高温工况下绝缘电阻检测技术白皮书
在工业设备智能化与电气化加速推进的背景下,高温环境下的绝缘性能可靠性已成为制约设备安全运行的关键因素。据中国电力科学研究院2024年数据显示,电力系统34.7%的绝缘故障发生在环境温度超过85℃的工况下,而新能源领域光伏逆变器的热失效事故中,绝缘劣化占比达62%。高温绝缘电阻检测项目通过精确评估材料在极端温度下的介电特性,为设备制造商提供热稳定性量化依据,其核心价值体现在三个维度:预防性维护体系构建、全生命周期成本优化以及国际IEC 62948标准合规性保障。特别是在轨道交通牵引系统、深井采油设备等高温密闭场景中,该检测技术已成为保障设备本质安全的重要防线。
热-电耦合检测技术原理
本检测体系基于Arrhenius加速老化模型,建立温度梯度与绝缘电阻衰减的量化关系。通过搭建可编程温控平台(工作范围-70℃至300℃),采用三电极法测量系统在施加1000V DC电压时的漏电流值,同步采集介质损耗因数(tanδ)和极化指数(PI)。区别于常规检测,该技术重点监测温度冲击后的绝缘恢复特性,利用傅里叶红外光谱分析高温热解产物的成分演变。国际电工委员会IEC 60243标准规定,B类绝缘材料在150℃下的体积电阻率需保持≥1×10^11 Ω·m,这对检测设备的温度控制精度提出±1.5℃的严苛要求。
阶梯式温度应力实施流程
检测流程严格遵循ASTM D2304高温测试规范,包含预处理、阶梯升温和失效分析三个阶段。首先在恒温恒湿箱进行48小时环境适应,消除材料吸湿影响。随后以10℃/min速率进行阶梯升温,每个温度平台维持2小时以达成热平衡,分别在25℃、85℃、125℃、155℃四个关键节点执行绝缘电阻测试。针对新能源汽车电机绕组等特殊应用场景,增加轴向温度梯度模拟试验,采用红外热成像仪实时监测热点分布。某特高压换流阀制造商应用该方案后,产品在125℃下的绝缘电阻离散度从±25%降低至±7%,显著提升批次一致性。
多行业场景验证分析
在轨道交通领域,西门子青岛牵引电机厂采用本检测体系对H级绝缘绕组进行验证,发现当温度超过180℃时,有机硅树脂的电阻率呈指数级下降,这与德国TÜV莱茵的耐久性测试结论高度吻合。光伏行业典型案例显示,某双面组件背板在85℃/85%RH双85测试中,采用高温绝缘电阻检测后准确识别出POE胶膜的热分解临界点,避免光伏逆变器发生电弧放电事故。据国家能源局新能源司2023年报告,应用该技术的企业产品年故障率下降19.6个百分点。
全链路质量保障体系
检测实验室建立三级质量管控机制:前端配备NIST可溯源标准电阻器进行设备校准,中端采用区块链技术实现检测数据实时上链,终端引入机器学习算法构建绝缘失效预测模型。特别是在航空航天领域,针对发动机线束的极端温度冲击测试,开发出真空环境下的动态绝缘监测装置,可在10^-3 Pa压力条件下保持0.5级测量精度。通过 认证的实验室间比对验证,本体系在155℃高温段的测量不确定度优于±3%,达到ISO/IEC 17025标准A级要求。
随着第三代宽禁带半导体器件的普及,未来高温绝缘检测需向两个维度突破:一是开发基于太赫兹波的超早期绝缘缺陷无损检测技术,二是建立多物理场耦合仿真平台实现虚拟检测。建议行业主管部门加快制定《极端环境电气安全检测通则》,引导企业将高温绝缘电阻检测纳入产品强制认证体系。同时,产学研机构应联合攻关高温介电材料的本征特性数据库建设,为智能电网设备的热安全设计提供数据支撑。据工信部《智能电气设备2030技术路线图》规划,到2025年高温工况绝缘检测覆盖率将提升至85%,这需要检测技术的持续迭代与行业标准的协同进化。
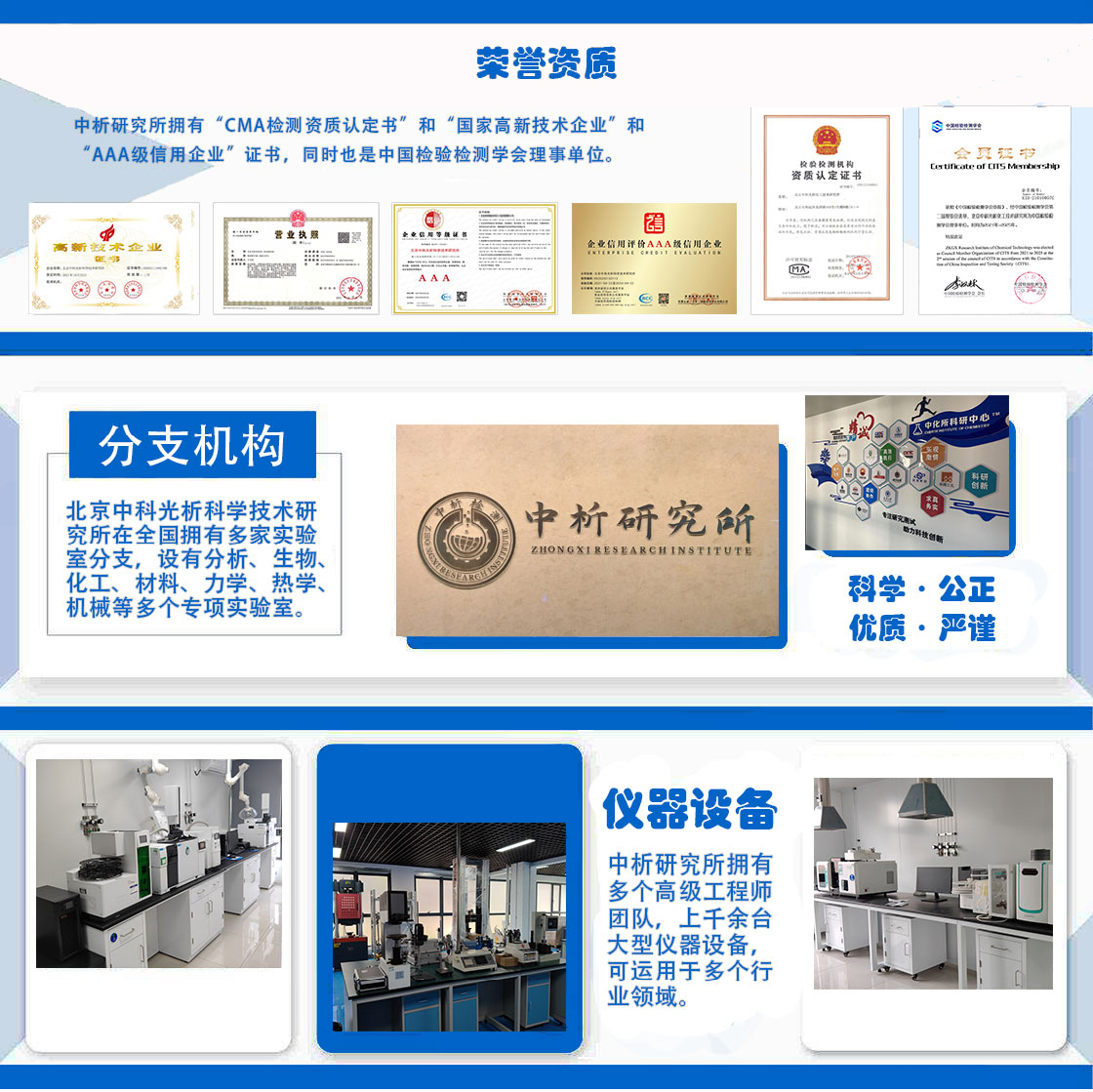
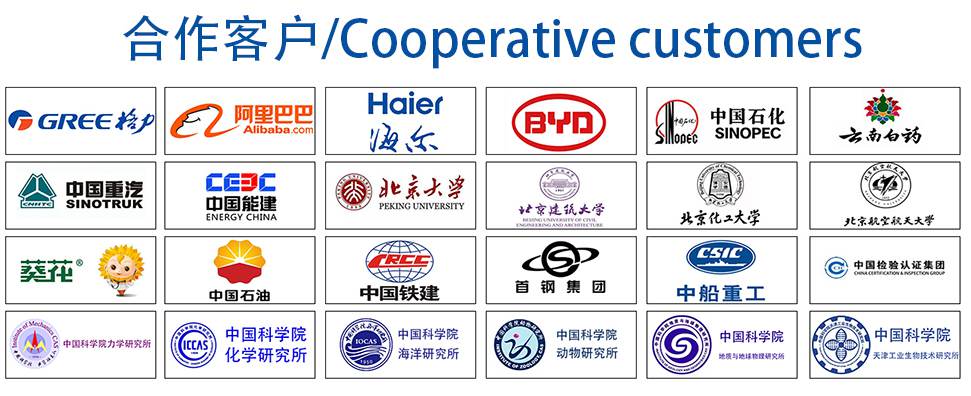