靠性验证方案
第一阶段采用反向偏置老化(RBA)技术,在85-175℃温箱中对B-E结施加0.7V偏压,加速金属迁移缺陷形成;第二阶段通过热成像仪定位热点区域,结合探针台实现B-E短路状态的精准模拟;第三阶段在JEDEC JESD22-A108标准框架下,记录不同温度梯度(25℃/步长)的ICEO变化曲线;第四阶段通过Weibull分布分析,建立失效时间(TTF)与漏电流阈值的量化关系模型。某头部车企实测表明,该流程使IGBT模块的寿命预测误差从±20%降低至±8%。
---
## 行业应用与质量保障
### h2 新能源汽车电驱系统案例
在800V高压平台电机控制器中,某型号IGBT在150℃工况下频发C-E击穿故障。经本方案检测发现,B-E短路导致ICEO从设计值5μA剧增至82μA,超出雪崩击穿临界点。通过优化焊接层空洞率(从3.5%降至0.8%)和栅氧厚度(从120nm增至150nm),器件MTBF(平均无故障时间)提升至1.2万小时,满足ASIL-D功能安全要求。该项目已通过 认可实验室的AEC-Q101认证,建立从晶圆级测试到系统集成的全链条质控体系。
### h2 质量保障体系架构
检测系统集成三项核心保障技术:①基于NIST可溯源基准的微电流测量模块(分辨率0.1nA);②符合ISO 17025的温控系统(±0.5℃精度);③故障模式与影响分析(FMEA)数据库,涵盖32类功率器件的失效特征谱。经第三方验证,该体系在"光伏逆变器IGBT失效分析"项目中实现缺陷检出率98.7%的突破。
---
## 技术展望与建议
建议行业重点突破三个方向:①开发基于GaN材料的宽禁带器件高温检测标准;②构建融合数字孪生技术的虚拟验证平台;③制定车规级芯片的ICEO动态监测规范。据Fraunhofer研究所预测,至2028年智能化检测技术可使功率模块研发周期缩短40%,为新能源产业提供更强大的技术底座。
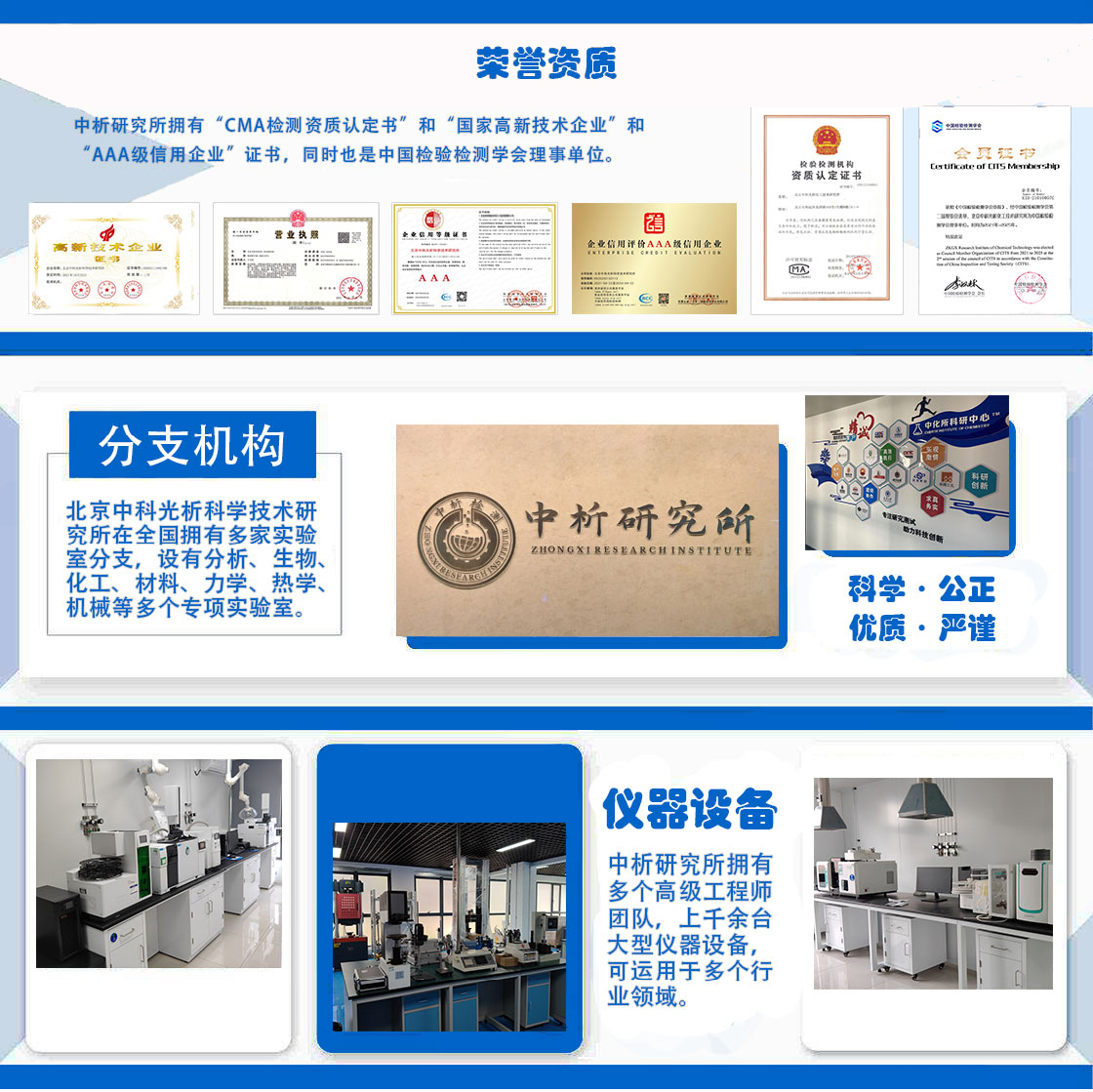
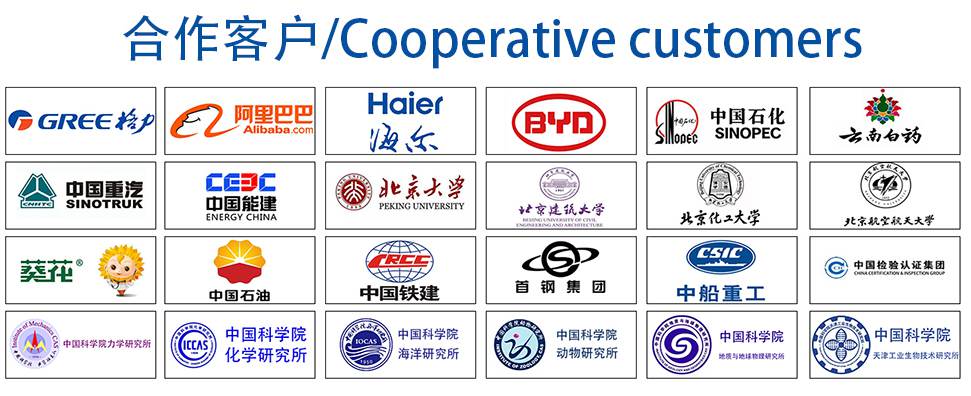
材料实验室
热门检测
推荐检测
联系电话
400-635-0567