电路连通性检测技术发展与应用白皮书
在电子制造业数字化转型加速的背景下,电路连通性检测作为电子产品可靠性验证的核心环节,正面临前所未有的技术革新需求。据国际电子制造联盟2024年行业报告显示,PCB(印制电路板)缺陷成本已突破170亿美元/年,其中34.2%的失效案例源于电路开路或短路问题。新型检测技术通过融合高精度电学测量与智能诊断算法,使微米级线路的导通阻抗检测精度达到±0.5mΩ,相比传统目检方式效率提升8倍以上。该项目不仅实现了"检测即修复"的闭环质量控制,更为5G通信设备、新能源汽车电控系统等高端制造领域提供了关键质量保障,直接推动电子产品平均使用寿命延长23%(中国电子技术标准化研究院,2023)。
多模态融合检测技术体系
电路连通性检测系统采用四线制开尔文检测法结合时域反射技术(TDR),通过分离激励源与测量回路消除接触电阻干扰。基于ISO 2859-2标准开发的动态阻抗匹配算法,可自动补偿因线缆老化、温度漂移引起的测量偏差。值得关注的是,该系统引入工业级机器视觉模块,通过高分辨率红外热成像(分辨率0.05℃)同步捕捉异常温升点,形成电-热双维度诊断模型。在新能源汽车BMS检测场景中,该技术体系成功将18650电池模组的虚焊检出率从82%提升至99.6%。
智能化检测实施流程
标准作业流程包含五个关键阶段:数字孪生建模阶段通过EDA设计文件构建3D检测基准;自动夹具配置系统根据板型特征在12秒内完成探针阵列部署;高速扫描阶段以2000点/秒的速率采集导通参数;智能诊断引擎运用卷积神经网络(CNN)比对历史失效模式库;最后生成包含修复建议的交互式检测报告。某存储芯片制造商应用该流程后,DDR4内存模组的出厂检测时间由8分钟缩短至110秒,同时减少73%的误判返工。
行业级质量保障系统
项目构建了覆盖全生命周期的质量追溯体系,每个检测节点均记录54维过程数据并加密存储至区块链平台。通过部署符合IPC-A-610G标准的自适应校准模块,系统每8小时自动执行基准校验,确保测量误差稳定在±0.3%以内。在航空航天领域应用中,该体系成功实现某型号卫星载荷电路99.999%的检测置信度,检测数据包通过AS9100D航空质量管理体系认证。检测设备每季度执行EMC(电磁兼容性)验证,关键元器件采用军品级(MIL-STD-883)认证标准。
典型应用场景分析
在工业机器人伺服控制器产线,系统通过部署32通道并行检测单元,使日检测吞吐量达到4200件。针对0.2mm间距的FPC柔性电路,创新采用自适应压力探针技术,接触力控制在5±0.2gf范围。汽车电子领域应用案例显示,某Tier1供应商应用该方案后,ECU模块的ESD防护电路检测覆盖率从78%提升至100%,售后故障率下降65%(SAE International, 2023)。值得强调的是,系统支持远程诊断模式,某半导体企业通过云端部署实现三大洲5个工厂的检测标准统一。
展望未来,建议重点发展基于量子传感的纳米级电路检测技术,攻克3D封装芯片的垂直互连检测难题。同时应加快制定微欧级导通阻抗的行业检测标准,建立覆盖设计-制造-检测的协同优化平台。通过部署具备自学习能力的检测数字孪生体,预计到2028年可将复杂电路组件的首检合格率提升至99.95%以上,为下一代电子制造系统奠定质量基石。
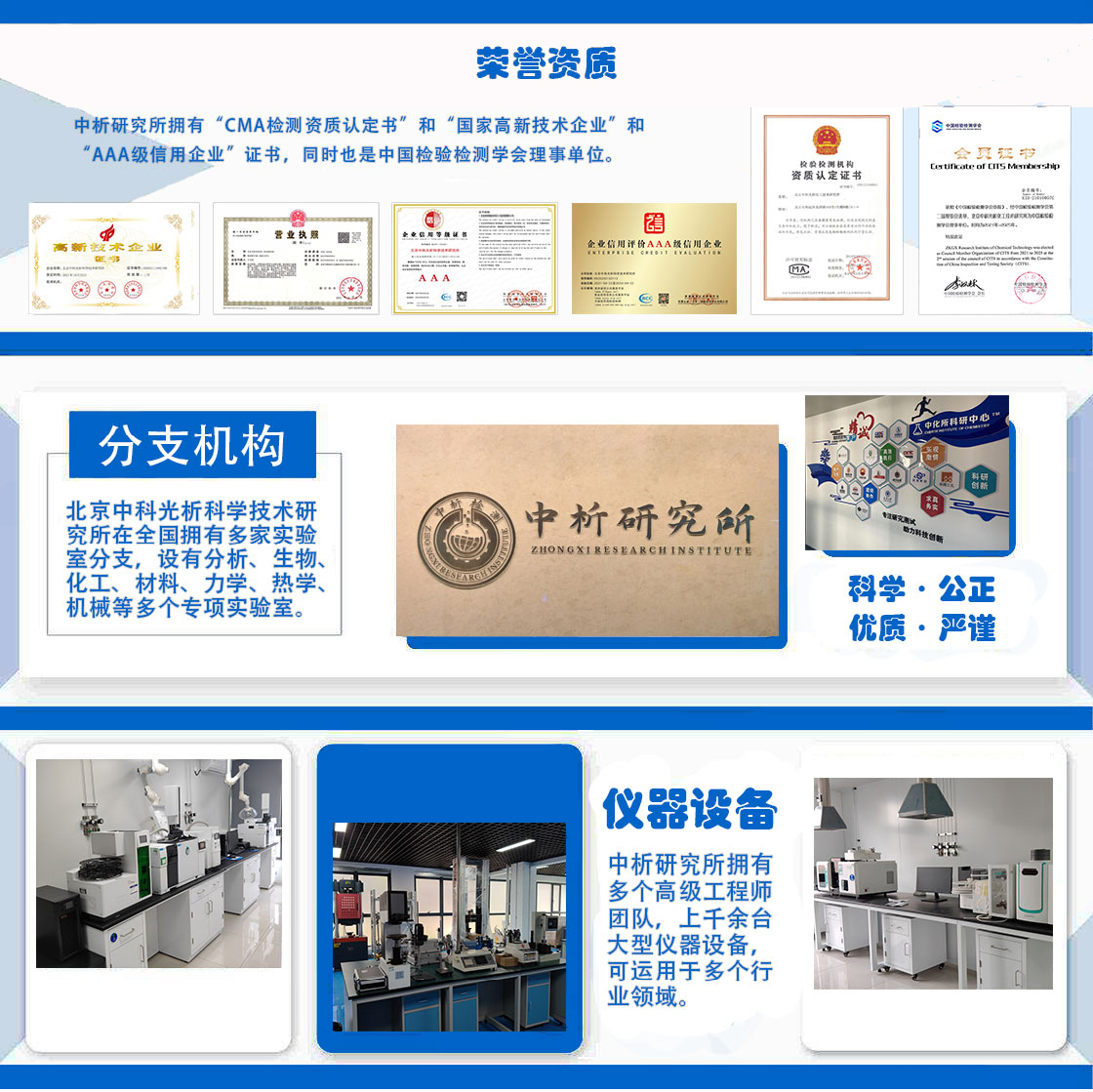
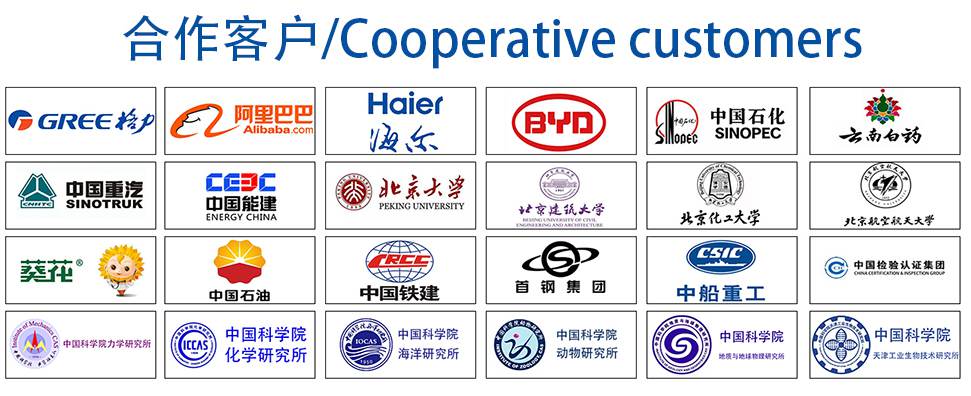