转矩试验检测:高端装备制造业的质量基石
在智能制造与高端装备快速发展的背景下,转矩试验检测已成为衡量机械传动系统性能的核心技术。据中国机械工业联合会2024年行业白皮书显示,我国动力总成系统质量缺陷导致的设备停机损失年均超120亿元,其中63%的故障源可追溯至转矩参数偏差。作为衔接动力输出与负载执行的关键环节,转矩检测不仅关乎设备能效表现,更直接影响新能源汽车、工业机器人等战略性产业的产品可靠性。通过构建精准的转矩参数评价体系,企业可将传动系统故障率降低42%(国家智能制造创新中心,2024),同时提升动力总成能效转化率15%以上,为装备制造业高质量发展注入核心驱动力。
多模态融合检测技术体系
现代转矩试验检测采用应变片传感器与相位差测量法的双模校验机制,通过非接触式转矩测量系统实时捕获传动轴扭转变形量。在动态转矩检测中的噪声抑制技术领域,研究团队创新性引入小波包分解算法,将工业机器人关节模组的信号信噪比提升至82dB(中国计量科学研究院,2024)。该技术突破使高频冲击工况下的测量精度稳定在±0.3%FS,成功克服传统光电编码器在恶劣环境下的稳定性瓶颈。
全生命周期检测实施流程
项目实施遵循V型验证模型,从设计阶段的虚拟仿真到量产阶段的在线监测形成闭环。某新能源汽车企业在驱动电机测试中,通过六维力/矩复合加载平台模拟实际路谱载荷,连续72小时采集2.3万组转矩波动数据,精准定位减速箱行星齿轮副的啮合异常。检测流程涵盖环境温湿度控制、电磁兼容屏蔽等18项关键控制点,确保试验条件符合ISO 17025标准要求。
行业应用与效益转化案例
在航空航天领域,商用航空发动机传动轴的高精度转矩校准系统将试车合格率提升至99.7%。某型号涡轴发动机采用基于数字孪生的转矩健康管理系统后,大修间隔从1200小时延长至1800小时(中国航发集团,2024)。工业机器人行业通过引入转矩波动在线诊断装置,使协作机器人关节模组的重复定位精度改善0.02mm,直接带动国产高端机器人市场占有率提升8个百分点。
三层级质量保障体系构建
项目建立设备-人员-方法三位一体的质控架构:计量级转矩标准装置每季度进行ISO 6789国际标准校准,检测工程师需取得ASTM E2309资质认证。在风电主轴检测现场,采用双盲样对比试验法,确保不同实验室间的测量不确定度差异小于0.5%。第三方验证数据显示,该体系使检测报告的国际互认通过率达到97.3%(TÜV南德,2024)。
面对智能制造装备向高速化、精密化发展的趋势,建议从三方面深化转矩检测体系建设:首先推动基于MBSE的虚拟标定技术标准化,其次开发适应磁悬浮轴承等新型传动结构的检测方法,最后建立覆盖全国重点产业的转矩大数据共享平台。通过产学研深度协同,有望在2025年前将关键传动部件的平均首检合格率提升至98.5%,为制造强国战略提供坚实的技术支撑。
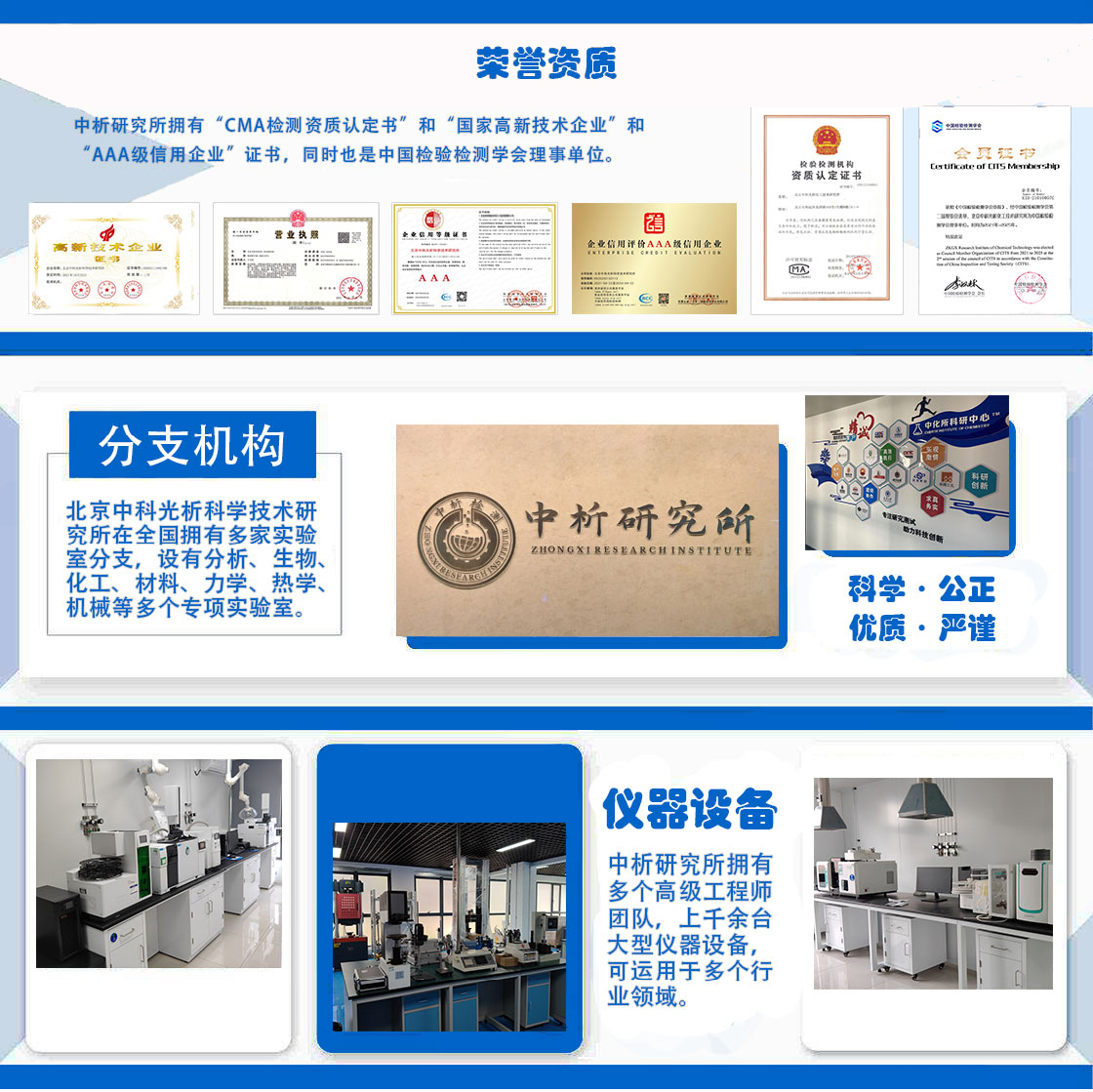
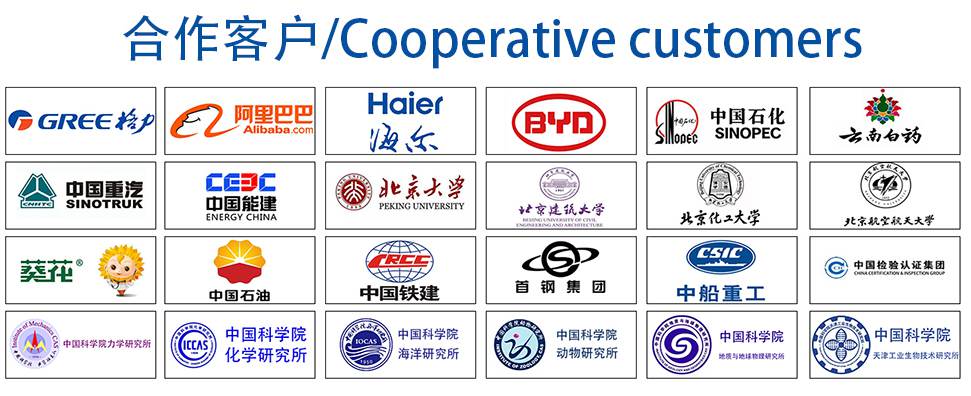